2023 Sustainable Aircraft Technology and Trends
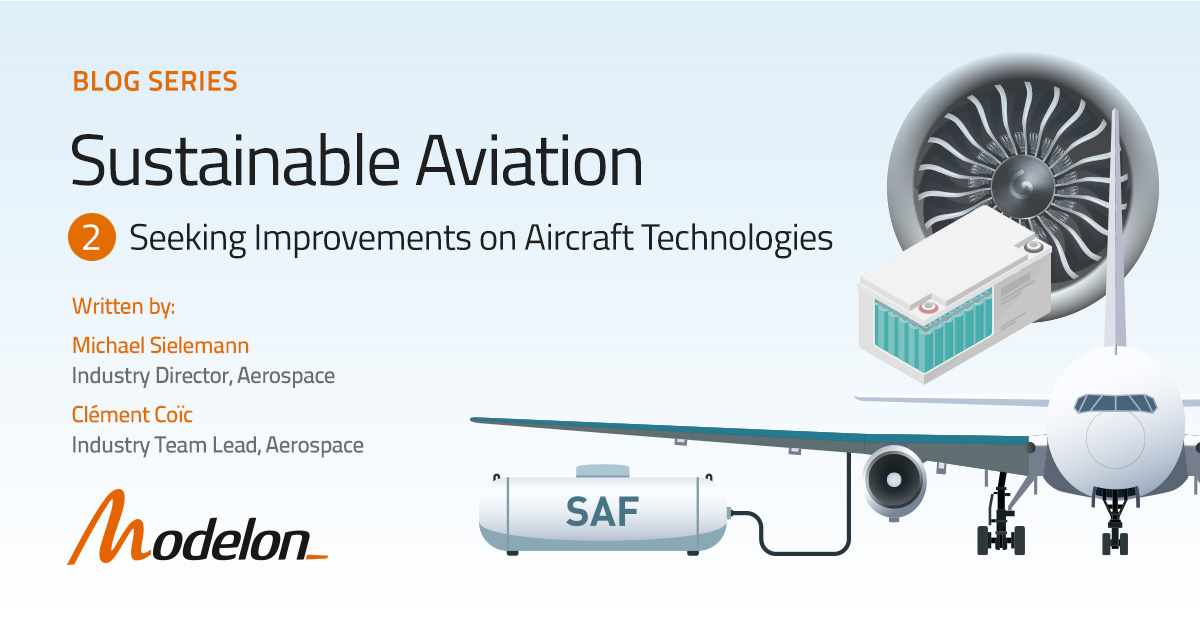
In the second blog of the Sustainable Aviation Series, our experts explain the current improvements and trends in aircraft technology that can be achieved reasonably soon in the aviation industry. In addition, we explain that other solutions, like hydrogen, require a complete redesign of the propulsion technologies and thus would happen most likely in a later future – but nonetheless, we think is required as a future aircraft sustainable solution.
- Read part 1 of this blog series which focuses on modeling and simulating fuel savings and increased flight range which is powered by hybrid electric propulsion systems.
Aircraft technologies and trends that are covered in this blog include:
- Ultra-High Bypass Ratio Geared Turbofan
- Alternative fuels: Sustainable Aviation Fuel (SAF)
- Partially Electric (“Hybrid”) Propulsion Concepts
Why Less Radical Aircraft Improvements are Insufficient
Engineers are trying to develop technologies that will enable more sustainable aviation in a timely manner. This is because the aviation industry has achieved remarkable fuel burn reductions over the last few decades, only to see them being outpaced by the demand for air travel. In the first blog of this series, we focused on increasing fuel savings and flight range with hybrid electric propulsion systems. Like this example, additional new aircraft solutions are required to help achieve the reductions. Let’s consider how aviation efficiency can be measured by looking at the mass of carbon dioxide generated per revenue passenger kilometer. This is shown below in Figure 1 over the last 60 years.
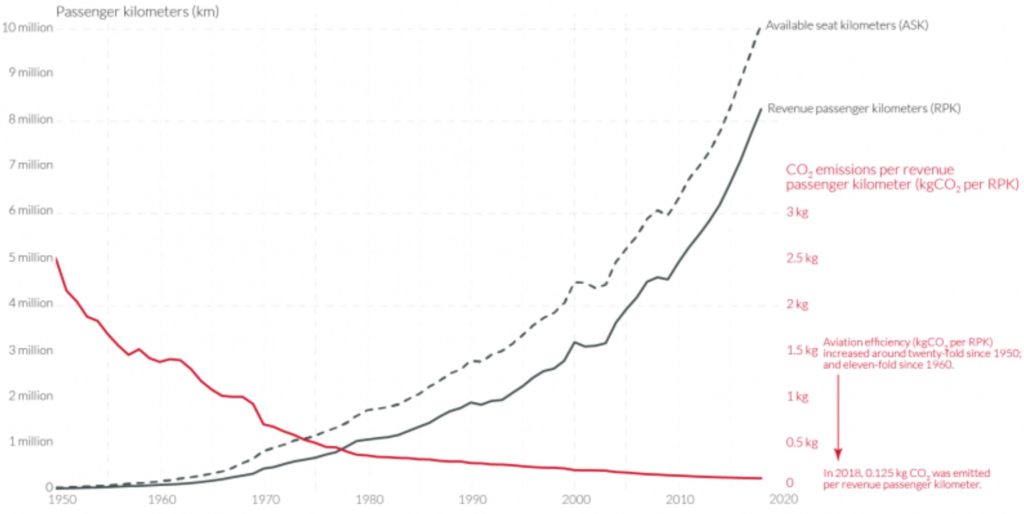
In the same time span, aviation use, measured in revenue passenger kilometers, increased by a factor of 76 (from 109,000 in 1960 to 8.257.000 million passenger kilometers in 2018). Data shows that even with the recent pandemic, aircraft emissions growth has not stopped. Because of this, it becomes critical for the aviation industry to reach neutral carbon emissions by the year 2050.
Short term, several promising technologies are infused into the so-called aero engine, the propulsion, and the power sub-system of the aircraft. They include ultra-high bypass ratio geared turbofan, Sustainable Aviation Fuel (SAF), and partially electric (“hybrid”) propulsion concepts.
Current Trends
Let’s dive into a deeper look at each of these current trends and improvements in existing aircraft technologies that are being improved upon as we speak.
Ultra-High Bypass Ratio Geared Turbofan
The first set of technologies in the aviation industry pipeline that offer mild improvements includes the current ultra-high bypass ratio geared turbofans. They increase the blade diameter and internal pressure of the turbofan. Here are two types of efficiency we can look at for the geared turbofan improvements:
- Thermal efficiency describes how efficiently input power provided to the engine (via a fuel flow or other heat source) is converted into intermediate mechanical power.
- Propulsive efficiency describes how efficiently intermediate mechanical power is converted into propulsive power moving the aircraft (e.g. the useful output power).
For thermal efficiency, improvements are limited by compressor materials. The key reason to improve thermal efficiency is to increase the overall pressure ratio, which also raises the compressor outlet temperature. Compressor rotor materials have to sustain massive mechanical loads due to the fast rotation, which can become impossible for ever higher outlet temperatures. The increase in overall pressure ratio also reduces the compressor cross-section area and leads to shorter last-stage compressor blades. Gaps in turn cannot be reduced arbitrarily, which means that, relatively, last-stage losses increase. Likewise, thermal efficiency improvements through a higher overall pressure ratio lead to higher turbine inlet temperatures, triggering turbine cooling challenges.
Finally, higher temperatures can also increase nitrogen oxide production in the combustor, which is a concerning pollutant. Overall efficiency can be taken as the product of thermal and propulsive efficiencies, the latter of which is limited by nacelle weight, drag, and possibly transmission efficiency. This might call for unducted fan concepts or distributed propulsion.
Sustainable Aviation Fuel (SAF)
Sustainable Aviation Fuel (SAF) is also proposed as an intermediate improvement of sustainability in the industry. Chemically, these fuels are very similar to conventional jet aviation fuel refined from oil. Sophisticated processes are used to source the atomic parts from more sustainable supplies for SAF. For instance in SAF production, one could use residuals produced by algae for such supplies, or even extract the unwanted carbon dioxide out of flue gas or the atmosphere.
While the use of SAF still results in essentially the same emissions, their supporters argue that the production requires extracting a similar amount from the atmosphere or similar sources (“offsetting”). However, the technical production at scale and feedstock sourcing remain largely unsolved. For ethical reasons, these should be produced from non-edible substances, which is not always the case. SAF has the potential to reduce CO2 emissions compared to traditional jet fuel, depending on the technological pathway and feedstocks used to produce the fuel. Other benefits of SAF include local air quality improvements due to lower sulfur content and reductions in soot pollution.
Partially Electric (“Hybrid”) Propulsion Concepts
Partially electric (“hybrid”) propulsion concepts, in combination with distributed propulsion, is the third set of aircraft technology in the aviation industry pipeline to increase sustainability. These mitigate typical contradicting design requirements with electrical machines. Some examples include:
- Turbofan designs suffer less from the typical compromise between take-off performance and noise vs. cruise efficiency. Hybridization allows for the operation of turbomachinery in more efficient operating conditions.
- Electric machines that modulate the gas turbine transients and allow operation with reduced surge margin, or route power to distributed propulsors, which can be more energy efficient as they ingest the aerodynamic boundary layer (and thus incur less ram drag).
Several hybrid electric propulsion concepts are deteriorated by the low specific energy of batteries and efficiency reductions of energy conversion. The specific energy of batteries can currently be projected to reach about 250 Wh/kg in the next couple of years. Jet fuel in turn has a specific energy of 12,000 Wh/kg.
For example, a generic regional jet has a Maximum Takeoff Weight of 49 tons (108,000 lbm) and a maximum fuel loading of 12 tons (26,500 lbm). Such aircraft’s wing sizing parameters are shown in the video below. This would mean that replacing the energy stored in fuel entirely with batteries would require 576 tons (1,270,000 lbm).
This results in a 13 times higher Maximum Takeoff Weight, before including any nonlinear (“snowball”) effects or any other sub-system changes. All extra mass on an aircraft causes extra lift and drag that’s required. This then becomes immediately clear how electrification must be injected carefully into propulsion concepts.
Converting gas turbine shaft power to electric power as well as converting electric power back into shaft power/thrust can be done very efficiently with today’s electric power systems. However, the current turbofan does not require any such conversion. It converts the shaft power directly to thrust and can therefore be more efficient. Any such propulsion system must first “payback” efficiency losses from extra mass and conversion inefficiencies due to its installation before it can deliver net benefits.
What’s in store for the future of aircraft engineering?
Our experts are currently seeing aircraft improvements and trends like the ultra-high bypass ratio geared turbofan, aviation fuel (Sustainable Aviation Fuel), and partially electric propulsion concepts. For these reasons, Modelon expects healthy single-digit to low double-digit fuel burn improvements for the current aircraft technology pipeline on propulsion and power sub-systems in the industry. Notably, they can be further increased with technical improvements to aerodynamics, structures, maintenance, and so on. Since technological improvements have too often been outpaced by the increase in aerospace travel, we therefore strongly believe that something more disruptive – like hydrogen propulsion – is required as a clean solution for the future.
Hydrogen propulsion reduces massively flight emissions because it’s a uniquely abundant renewable source of energy – down to zero when using a Fuel Cell. But at the same time, it brings its share of challenges, both on the aircraft propulsion, the storage itself, and the airport infrastructure for hydrogen generation and filling.
Keep a look out for our upcoming blog where our engineering experts explain hydrogen propulsion, the advantages, the challenges, and how a complete redesign of hydrogen propulsion technologies is required – which is why it will most likely be a longer-term effort. Because of this, Modelon’s simulation software, Modelon Impact, is enabling organizations to speed up the engineering design process.
References
Figure 1: Our World in Data https://ourworldindata.org/uploads/2020/10/Aviation-traffic-and-efficiency-Lee-et-al.-2020-800×505.png