When to use Physical System Simulation?
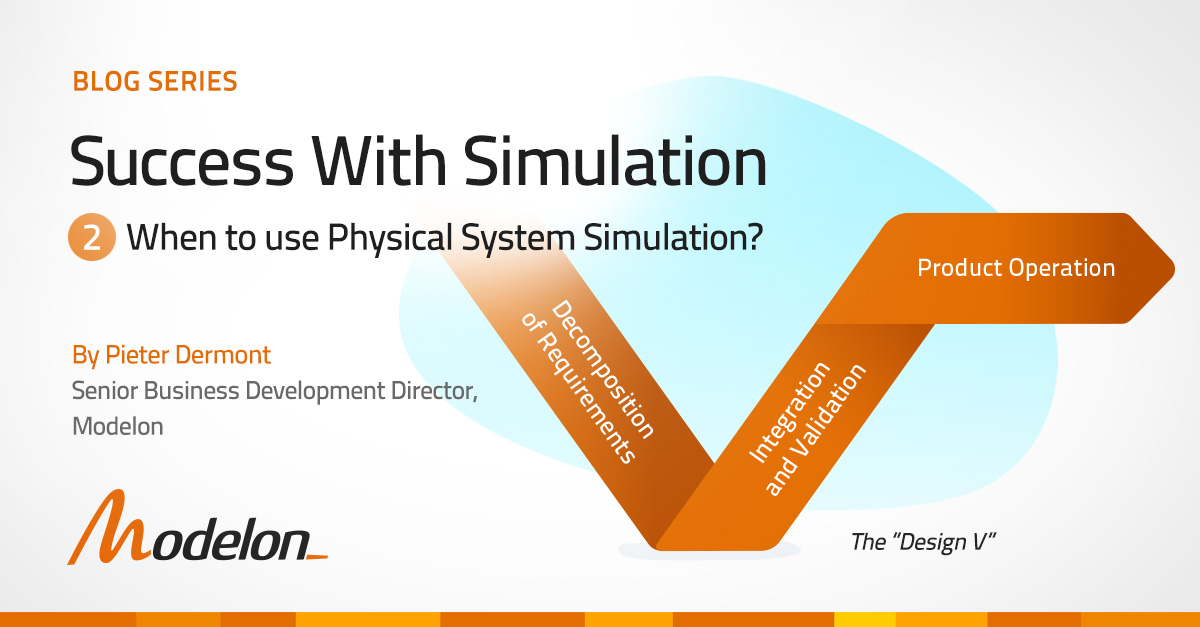
If you are engineering products or operating assets in the field, you may have wondered what system simulation can mean to you. Can it help you reduce development costs? What about reducing the duration of the product development cycle? Can it help you build better products? Alternatively, you may have heard of the ‘buzz word’ digital twins and wonder if it can help you operate your assets more effectively and enhance your products’ lifetime.
The opportunities to improve product design and operation with simulation are abundant. In this blog, we’ll aim to focus on the areas in which Modelon can positively add value to your organization while firmly staying with the physical system simulation paradigm.
Read Part 1 “What is Physical System Simulation”.
The “Design V’s” Extension
Often, engineers explain the model-based engineering design process with a graphical representation called the “Design V’. The “V” typically starts with defining the requirements of the product’s full system down to the connected sub-systems and subsequent components. Once requirements are identified, the product will then go through the development phase, where systems are connected, integrated with controls, and validated.
The “V” typically ends when the product is fully developed and ready for its go-to market. Recently, however, many engineering thought leaders have been proposing an extension to include the value of model-based approaches when the asset is in operation – making the “V” resemble more of a square root. Ultimately, physical system simulation isn’t just highly beneficial in the development of a product, but also for the entire product lifecycle.
Let’s further examine this newer representation, identifying and illustrating when and how physical system simulation can make a difference.
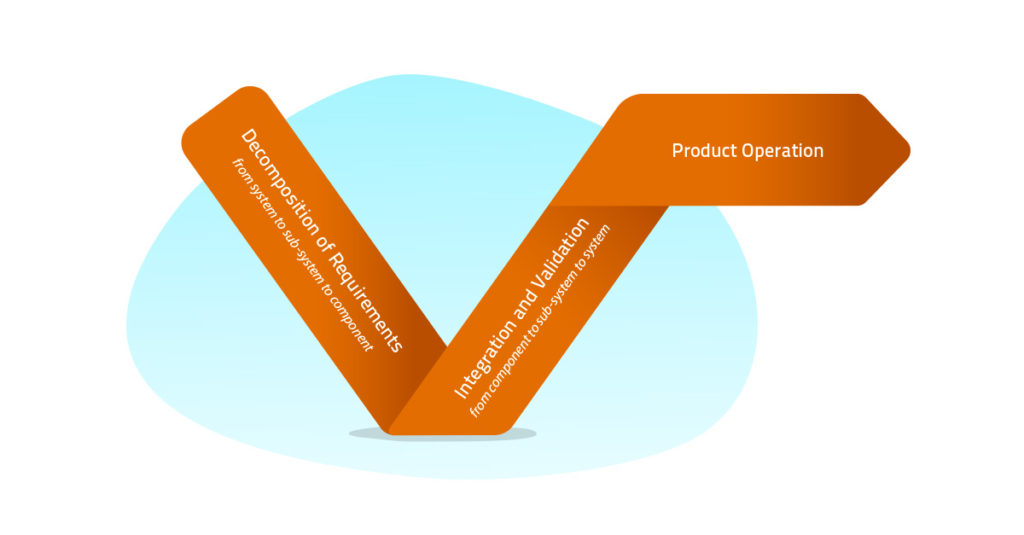
Decomposition of Requirements
During the early phases of product design, an engineer is tasked with the decomposition of requirements for each sub-system and ultimately the component. This starts with the topology decisions, where the ability to rapidly create and evaluate variants with physical system simulation helps. Steady-state physical system simulation is applied to help determine the performance requirements for each subsystem and component. To establish the appropriate component requirements for highly dynamic systems without including or designing control strategies, advanced and approachable optimization techniques can be utilized.
From this initial product design phase, one can determine the component requirements design. While physical system simulation is not often used in the design of components themselves (here, 3D simulation plays a bigger role), system simulation plays a critical supporting role. Many of Modelon’s customers are OEMs who integrate parts acquired from suppliers. Dynamic physical system simulation techniques are used to support the dialogue with their partners, determine requirements, and assess the performance of the purchased parts in a system.
Integration of Parts and Validation
At this point in the design cycle, we start walking gently upwards to the second leg of the “V”, the integration phase. In this phase, the components are integrated not only with each other but also with controls. Dynamic system models become a critical tool to validate and verify the system behavior as the dollar cost of simulation is comparatively low compared to physical prototyping and testing. Additionally, simulation permits rapid iterations through a variety of scenarios. In a simulation, failure of the system comes at no cost; in the physical world, failure may be catastrophic. As we reach the end of the second leg, you may also utilize the dynamic system models to design control strategies, tune controllers, and perform testing with hardware.
Product Operation
As the schematic levels out to a horizontal line, the product is now an asset in operation. At this stage, the value of physical system simulation stems from its ability to determine the performance of the asset that cannot directly be measured, as the number of sensors are limited, and certain parts of the asset cannot be measured or only measured with excessive uncertainty. A physics-based digital twin, as you can create with Modelon Impact, permits the extrapolation of sensor data to virtual sensors, leveraging the first-principle laws that link them. Virtual sensor data often pertains to asset health and lifetime, such as mechanical and thermal stresses.
Carry Your Model Assets Through the Design Cycle
While many use their physical system model for only one of the above-described phases, it will be cost and time effective to carry one and the same model through the entire product design cycle and into product operation. Minimizing digital discontinuities is a strategic objective for most model-based design practitioners. Modelon customers can minimize digital discontinuities as Modelon Impact enables handling model variants corresponding to the need of each design stage. In a larger tool ecosystem for product design, including component design tools, lifecycle management tools, and dedicated control design tools, Modelon customers can leverage open-standards technology that forms the backbone of Modelon Impact to successfully eliminate digital discontinuities.
Learn More From Modelon Customers
Let’s look at how Modelon customers are able to meet product deadlines and reduce costs through leveraging physical system simulation for requirement decomposition, integration & validation, or operation.
- For designing an entire and novel energy system with tens or hundreds of MW peak power, Malta Inc worked with Modelon solutions to navigate the first two steps of the design V as presented above. The team determined the system architecture to find the requirements for turbomachinery and heat exchangers and ultimately integrated and validated the system with variants of the same physical system model.
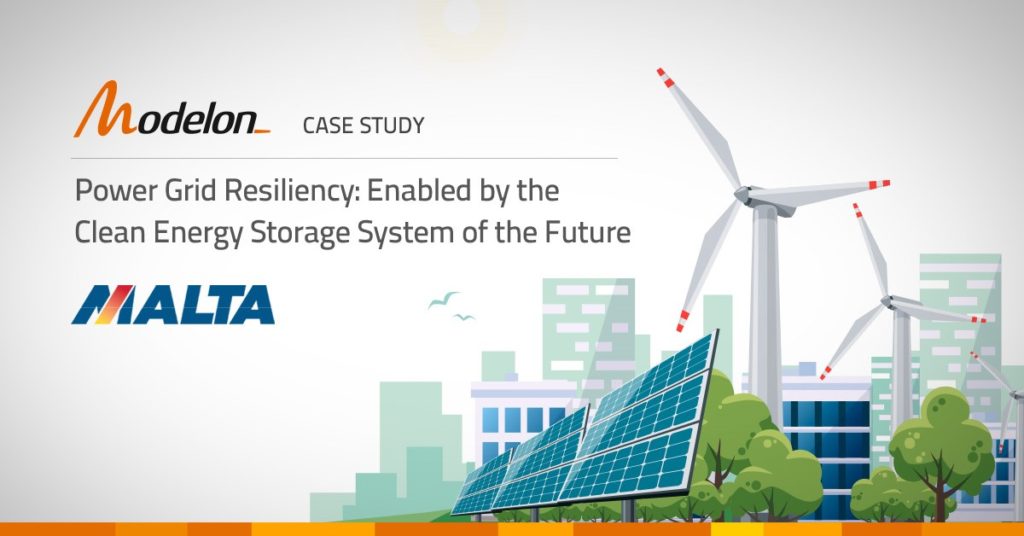
- Photovoltaics plants are often located in remote, desolate locations, and thus visual inspection and maintenance are costly. One of ENGIE’s photovoltaic plants is located in the Atacama Desert. A physical system model using Modelon Impact helps ENGIE with improving asset operation through extrapolating sensor data to pinpoint component failure.
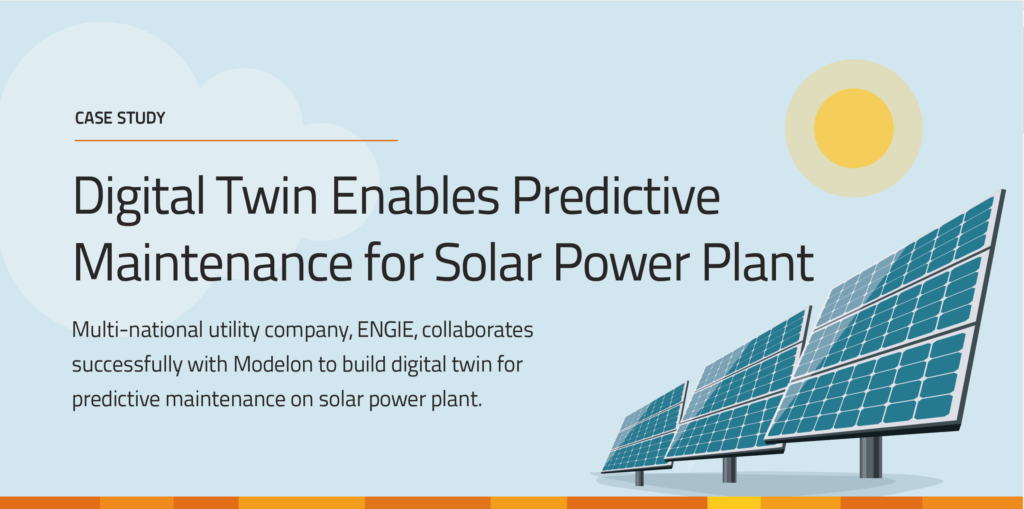
- The decomposition of the requirements phase is critical to achieve product specifications. The team from Lightyear develops solar-powered electric cars and is able to determine a better system architecture using Modelon Impact:
- “The architecture they had for the first prototype of Lightyear 0 had three pumps in the coolant system of their battery and drivetrain. When the components, such as the motors and inverters, started changing, Lightyear wondered if they could improve the controls by going from three pumps to two. They used Modelon Impact to optimize and simulate their two-pump design, proving that they could indeed simplify their system architecture – saving packaging and weight in the battery of their prototype vehicle.”
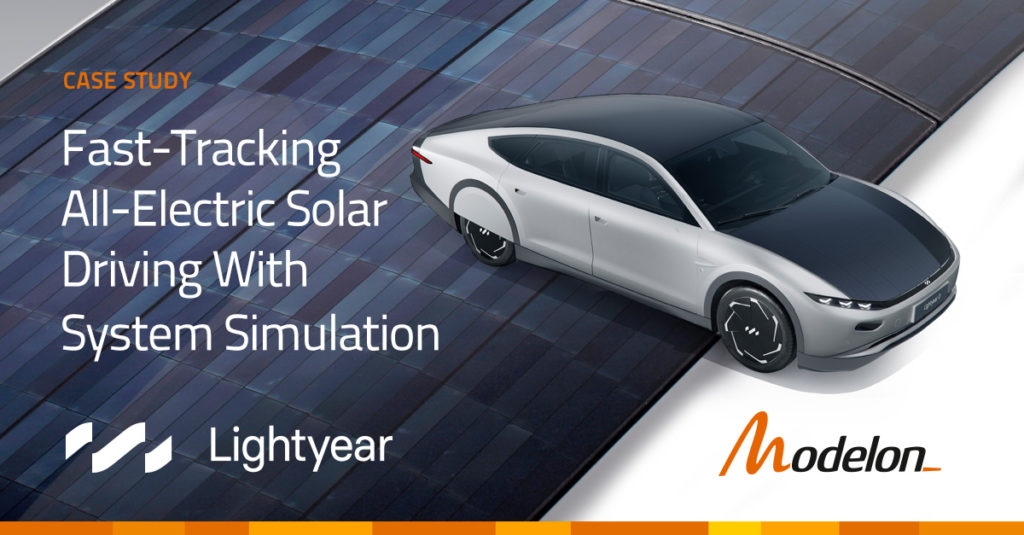
Conclusion for Physical System Simulation
We’ve hardly scratched the surface here and though the content may have helped you advance your thoughts – you might have even more questions now. We encourage you to reach out to us for a discussion on how physical system simulation can help you with your engineering problems, at any point of the design cycle.