Pioneering Hydrogen-Powered Aviation with System Modeling and Simulation
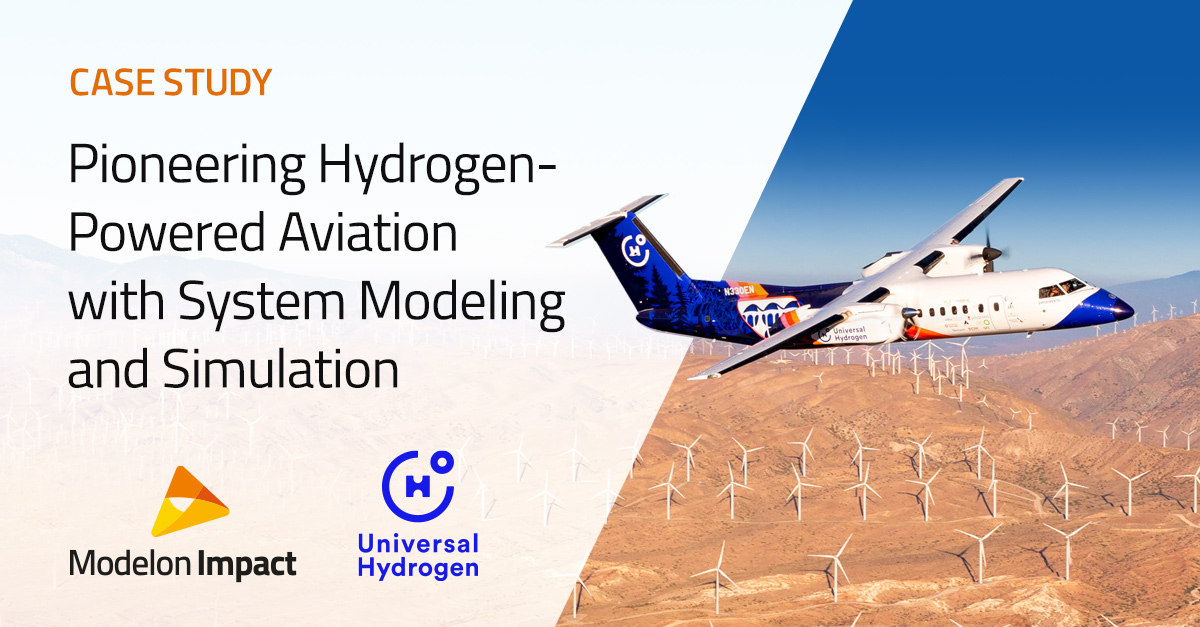
Universal Hydrogen designs, validates, and simulates their unique Liquid Hydrogen Distribution System with Modelon Impact.
From engineering centers in Los Angeles, California, and Toulouse, France, Universal Hydrogen is building the future of flight by commercializing true zero-carbon fuel. Universal Hydrogen has an ambitious mission to put aviation on a trajectory to meet Paris Agreement emissions targets by making hydrogen-powered commercial flight a near-term reality. As an international pioneer in hydrogen fuel services, Universal Hydrogen takes a novel approach to hydrogen-powered aviation.
They’re building modular liquid hydrogen conversion kits rather than hydrogen-powered aircraft from the ground up. The conversion kit integrates their new modular hydrogen capsules to store the hydrogen. The conversion kits are installed onboard regional turboprop aircraft like those used in the company’s test flights throughout 2023. Hydrogen modules connect to an electric powertrain using fuel cells to offer air travel that emits only water.
Challenges
As a Liquid Hydrogen Design Engineer, Théophile Coutant is a core contributor to the process of designing, validating, and testing Universal Hydrogen’s liquid hydrogen capsule for use onboard commercial aircraft. The module has a unique shape, mimicking the fuselage of a plane, and can be loaded into the aircraft using existing cargo handling equipment. Universal Hydrogen must maximize the liquid fuel in each capsule while controlling temperature and pressure during filling, storage, and operation to ensure safety.
“The modular approach makes us unique to our competitors. To decarbonize as fast as possible, our industry doesn’t have time to build out new, costly infrastructure. By transporting capsules already filled with liquid hydrogen from green production sites to airports around the world, we add value and have the potential to enable hydrogen-powered flight much sooner than our competitors,” said Theophile Coutant.
Efficiently filling, transporting, and vaporizing liquid hydrogen is critical to Universal Hydrogen’s business model. When held at extremely low temperatures (-250°C), liquid hydrogen has high energy density. If conditions inside the capsules are not maintained precisely, the liquid hydrogen will boil off from heat ingress. Significant safety concerns also exist if highly pressurized systems are not designed properly.
Given the varying operating conditions of commercial air travel, how can Universal Hydrogen ensure its system will function as intended? What system design will provide proper storage, heating, and flow of liquid hydrogen to the electric powertrain?
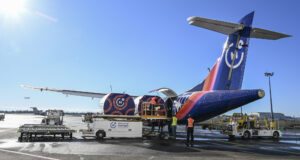
Universal Hydrogen turned to system simulation and modeling to ensure fast commercialization of their hydrogen conversion kits and successful tests of their system. Their teams needed a system simulation tool that could:
- Accurately represent the behavior of liquid hydrogen during filling, storage, extraction, and distribution
- Help make critical design decisions collaboratively using insights from simulation data
- Validate the model’s performance with physical prototype data
While simulation software tools for aviation have existed for decades, many legacy tools have limitations that do not meet the needs of modern teams. For example, legacy tools may only be available as local installations, making collaboration across teams difficult. Additionally, these tools often lack the export capabilities or functional mock units (FMUs) that ensure a variety of stakeholders can leverage a given model. Universal Hydrogen prioritized agile engineering and collaboration.
Solutions
Universal Hydrogen selected Modelon Impact as their system simulation solution. When building its model of the liquid hydrogen conversion kit and associated thermal management system, Universal Hydrogen used a hydrogen tank, pipes, valves, and heat exchangers. This pre-existing content from the Vapor Cycle Library, Liquid Cooling Library, and Heat Exchanger Library saved them critical time building their model. Using alternative system simulation solutions would have required weeks or months to build the necessary component models. Instead, many essential component models already existed in Modelon Impact and could be utilized on day one.
Universal Hydrogen asked Modelon’s aerospace experts to help them iterate on their model. The Modelon team’s advanced knowledge of model-based design and aerospace experience helped the Universal Hydrogen team architect their model.
Results
Due to liquid hydrogen’s cryogenic temperatures, Universal Hydrogen wanted to limit the number of moving parts in the liquid hydrogen capsule. During an in-person working session in Toulouse, France, Universal Hydrogen and Modelon experts worked together to build a first model of the Liquid Hydrogen Aircraft Distribution System. The model provided clear predictions of pressures and temperatures throughout the system, which allowed Universal Hydrogen to study the best location of components and the potential need for additional ones.
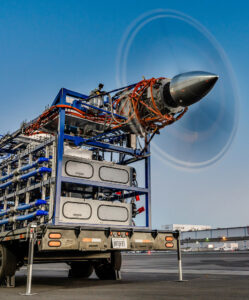
Universal Hydrogen’s final design was capable of controlling the changes in temperature and pressure inside the liquid hydrogen tank and the flow rate of liquid hydrogen to the electric powertrain. A control loop was created via a series of valves and pipes to manage the tank’s safe and continuous function.
After performing both transient and steady-state simulations, Universal Hydrogen compared their model’s results with physical prototype data. These comparisons validated the new model and gave Universal Hydrogen confidence in the liquid hydrogen capsule design.
“It was quite striking how easy it is to see and compare results with different models. It is much more intuitive with Modelon. The time to get an answer using simulation got reduced by a factor of 2 to 3, compared to custom code modeling or other simulation tools,” said Théophile Coutant.
Universal Hydrogen arrived at a complete model quickly, decreasing development costs and saving time on their journey to commercialize the liquid hydrogen conversion kits.
“Collaboration is important to us. We’re working on one model so everyone’s work is standardized and accessible. We can easily export our work with Modelon Impact and ensure that other teams can use it,” said Theophile Coutant, Liquid Hydrogen Design Engineer.
Modelon Impact and our aerospace experts met and exceeded Universal Hydrogen’s initial requirements for modeling and simulation with a fast turnaround for critical developments. The combined utility of a cloud-based platform like Modelon Impact and the knowledge of our team enables strategic decisions for Universal Hydrogen as they build a more sustainable aviation industry.
Universal Hydrogen continues to build and test its liquid hydrogen systems in Modelon Impact.