Cooling Systems for Electric Vehicle Powertrains
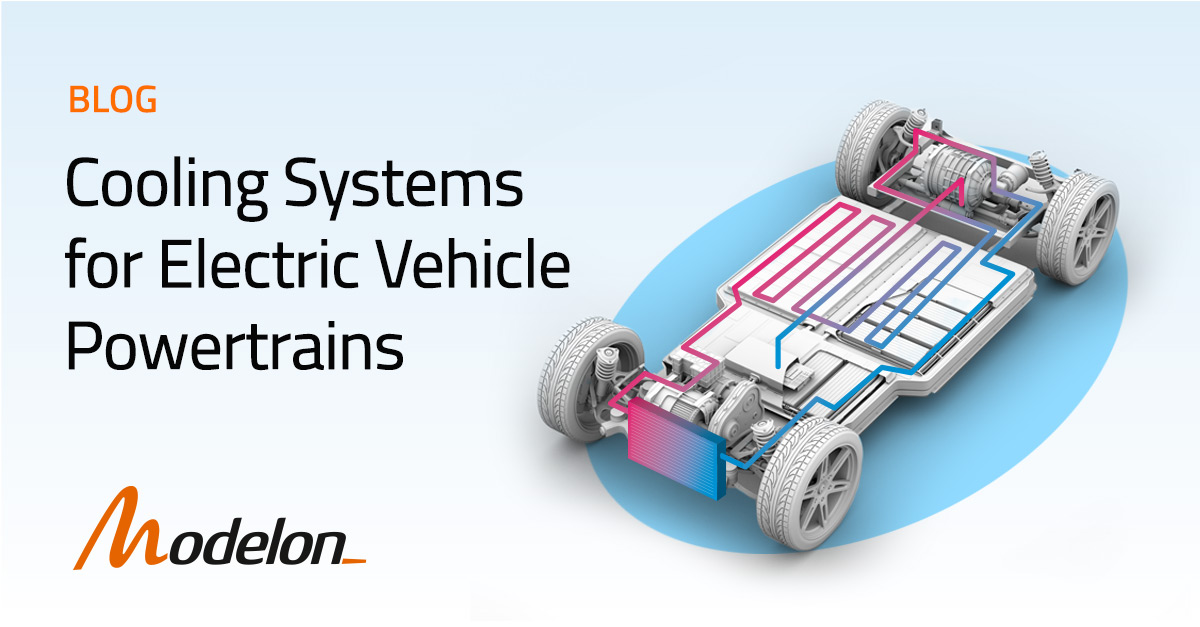
Thermal management for EV powertrains is a crucial capability for key customer attributes such as vehicle performance, range, and comfort. The thermal management system keeps the vehicle batteries, motors, and power electronics operating within each component’s safe and target temperature range. In addition, other components, such as the DC fast charger, e-axles, and steering/brake pumps, also require thermal management.
Increasing energy consumers in EV systems
With the increasing number of components requiring thermal management, EV thermal management systems increased in complexity. There are numerous thermal consumers, each with different temperature requirements. Thermal management includes cooling and heating system components for optimal performance (and sometimes both at the same time, depending on the component and thermal loading).
In addition to the EV powertrain components, the vehicle cabin and its occupants also need proper thermal management. Some of the biggest complaints regarding EV performance are related to cabin heating and air conditioning. Without the excess waste heat from the combustion engine, heating can be especially challenging in EVs. EVs often require PTC heaters to maintain adequate cabin heating performance in cold climates and battery temperatures, which can significantly impact vehicle range.
Developing complex coolant networks for EVs
Traditional heating and cooling loops in automotive powertrains include a coolant loop and a refrigerant loop for climate control. In an EV, integrated thermal management systems that combine the coolant and refrigerant loops are required to provide sufficient cooling for the battery under all ambient conditions. Recent trends in integrated thermal management have shifted to more complex coolant networks with relatively simple refrigerant loops that can allow targeted heating and cooling of the various thermal consumers. The figures below shows common refrigerant loop models, spanning from simple single loops with a single evaporator to dual loop systems with multiple evaporators or an evaporator (or multiple evaporators) and a chiller.
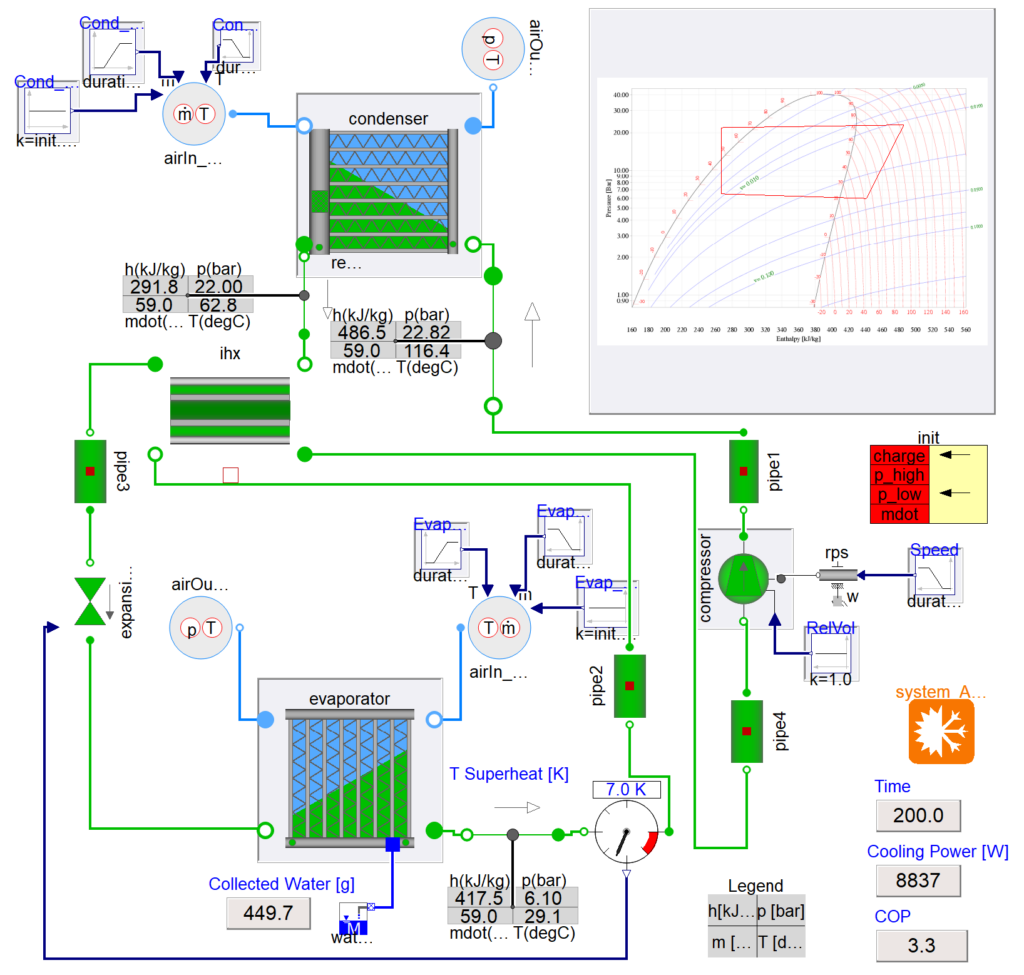
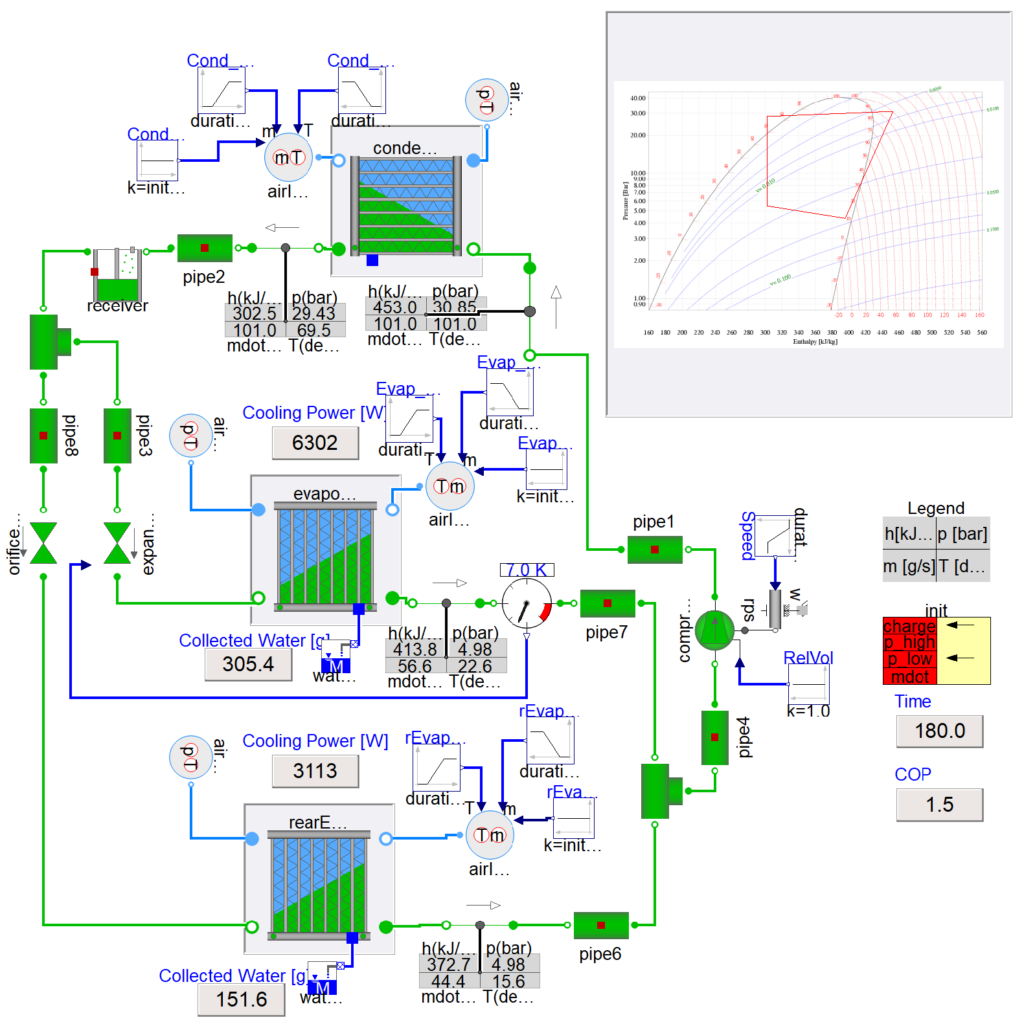
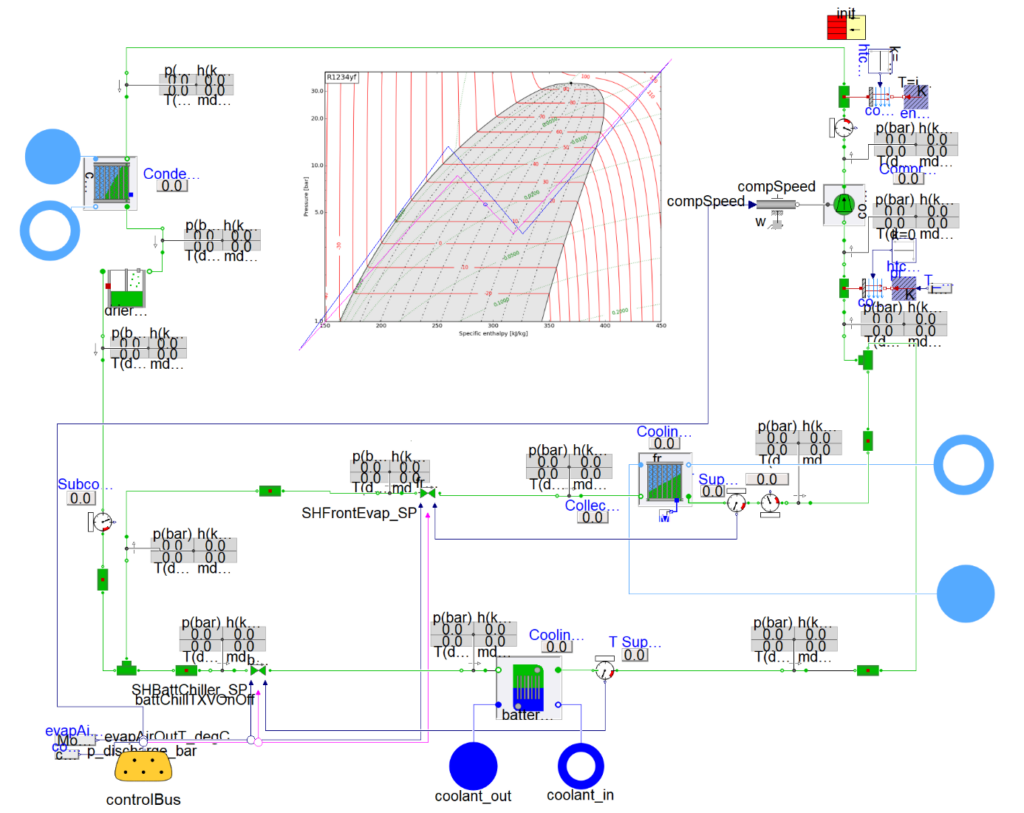
The figure below shows a sample architecture developed by EV Thermal Flow Solutions that illustrates the level of complexity typical in EV thermal management solutions. From an engineering standpoint, separate departments which were responsible for engineering the coolant loop and refrigerant loop are now integrated and working together to deliver an optimized thermal management system. Given the thermal management system’s complexity, there is also a greater need for integration of controls with physical system models.
There are significant benefits to this approach in terms of optimized system performance. With flexible connections between various parts of the system, coolant can be routed to improve system performance and efficiency. For example, heat from the power electronics can be used to heat the battery. Chiller operation can be optimized to deliver the required amount of cooling in conjunction with a coolant-based radiator when ambient conditions are favorable. Flexible system operation with optimized cooling and heating performance can lead to smaller heat exchangers and lower capital costs. Improvements in energy efficiency can directly lead to improved electric vehicle range. We are seeing customers exploring various thermal architectures in a model-based approach to deliver optimized thermal systems, design and size heat exchangers, pumps, valves, and compressors, and assess control strategies over real-world load cycles.
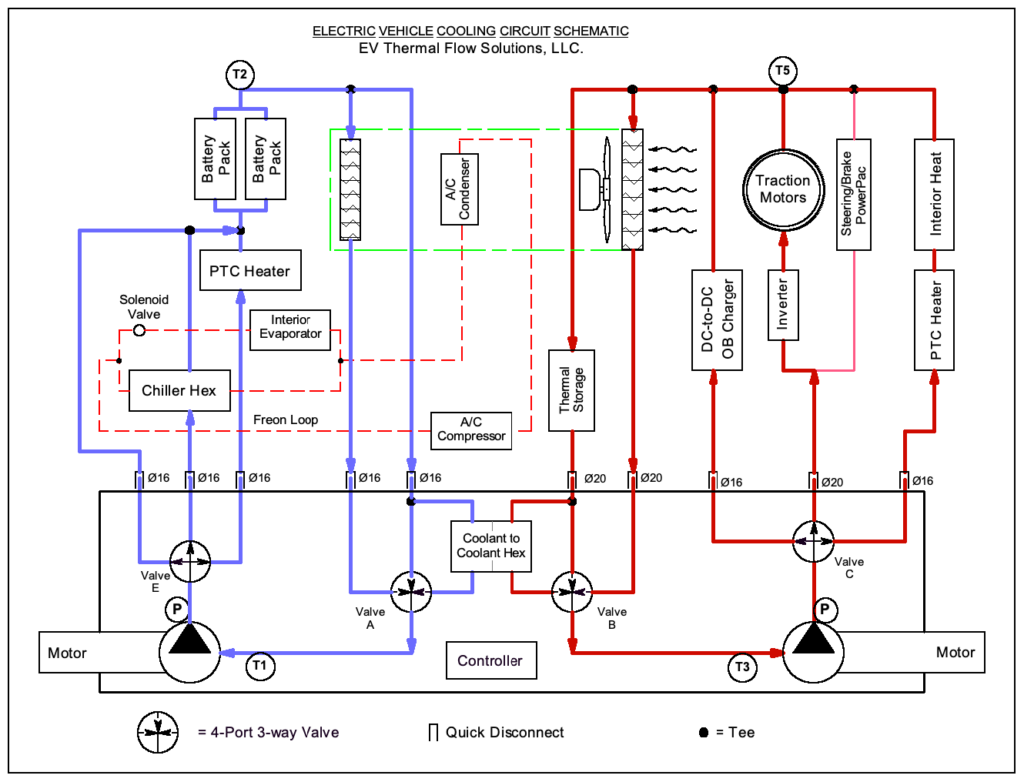
Advanced component libraries for EV thermal management
Modelon thermofluid libraries support model-based development of integrated coolant and refrigerant systems. Air Conditioning Library contains the components to model the refrigerant loop including refrigerant-coolant heat exchangers like chillers. Liquid Cooling Library includes the components to model the coolant loop, while Heat Exchanger Library includes the models for the coolant-air heat exchangers. Batteries from Electrification Library can also be used to capture the electrical and thermal performance of the battery and accurately determine battery thermal losses. To enable the connection between the coolant in Air Conditioning Library and the coolant in Liquid Cooling Library, an adapter is provided. The model below shows a relatively simple integrated system with a separate coolant loop for battery cooling. Results from this model show the impact of battery cooling requirements on the cabin cooling from a hot soak.
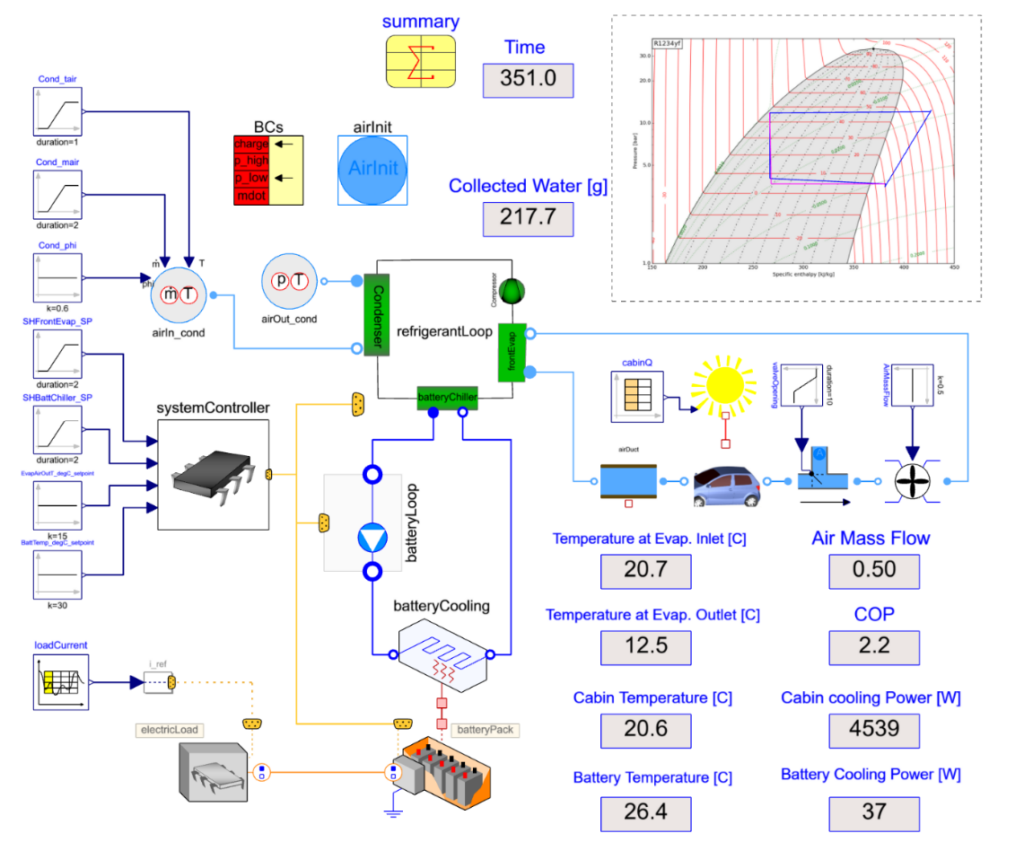
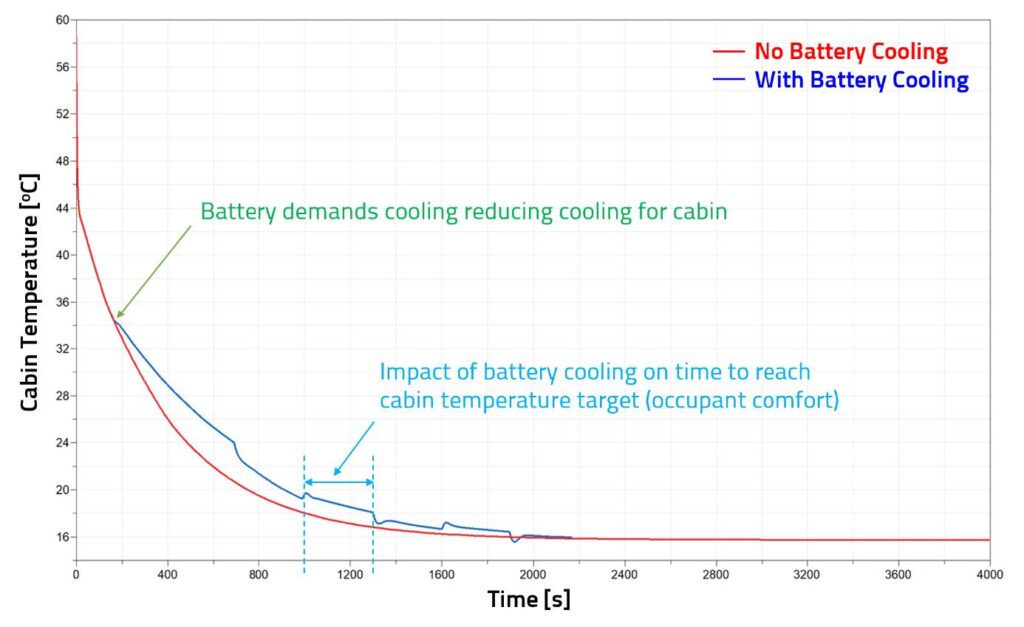
Future enhancements in the Modelon suite of thermofluid libraries aim to streamline the modeling process for these integrated thermal management systems. Chiller and radiator models with coolant compatible with Liquid Cooling are being developed. These models will deliver functionally the same results as the current components in Air Conditioning library but will eliminate the need for the adapters. Examples of integrated systems will also serve as templates for customers to adapt for their work.
Contact our experts to learn more about our libraries and capabilities in modeling cooling systems for EV powertrains.