物理システムシミュレーションを使うタイミングは?
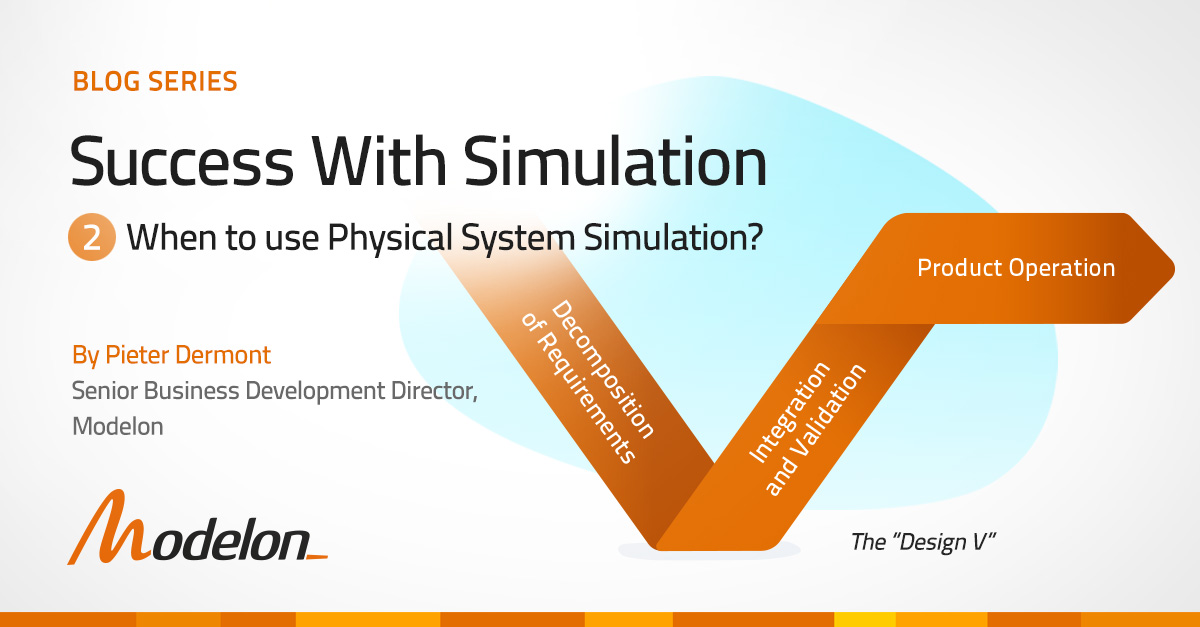
製品の設計や現場での製品運用をされている方は、システムシミュレーションがどのような意味を持つのか、疑問に思われたことがあるのではないでしょうか。開発コストの削減に役立つのだろうか?製品開発サイクルの期間を短縮することはできるのだろうか?より良い製品を作ることができるのだろうか?あるいは、デジタルツインというバズ・ワードを耳にし、それがより効果的にリソースを活用し、製品の寿命を延ばすことができるのか、と考えたことがあるかもしれません。
シミュレーションを活用することで、製品の設計や運用を改善するチャンスは豊富にあります。このブログでは、物理システムシミュレーションのパラダイムをしっかりと守りながら、モデロンが貴社に付加価値を与えることができる分野に注目していきます。
V字モデルの延長
エンジニアは、モデルベースエンジニアリングの設計プロセスを「V字モデル」と呼ばれる図式で説明することがよくあります。「V字」は通常、製品のフルシステムの要件を、接続されたサブシステムや後続のコンポーネントに至るまで定義することから始まります。要件が特定されると、製品は開発フェーズに入り、システムの接続、制御との統合、検証を行います。
「V字」は通常、製品が完全に開発され、市場に投入される準備が整った時点で終了します。しかし、最近では、多くのエンジニアリングのオピニオンリーダーが、資産が稼働しているときのモデルベースアプローチの価値を含めるように拡張することを提案しており、「V字」をより平方根の形に近いものにしています。物理システムシミュレーションは、製品の開発時だけでなく、製品のライフサイクル全体において非常に有益であることがわかります。
物理システムシミュレーションがどのような場面でどのように効果を発揮するのか、この新しい事象についてさらに検証してみましょう。
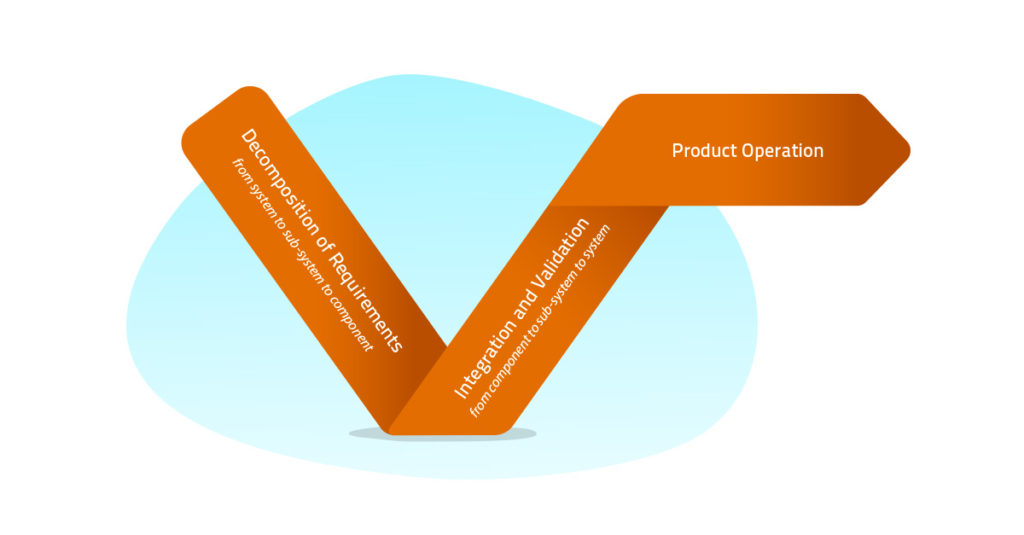
要求事項の分析
製品設計の初期段階において、エンジニアは、各サブシステム、そして最終的にはコンポーネントの要件の分析を行います。これは製品構成のトポロジーの決定から始まりますが、ここで物理システムシミュレーションでバリエーションを迅速に作成・評価できることが役立ちます。定常状態の物理システムシミュレーションは、各サブシステムとコンポーネントの性能要件を決定するために適用されます。制御戦略を含むことなく、また設計することなく、高度に動的なシステムの適切なコンポーネント要件を確立するために、先進的でアプローチしやすい最適化技術を利用することができます。
この製品設計の初期段階から、部品の設計要件を決定することができます。部品そのものの設計では物理的なシステムシミュレーションはあまり使われませんが(ここでは3Dシミュレーションが大きな役割を果たします)、システムシミュレーションは重要なサポート役となるのです。モデロンの顧客の多くは、サプライヤーから入手した部品を統合するOEMです。ダイナミックな物理システムシミュレーション技術は、パートナーとの対話をサポートし、要件を決定し、システム内の購入部品の性能を評価するために使用されています。
部品の統合と検証
この時点で、私たちはデザインサイクルの “V “の2番目の部分である統合フェーズに入り、ゆるやかに上へ歩き始めます。この段階では、コンポーネント同士だけでなく、制御系とも統合されます。シミュレーションのコストは、物理的なプロトタイピングやテストに比べて比較的低いため、動的なシステムモデルは、システムの挙動を検証し、確認するための重要なツールとなります。さらに、シミュレーションでは、さまざまなシナリオを迅速に反復することができます。シミュレーションでは、システムの不具合が発生してもコストがかかりませんが、物理的な世界では、不具合が発生すると致命的なダメージを受ける可能性があります。また、Vプロセスの2番目の段階として、ダイナミックシステムモデルを利用して、制御戦略の設計、コントローラーの調整、ハードウェアによるテストなどを行うこともできます。
製品オペレーション
平方根形のVプロセスの最後の水平線の部分では、製品は実際稼働している資産となります。この段階では、センサーの数が限られていたり、資産のある部分が測定できなかったり、過度の不確実性を伴ってしか測定できなかったりするため、物理システムシミュレーションの価値は、直接測定できない資産の性能を予測できるところに生まれます。Modelon Impactで作成できる物理ベースのデジタルツインは第一原理の物理法則から、センサーデータを仮想センサーに拡張し、活用することを可能とします。仮想センサーのデータは、機械的ストレスや熱ストレスなど、資産の健全性や寿命に関係するものが多いのです。
モデル資産をデザインサイクルに活かす
多くの場合、物理的なシステムモデルは上記のフェーズのうちの1つだけに使用されますが、1つの同じモデルを製品設計サイクル全体から製品運用まで活用することは、コストと時間の面で効果的です。デジタル開発の非連続性を最小化することは、ほとんどのモデルベース設計の実務家にとって戦略的な目標となっています。モデロンのユーザーは、Modelon Impactが各設計段階のニーズに対応したモデルバリエーションに対応することができるので、デジタル開発の非連続性を最小化することができます。コンポーネント設計ツール、ライフサイクル管理ツール、および専用制御設計ツールを含む製品設計のためのより大きなツールエコシステムにおいて、モデロンのお客様は、Modelon Impactのバックボーンを形成するオープンスタンダード技術を活用して、デジタル開発の非連続性をうまく消し去ることができます。
お客様の声
物理システムシミュレーションを要件分解、統合と検証、または運用に活用することで、モデロンのお客様がどのように製品の納期に間に合わせ、コストを削減しているのかを見てみましょう。
- 数十~数百MWのピークパワーを持つエネルギーシステム全体を新規に設計するために、Malta社はモデロンのソリューションを活用して、上記V字プロセスの最初の2ステップを実践しました。チームは、ターボ機械と熱交換器の要件を見つけるために、システムアーキテクチャを決定し、最終的に同じ物理システムモデルのバリエーションとシステムを統合して検証しました。
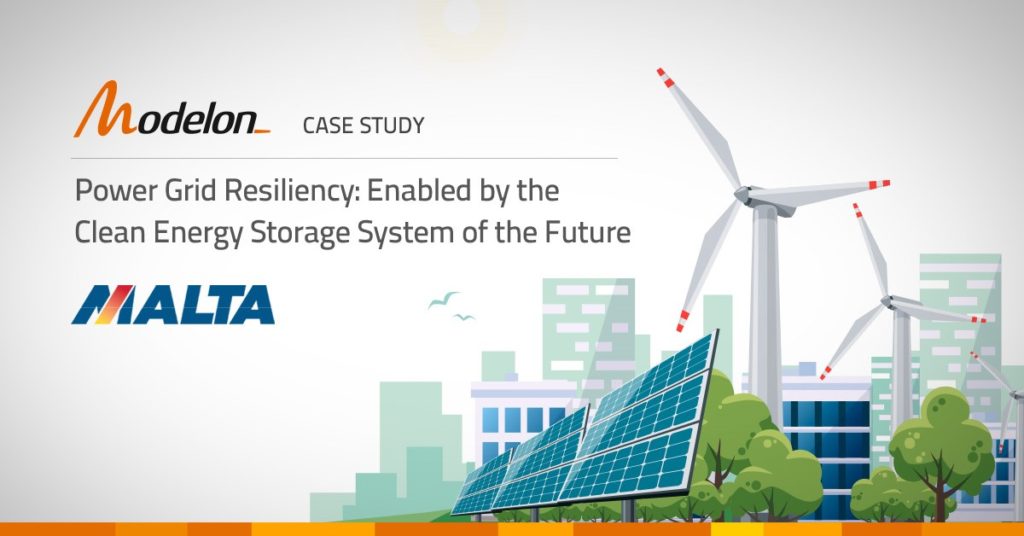
- 太陽光発電所は人里離れた荒涼とした場所にあることが多いため、目視による点検やメンテナンスにはコストがかかります。ENGIE社の太陽光発電所の1つは、アタカマ砂漠に位置しています。Modelon Impactを使用した物理システムモデルは、センサーのデータを外挿することで部品の故障を予測し、ENGIE社が資産の運用を改善するのに役立っています。
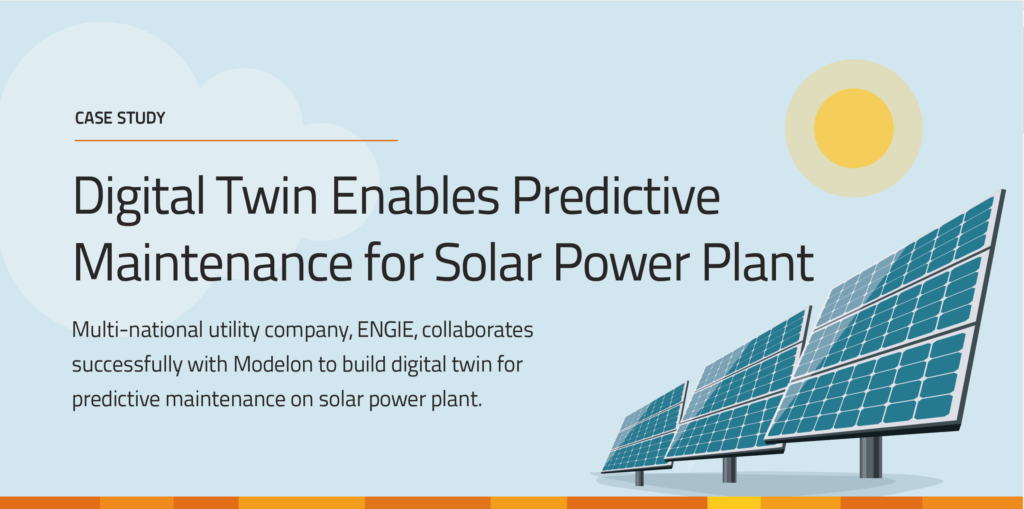
- 製品仕様を実現するためには、要求フェーズの分解が重要です。Lightyear社のチームは、太陽光発電の電気自動車を開発していますが、Modelon Impactを使って、より良いシステムアーキテクチャを決定することができました:
- 「Lightyear0の最初のプロトタイプのアーキテクチャでは、バッテリーとドライブトレインのクーラントシステムに3つのポンプを搭載していました。モーターやインバーターなどのコンポーネントが変化し始めたとき、Lightyear社は3つのポンプを2つにすることで制御を改善できないかと考えました。彼らはModelon Impactを使用して、2ポンプ設計の最適化とシミュレーションを行い、システムアーキテクチャを実際に簡素化できることを証明し、そして試作車両のバッテリーのパッケージと重量を削減することができました。」
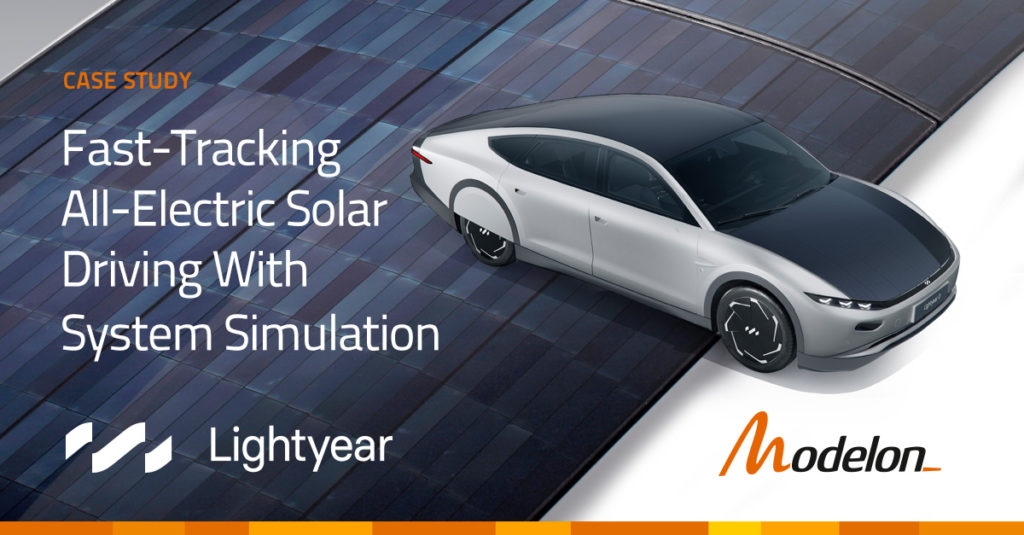
物理システムシミュレーションにおける結論
ここで紹介した内容は、あなたの考えを深めるのに役立ったかもしれませんが、さらに多くの疑問が湧いてきたかもしれません。物理システムシミュレーションが、設計サイクルのどの時点でも、お客様のエンジニアリングの問題にどのように役立つのか、ぜひ一度私たちにご相談ください。