Steady State and Dynamic Simulation: What is the difference?
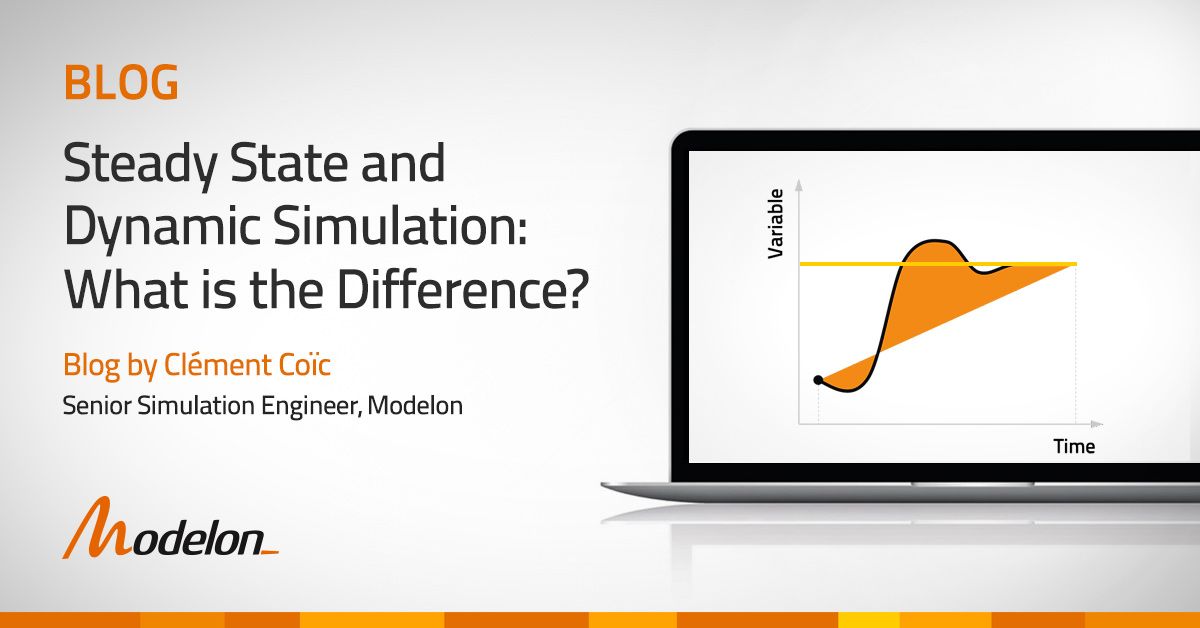
In this blog post, Modelon’s senior simulation engineer, Clément Coïc, breaks down the difference between steady-state and dynamic simulation. When would you use steady-state simulation? When would it be beneficial to use dynamic simulation?
A Convertible Car Driving on the Coast
Imagine yourself in a convertible, driving along the coast – the wind blowing through your hair (if you have any), controlling the wheel as the road ascends, descends, and winds near the coast. You stop halfway through your trip to fill the gas tank and your (engineering) mind begins to wonder:
- What would be the optimal size of my gas tank, so I do not need to refuel?
- What would have been the best acceleration profile to reduce my fuel consumption in this journey?
- How much time does it take to go from zero to the speed limit?
- How much have environmental elements, like wind drag, affected my burn rate?
These are questions that can be solved in Modelon Impact, using steady-state or dynamic simulation. Designing a system, whether it be an electric car or airplane, or an advanced energy storage system, to achieve specific targets and optimal operation in varying conditions is a challenge all engineers face.
To overcome that challenge, engineers must decide and implement varying modeling techniques, two of which include: Steady-State Simulation and/or Dynamic Simulation. What is the difference between steady-state and dynamic simulation? Simply, steady-state refers to a single point when the system is at equilibrium while dynamic refers to a trajectory where history matters. Let us discuss the specifics of each type
of simulation.
What is Steady-State Simulation?
Requirement specifications often include a high quantity of steady-state requirements where the path to this point is not relevant. When we want to know the fuel consumption at the speed limit on an uphill climb, we are not interested in whether the driver accelerated smoothly or aggressively to this functioning point.
It is relevant to highlight that steady-state does not mean fixed position. It means fixed behavior. Here, the car speed is in the fixed state. In hydraulics, it could be steady-flow. For a pendulum, it could be the fixed oscillation.
A product or system is designed to meet its requirements. Acknowledging that a high fraction of a system specification contains steady-state requirements, I am often surprised to see people use dynamic simulation in this context. Obviously, the steady-state results can be achieved at the end of a dynamic simulation as it reaches equilibrium. But this should be done with care – making sure that all states that are supposed to be steady are steady, not just looking at one curve.
The Value of Steady-State Simulation
Steady-state simulation maximizes productivity; you obtain the result directly and faster, by several orders of magnitude, and it simplifies post-processing of the results. It is beneficial for defining the problem directly as steady and solving the system for it. Like the Pareto principle: you reach 80% of the objectives with 20% of effort. You can extrapolate the gain on a design exploration, where you run hundreds or thousands of points.
Modelon Impact includes steady-state solvers, as well as our Physics-Based Solving technology, that enables adding engineering insights in models so that the steady-state simulation solves even faster and in an extremely robust way. This also allows answering several questions with a single model.
What is Dynamic Simulation?
Now we will uncover the benefits and value of dynamic simulation! Not all requirements are steady-state. Dynamic simulation allows engineers to study how a system behaves in reaction to a change. When pressing the gas pedal there is often a short delay before the car accelerates. This delayed behavior can be captured with dynamic simulation.
Acknowledging that the fuel in the tank is energy stored, accelerating induces burning fuel which reduces the available fuel quantity in the tank. Studying the optimum acceleration profile to maximize the distance along the coast is a dynamic optimization problem.
Engineers needing to simulate entire driving cycles to assess vehicle fuel consumption, and resulting CO2 emissions is a relevant case for dynamic simulation. System response to failure is another example in which the focus is on the transient response of the system and not the steady behavior. Dynamic simulations look at the evolution of variables along a mission profile. You are no more looking at a single functioning point but at the continuous trajectory in time.
The Value of Dynamic Simulation
Dynamic simulation is essential for achieving many goals such as reducing energy consumption along a drive cycle; extracting the maximum force to steer the wheel during a parking maneuver; assessing the behavior of automatically controlled systems such as evaluating the time for the convertible rooftop to open and close. Imagine the rooftop remaining half-open because the controller is not well designed and stopped half-way through its mission. System response to failure is another example in which the focus is on the transient response of the system and not its steady behavior.
Modelon Impact – Offering Steady-State and Dynamic Simulation Capabilities
Engineers understand the benefits and value of both steady-state and dynamic simulation, and as a result software providers responded by developing tools specific for each. This, unfortunately, has built a barrier between both worlds – which should be complementary. Modelon Impact removes this barrier, offering both simulation capabilities so that the users can leverage the correct solution in a single tool, based on the problem to solve. The relevant questions an engineer wonders about can be answered in Modelon Impact!
If you have additional questions regarding steady-state simulation or dynamic simulation capabilities in Modelon Impact, contact us.