Predictive Motion Control Considering Body Attitude Constraints for Four in-Wheel Motor Vehicles – IEEE CDC 2023 Winners
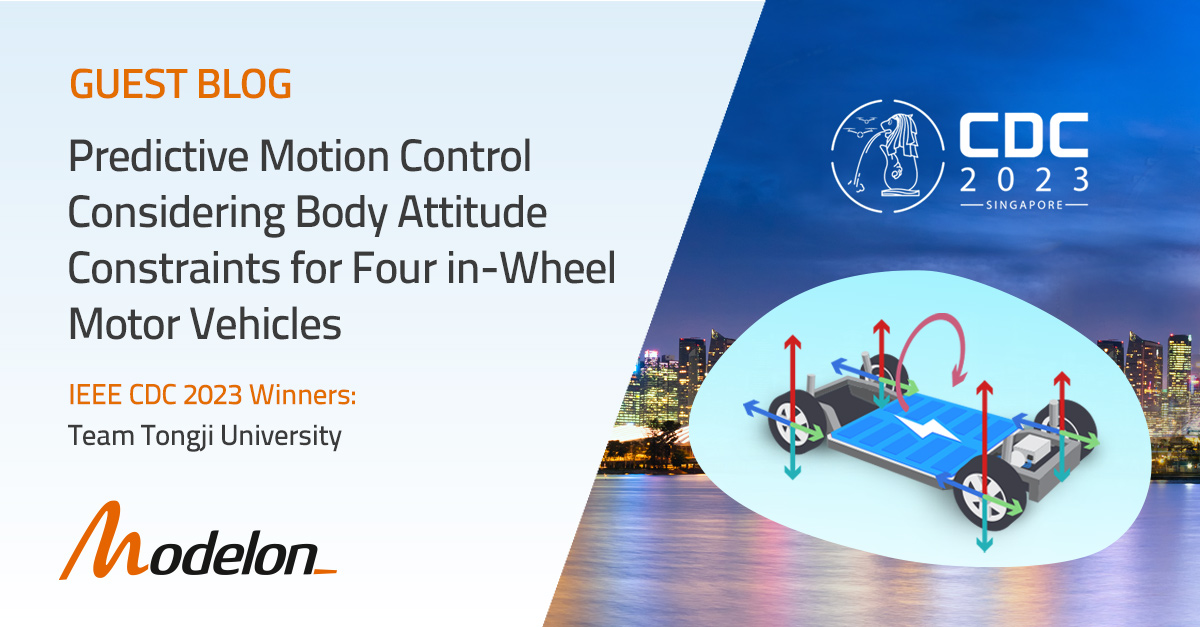
This blog is authored by the IEEE CDC Autonomous Driving Benchmark Control Challenge Gold Award winners from Tongji University, made up of Hongqing Chu, Zongxuan Li, Qiao Kang, Zhenghao Li, Bingzhao Gao, and Hong Chen.
This post details the innovative use of Model Predictive Control (MPC) to develop a controller for a vehicle dynamic system. The proposed controller was developed for the 62nd IEEE Conference on Decision and Control (CDC 2023) Benchmark Challenge for Autonomous Driving Control, and it stood out from fierce competition among dozens of teams, winning the gold award.
The team expresses heartfelt thanks to Modelon for providing an accurate and user-friendly Plant model for algorithm validation in this benchmark competition. Combining Modelon Impact and Mathworks’s Simulink platform makes it easier to leverage the latest developments in control simulations without disrupting current workflows and simplifying the process of modeling the systems. Renowned for their advanced simulation tools, Modelon provides solutions for designing, analyzing, and optimizing complex systems across multiple industries. Their products enable engineers to create highly accurate models of physical systems, allowing seamless integration with various engineering software.
MPC is a proactive control strategy that uses a mathematical model to predict and optimize a system’s future behavior. The effectiveness of MPC heavily relies on the accuracy of its simulation model. A precise model ensures that MPC can accurately forecast future states, allowing optimal control. The integration of Modelon’s advanced simulation capabilities plays a pivotal role in enhancing the performance of MPC. Modelon provides high-fidelity physics-based models so that the intricate dynamics of various systems can be modeled, providing a reliable foundation for controller design and testing.
Outline of the benchmark problem
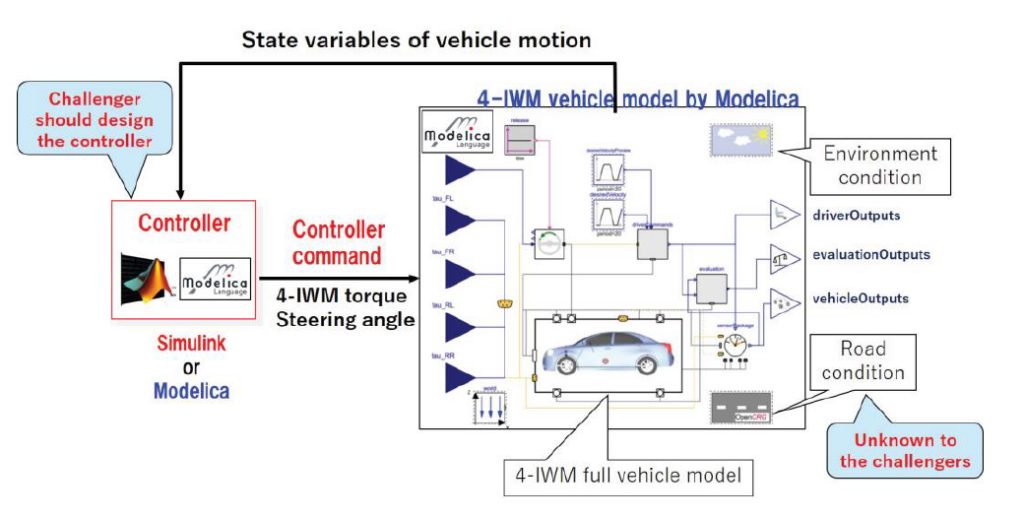
Fig. 1 The Framework of the benchmark problem
The benchmark problem is to control the vehicle dynamics for a 4-wheel IWM vehicle, which can control the driving/braking behavior and the body attitude. The full vehicle model of the 4-IWM vehicle is provided as a Modelica model, including a 3D multibody mechanical model of the suspension and body, an electric model of the battery and motor, and nonlinear tire model. The challengers are requested to design and test a controller of 4-IWM torque and steering angle. There are two tasks to be solved in this benchmark problem:
Problem 1 (Acceleration and braking on a rough, slippery, straight road):
Minimizing deviation from the desired speed profile, body motion (heave, pitch, roll), and energy consumption.
Problem 2 (ISO double lane change on rough road):
Minimizing deviation from the desired course, body motion (heave, pitch, roll), and energy consumption.
The vehicle dynamics model is provided as a Modelica model. The vehicle model consists of a chassis model with a 3-dimensional multibody mechanical system model and power system model of an IWM drive train by electric model. The chassis model includes a 3D multibody mechanical system, featuring front and rear suspension kinematics, body motion, and nonlinear tire characteristics. The power system model comprises a battery system, four in-wheel motor models, and a controller constructed using Modelon’s Electrification Library. The model considers the non-linear characteristics of suspension bushes, steering shaft stiffness, and friction, which are critical for accurate steering behavior. The hierarchical structure of the model allows Modelon Impact to solve simultaneous differential algebraic equations and generate simulation codes automatically. It also enables calculating and plotting of simulation results for each physical variable. The Modelica tool also facilitates the creation of animation results, showcasing the model’s dynamic behavior.
Control Scheme
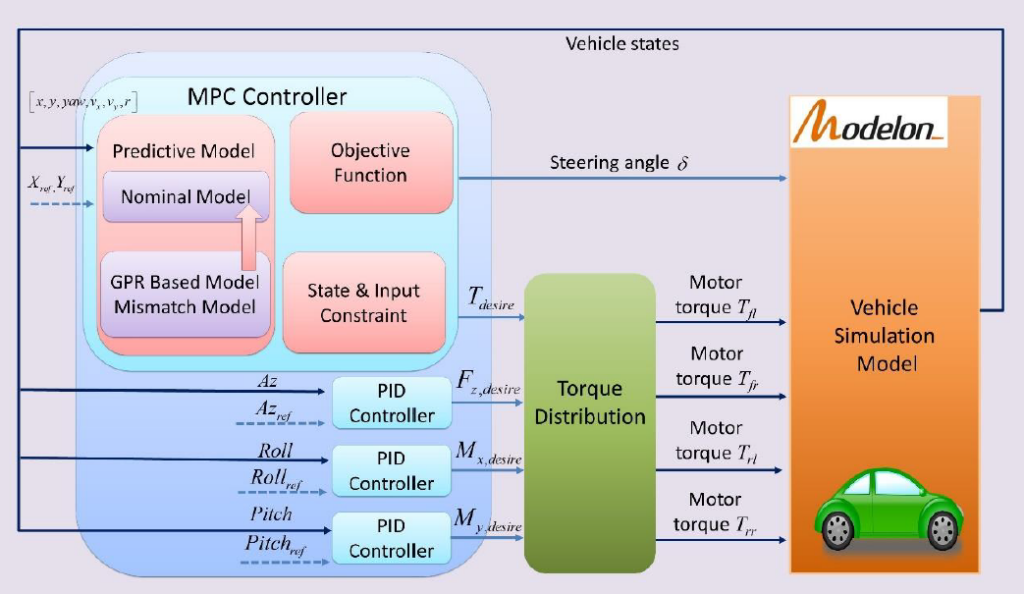
Fig. 2 Control scheme of our proposed controller
The control scheme we proposed for this benchmark competition can be summarized in Fig. 2. Firstly, we utilize the PID controller to calculate the expected additional vertical force, pitch, and roll moment resulting from random road disturbances. Next, employing the 3-DOF vehicle model and Gaussian Process Regress (GPR), a learning-based predictive model is employed to develop an MPC controller for tracking the desired speed and trajectory. Finally, the desired force and moment are converted into torque for each driving wheel through torque distribution.
MPC Controller Design
Model Predictive Control (MPC) is an optimal control technique in which the calculated control actions minimize a cost function for a constrained dynamical system over a finite receding horizon. As shown in Fig. 3, MPC anticipates the future behavior of the vehicle by utilizing a predictive model and computes optimal control actions accordingly. This is particularly useful when vehicle dynamics are complex, and the environment is uncertain.
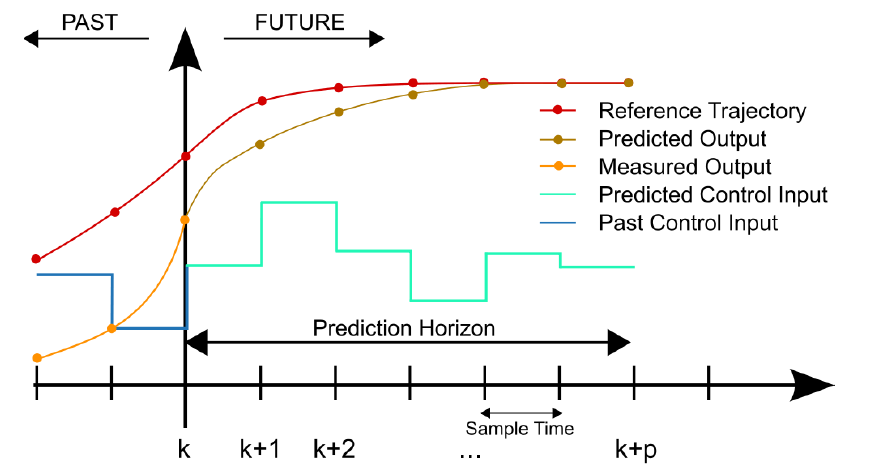
Fig. 3 The scheme of MPC
The optimization problem can be formulated as follows. The control objective is to minimize the tracking error of the desired speed and trajectory. The objective function consists of the 2-norm penalty of the tracking errors and the control inputs.
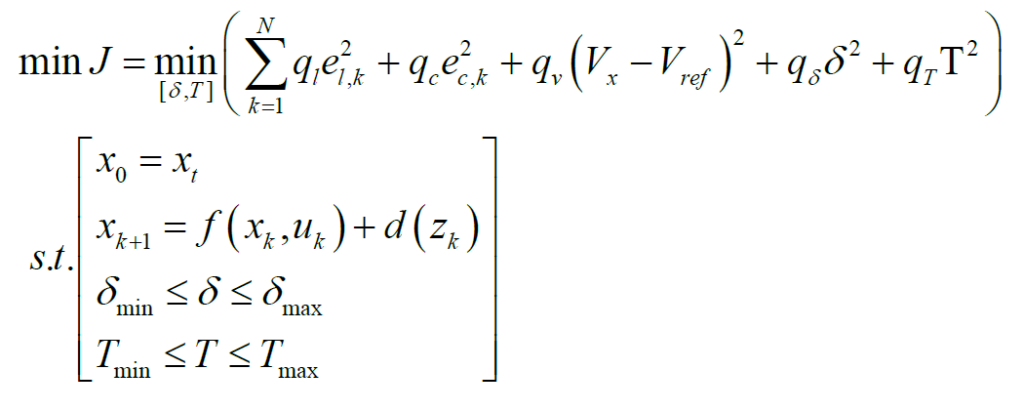
where
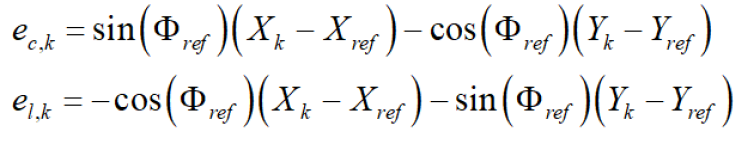
For the modeling of the 4-IWD vehicle, we use a 3-DOF nonlinear vehicle model. To ensure the performance of the MPC controller, a model-mismatch estimation model d( Zk ) based on GPR is developed and used to compensate the error of predicted vehicle state. Thus, the predictive model using model-mismatch learning can be expressed as:

The optimization problem is solved iteratively to get the desired steering angle and yaw moment. With the desired yaw moment, the desired driving/braking force of each in-wheel motor can be calculated by using the torque distribution matrix below:
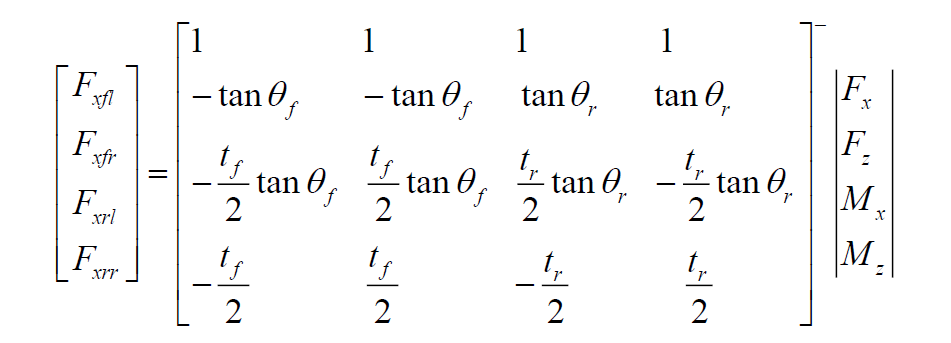
The torque distribution matrix is derived by the relationship between the longitudinal and vertical forces of the wheels, which is shown in Fig. 4.
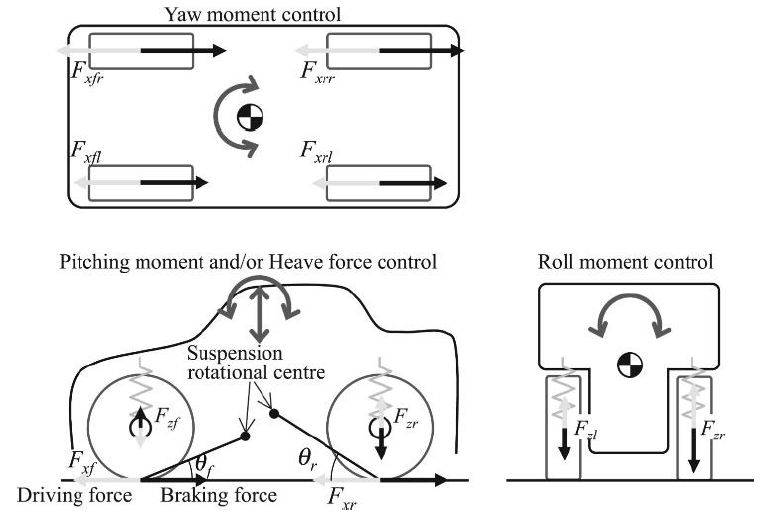
Fig. 4 The relationship between the longitudinal and vertical forces of the wheels
Simulation Results
In this case, the performance of the proposed learning MPC controller was shown by a thorough simulation carried out using Modelon Impact. The following figures provide controller performance and state constraint information with respect to each task. To validate the LMPC approach, traditional MPC and baseline controllers are selected as comparisons.
Task1
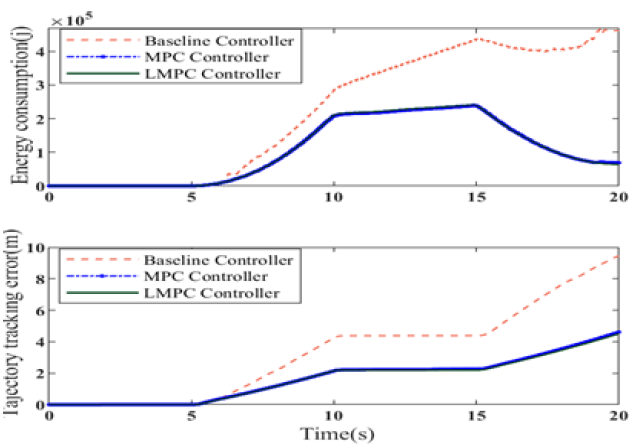
Fig. 5 Controller performance.
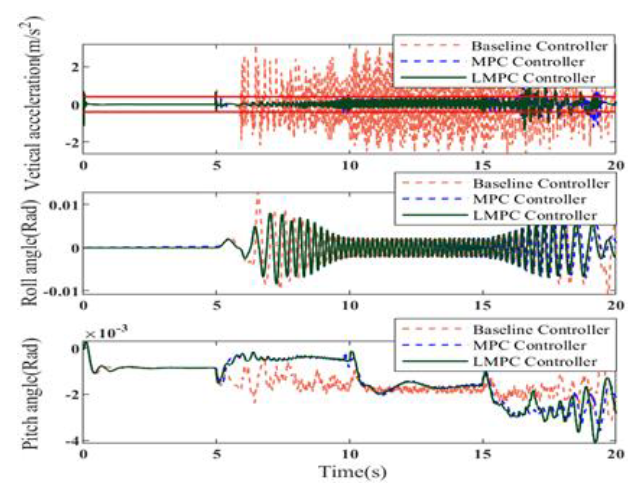
Fig. 6 State constraints.
Task2
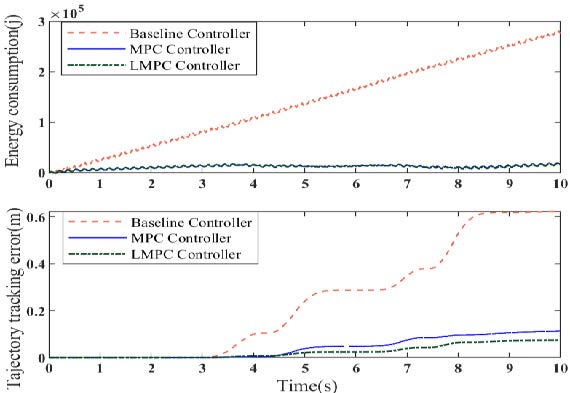
Fig. 7 Controller performance
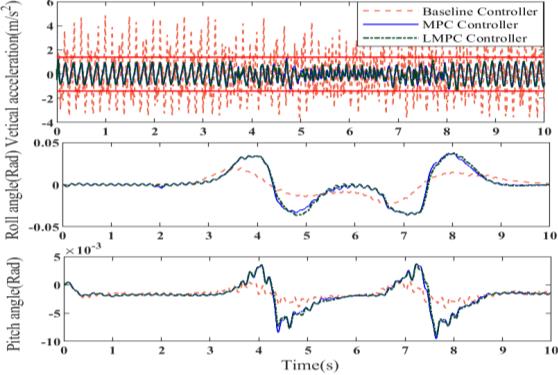
Fig. 8 State constraints
Fig. 5 and 6 show the controller performance and state constraints for task 1; the MPC controller and LMPC controller are both effective, but LMPC demonstrates superior performance, minimizing energy consumption and tracking error. The cumulative error of speed tracking is 4.5059, and the energy consumption is 6.4139x104J, about 7% less than that of a traditional MPC controller, with minimal violation of the state constraints. Fig. 7 and 8 show the controller performance and state constraints for task 2. For task 2, the outcome is similar: the cumulative error of trajectory tracking is 0.0743, significantly reduced compared to the MPC controller, and the energy consumption is 1.5482x104J, approximately 10% less than that of MPC. In task 2, the proposed scheme successfully maintains vertical acceleration, roll angle, and pitch angle within the specified limits, affirming its effectiveness.
Conclusion
This blog introduces an innovative control scheme employing a learning model predictive control (MPC) and body attitude control framework. A Simulink/Modelon Impact co-simulation test is conducted to validate the effectiveness of the proposed control scheme. Comparing the baseline’s results, it can be observed that the tracking errors of speed and trajectory are greatly reduced. The combination of Modelon Impact and Simulink not only delivers improved performance but also accelerates the speed of simulation. By employing learning MPC to develop controllers, it’s possible to rapidly explore a variety of innovative designs, enhancing the controller’s performance. Modelon is committed to continuously enhancing and expanding this technology for future projects, further advancing the field of system design and control.
About the Tongji University team:
Zongxuan Li received a B.S. degree from Jilin University, Changchun, China, in 2023. He is currently working toward the M.S. degree with the Shanghai Research Institute for Intelligent Autonomous Systems, Tongji University, Shanghai, China. His main research interests include learning model predictive control.
Qiao Kang received the B.S. degree from Jilin University, Changchun, China, in 2023. He is currently working toward the M.S. degree with the Shanghai Research Institute for Intelligent Autonomous Systems, Tongji University, Shanghai, China. His main research interests include motion planning and vehicle control.
Zhenghao Li received the B.S. degree in automotive engineering from Tongji University, Shanghai, China, in 2021, where he is currently working toward the M.S. degree. His main research interests include planning and control for autonomous vehicles.
Bingzhao Gao (Member, IEEE) received the B.S. and M.S. degrees in vehicle engineering from Jilin University, Changchun, China, in 1998 and 2002, respectively, and the Ph.D. degree in mechanical engineering from Yokohama National University, Yokohama, Japan, and in control engineering from Jilin University, in 2009. Since 2013, he has been a Professor with Jilin University. He is currently a Professor with Tongji University. His research interests include vehicle powertrain control and vehicle stability control.
Hong Chen (Fellow, IEEE) received the B.S. and M.S. degrees in process control from Zhejiang University, Hangzhou, China, in 1983 and 1986, respectively, and the Ph.D. degree in system dynamics and control engineering from the University of Stuttgart, Stuttgart, Germany, in 1997. In 1986, she joined the Jilin University of Technology, Changchun, China. From 1993 to 1997, she was a Wissenschaftlicher Mitarbeiter with the Institut fuer Systemdynamik und Regelungstechnik, University of Stuttgart. Since 1999, she has been a Professor with Jilin University, Changchun, and here after a Tang Aoqing Professor. From 2015 to 2019, she was the Director of the State Key Laboratory of Automotive Simulation and Control, Jilin University. She currently joins Tongji University, Shanghai, China, as a Distinguished Professor. Her research interests include model predictive control, nonlinear control, and applications in mechatronic systems focusing on automotive systems.