Driving Towards Carbon Neutrality With System Simulation
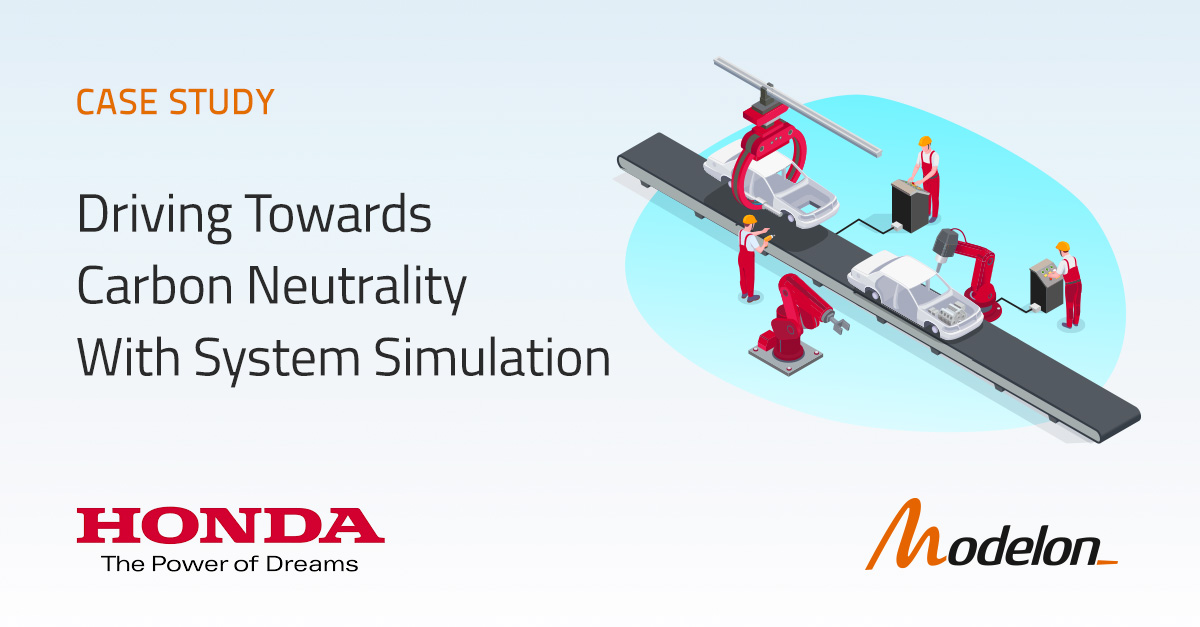
Honda uses Modelon Impact to design and evaluate a carbon neutral assembly plant with confidence.
Challenges
Honda Motor Company is a leading international manufacturer of automobiles, motorcycles, and power equipment. Headquartered in Tokyo, Japan, the world’s largest power unit manufacturer ships close to 30 million power units a year. With such a large influence in the mobility industry, Honda is taking a lead on decarbonization and pledging to be a carbon neutral organization by 2050.
Koji Moriyama, Principal Engineer at Honda, leads R&D projects targeting carbon neutrality, including energy solutions such as renewable energy fuels and hydrogen fuel cell battery systems. As an initial project, Dr. Moriyama was tasked with determining Honda’s approach toward transitioning production plants to be carbon neutral. However, with so many potential technology options, how would Honda decide on the right ones? What renewable energy sources, storage systems, and plant configurations provide the highest performance while also optimizing the total cost of operation?
To make these design decisions in an efficient time frame, Dr. Moriyama and his team turned to system simulation and optimization.
To consider their pilot project a success, Honda needed a system simulation solution that could:
- Accurately represent an existing assembly plant in the United States
- Consider a variety of carbon reduction options
- Select the option that results in the lowest total cost of ownership while being carbon neutral
The solution would also have to consider multiple constraints such as peak shaving, surface area for photovoltaics, and the minimum energy required in storage for backups.
Solutions
Dr. Moriyama and his team selected Modelon Impact for their pilot project. Modelon Impact contains native libraries and model packages that Honda needed to build an accurate virtual representation of their US plant. For scenarios in which Honda needed to tailor components, they could do so by accessing the model code layer as a result of Modelon Impact’s open standards-based architecture. Modelon Impact also has documented Python APIs that helped Dr. Moriyama and his team script advanced analyses and visualization tools to effectively communicate with their stakeholders.
The model of Honda’s assembly plant was built using Modelon Impact’s native microgrid package in the thermal power library. Varying loads such as electric, hydrogen, and thermal loads for buildings, transportation, and HVAC systems were considered within the model. This approach helped Honda assess different carbon neutral options to satisfy various loads and measure efficiency.
However, Honda’s requirements didn’t stop at just building the physical model. Multiple constraints needed to be accounted for within the model. This included the physical space that was required for photovoltaics, the amount of backup power the plant would need at all times, and seasonal energy demand paired with regulatory caps. Dr. Moriyama leveraged Modelon’s experts to ensure the necessary parameters were in place to create a more accurate model.
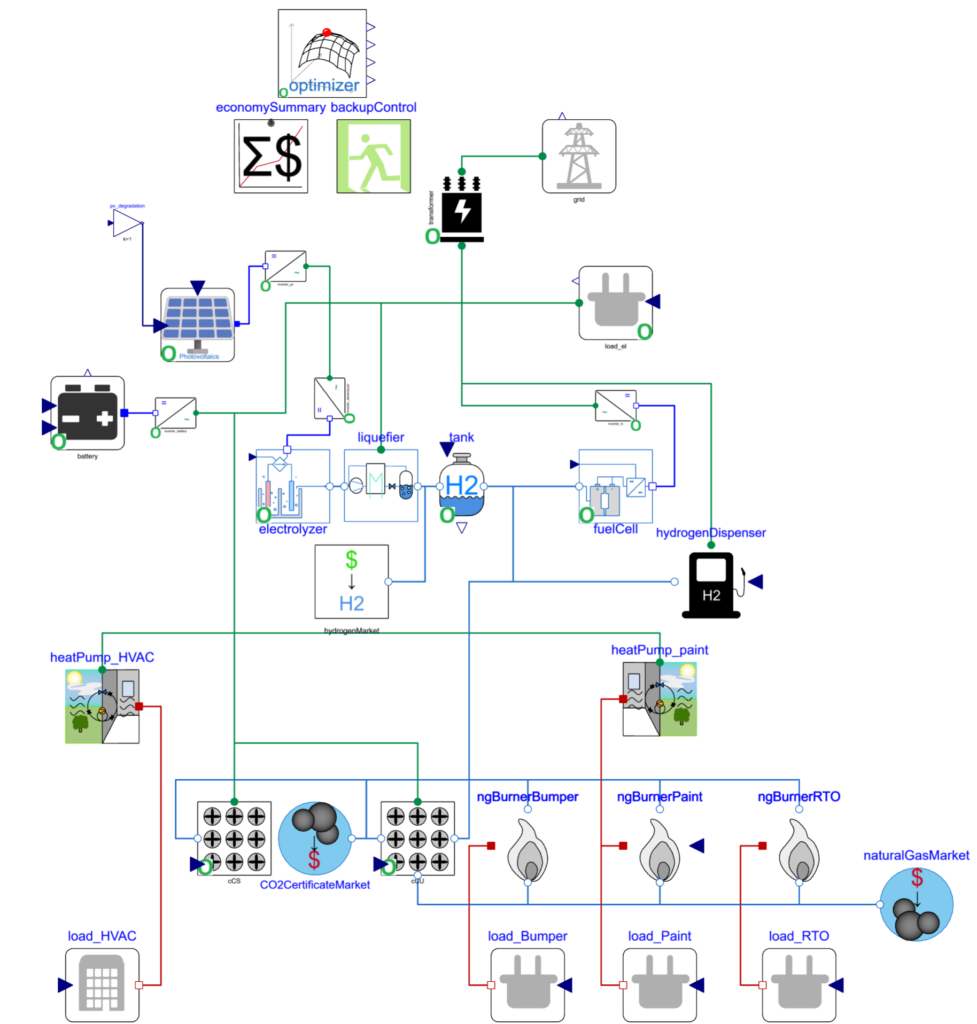
In order to make the correct decisions in a short time, it was determined that Honda would not need to design a control strategy for each considered plant configuration. It was more efficient for Honda to build their model and let Modelon Impact’s native solver optimize for both component sizing and control strategy at the same time. In this way, Honda was also able to get the best possible design for the considered plant.
To determine the total cost of operation, Honda reasonably estimated a fixed cost and an operational cost for each component. The grid model also accounted for peak shaving and the demand charge for high-demand seasons. Altogether, this approach proved to be accurate enough for Honda to continue their project while being computationally inexpensive.
“Modelon reviewed our requirement and developed a model with uninterrupted communications through bi-weekly online meetings with project updates. In addition, Modelon had been actively engaged with Honda for clarification and requested any essential information for a successful project. In the end, Modelon Impact was the right choice” says Dr. Moriyama.
Results
With a Modelon Impact model curated to Honda’s specifications, Dr. Moriyama and his team were able to simulate different scenarios and make conclusive decisions. For example, one of these decisions included choosing fuel cells over batteries for power backup. Not only were fuel cells the better option for providing power and lowering demand charges, they also were able to maintain a larger amount of power storage – making for a more financially viable option overall.
Honda was also able to see where to focus its time and effort on high-priority changes. When it came to importing versus generating hydrogen and electricity on-site, Modelon Impact’s optimization determined both options were necessary. While on-site electricity generation using photovoltaics was able to significantly reduce demand charges during peak months, they would not be less expensive than utility companies during off-peak seasons. On the other hand, running the electrolyzer to produce liquid hydrogen would be more expensive during peak season and hydrogen would therefore have to be imported. It was determined that running the electrolyzer on-site for the rest of the year would be the most cost-effective approach. The different technology options selected by the optimizer as well as the capacities in terms of energy per year are shown in the Sankey Diagram below as delivered by Modelon Impact’s simulation results.
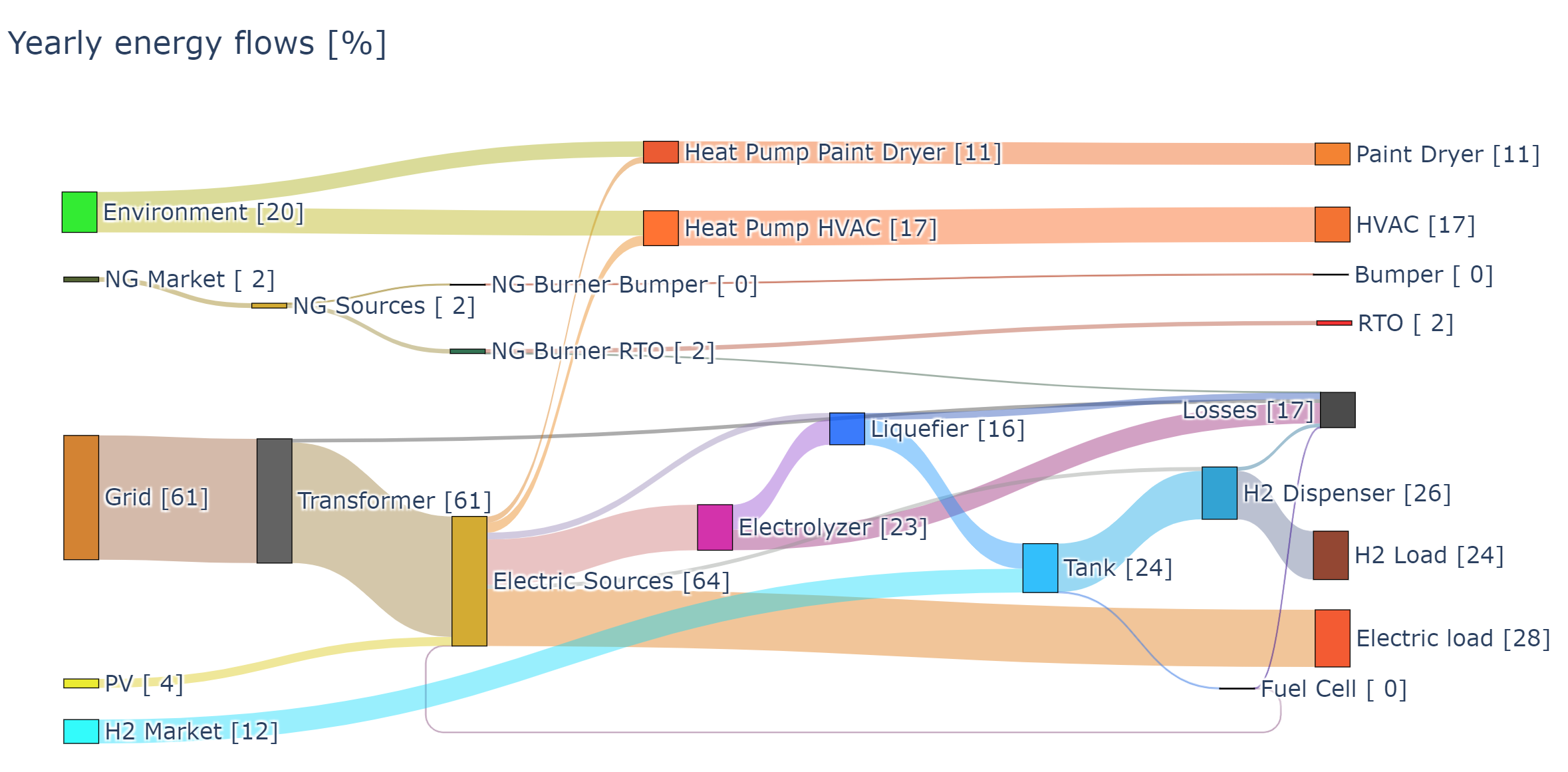
“Despite the short time frame, I conclude this project was a success. We were able to construct a framework that can be utilized to propose a future strategy and achieve a carbon reduction system with diverse options highlighting minimization of Total Cost of Ownership while optimizing system operation,” said Dr. Moriyama.
Modelon was able to satisfy all project requirements of Honda while also providing modeling and simulation expertise to help Honda make strategic decisions about their assembly plant. Honda continues to partner with Modelon to transition its facilities towards carbon neutral operation.