Modeling Solutions to Hydrogen Energy Storage Challenges
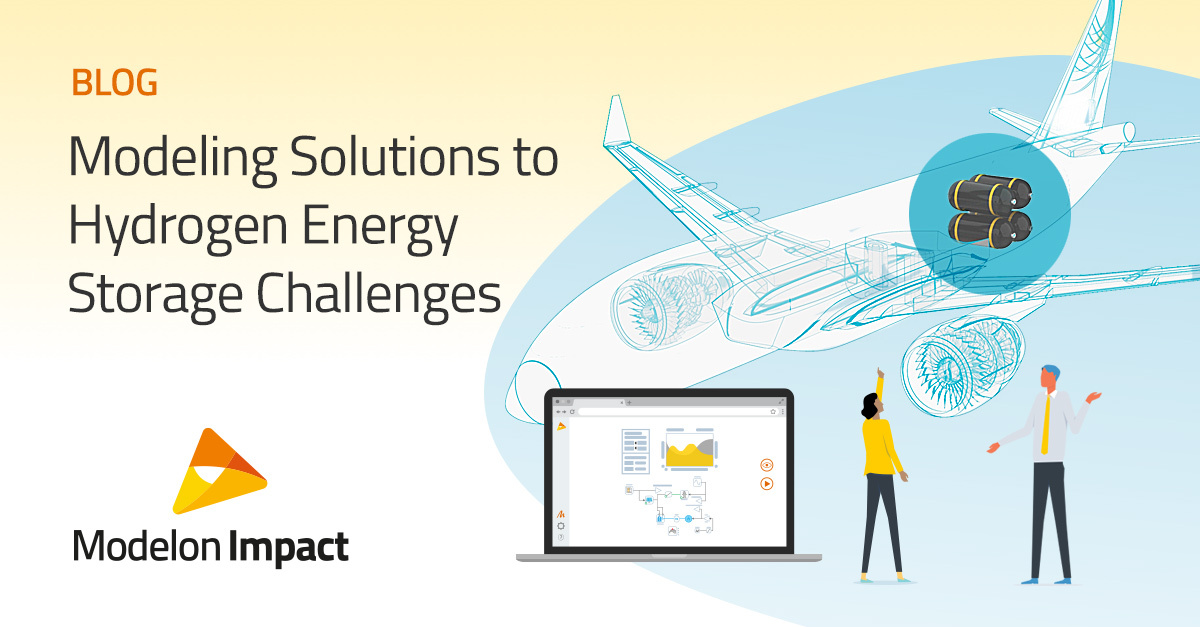
Hydrogen energy will play a significant role in our decarbonized future, replacing natural gas and fossil fuels in many contexts. As an energy source, hydrogen fuel is “clean”: its combustion yields only water vapor, a stray oxygen molecule, and some NOx (formed when oxygen binds with atmospheric nitrogen). Meanwhile, hydrogen fuel cells produce “clean energy,” emitting no greenhouse gasses. Shifting to hydrogen fuel combustion and fuel cells could substantially reduce emissions—especially those most environmentally damaging: methane and carbon dioxide.
The challenges with hydrogen production are widely discussed—especially issues around the challenge of shifting from fossil-fuel-powered electrolysis (i.e., “grey hydrogen”) to production powered by renewable energy (“green hydrogen”).
Safe storage may be an even more pressing concern. For fuel cells and hydrogen combustion engines to be viable, you need to be able to safely store and transport large volumes of cryogenic hydrogen in a variety of different vehicles working under often unpredictable conditions.
Thus far, despite decades of exploring the use of hydrogen fuel in aerospace, we’ve hardly scratched the surface.
Optimizing Hydrogen Storage for Widespread Application
Although technically challenging, hydrogen storage is well understood. Renato Bellarosa, Head of Propulsion Products and Tanks at Airbus Defense and Space, noted: “The space industry has been using pressure vessels for the storage of liquid propellent [hydrogen and oxygen] to fuel space exploration for decades. So we have a lot of expertise in damage tolerance, in advanced manufacturing technologies, and in vessel pressure testing.”
That said, it’s one thing to know we can safely store hydrogen on a handful of space shuttles that launch a few times each year; it’s quite another to ensure we can safely store hydrogen on 8,000 commercial jets flying the friendly skies daily.
Hydrogen storage optimization is an area where simulation-based modeling is essential, as it allows for fast, low-cost design exploration and prototyping that can quickly reveal novel problems hydrogen-powered airliners might face. The Modelon Impact platform and libraries are helping engineers do just that.
The Role of Simulation for Hydrogen Storage
Anh Nguyen, a Simulation Engineer at Modelon, offers a recent example he came across when running simulations of insulated hydrogen storage tanks for airliners. These tanks must be designed with far more constraints (regarding shape, weight, and insulation) than hydrogen fuel tanks used in other applications.
“We found that the rate of liquid hydrogen extraction has the potential to cause the pressure and temperature in the tank to decrease. As heat ingresses into the tank, the LH2 will evaporate, and the tank will vent off GH2 when the pressure limits are reached. When LH2 is extracted from the tank, the volume occupied by LH2 is reduced, giving space for LH2 to evaporate if there’s energy or GH2 to expand, reducing the rate at which pressure and temperature increase. When the rate of LH2 extraction is doubled in the experiment, it’s easier to see the pressure and liquid temperature are lower,” Anh explains.
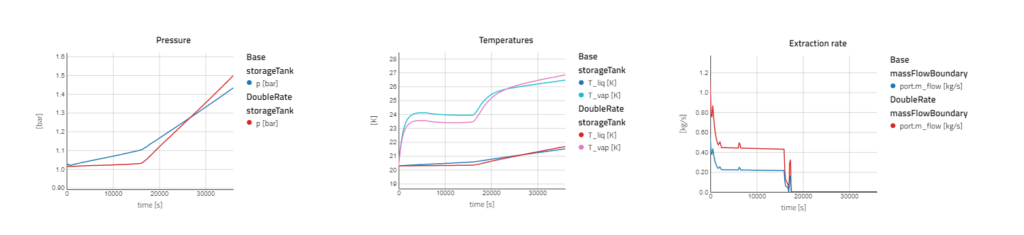
He continues, “If we consider an ideal case where the tank is well insulated with no heat ingress, the extraction of LH2 would decrease pressure and temperature as the expanding GH2 cools down by the Joule-Thomson effect. Keeping in mind that the ambient pressure in the cabin around the tanks could be near 0.8 bar, some heat ingress is desirable to avoid the tank pressure dropping below ambient pressure, which could then cause air leaking from the environment into the tank.”
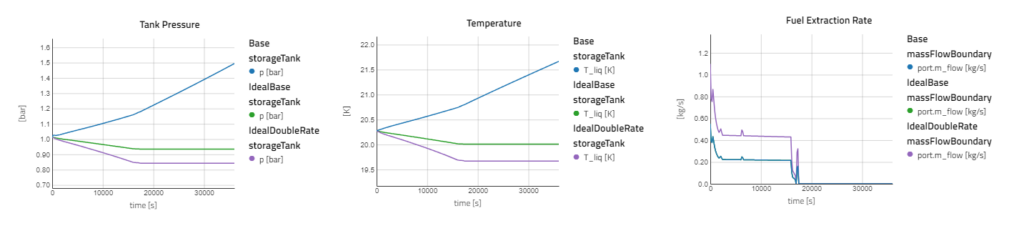
Hydrogen leaks from the tank can be dangerous on their own. But outside air seeping in is no better: air instantly freezes when it enters the tank, potentially blocking fuel lines.
Using Modelon’s Vapor Cycle Library in Modelon Impact, the model-based design and system simulation platform, engineers were able to iterate through several possible solutions quickly. Ultimately, they determined that the best approach to balancing system design and outcome might be adding a heater to better manage tank pressure throughout a flight. Dynamic model-based design makes it economical to collaborate and iterate, quickly eliminating unproductive approaches to new problems.
For engineers seeking to iterate quickly and meet project milestones, Modelon delivers system simulation technology and expertise. Modelon’s flagship product, Modelon Impact, is a cloud platform for virtually designing, simulating, and analyzing industrial systems. Combining decades of technical expertise with robust component libraries, we empower engineers to accelerate their work with hydrogen storage in the aerospace industry.