Hydrogen Propulsion: The Advantages and Challenges
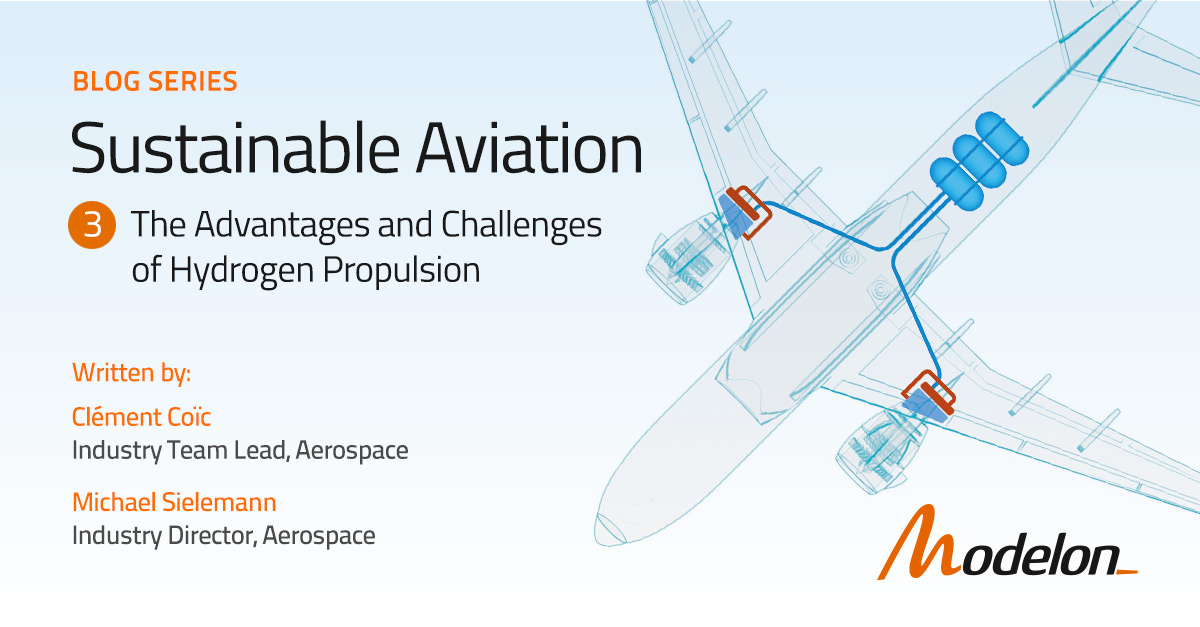
To act against a continuing global warming crisis, the aerospace industry is searching for alternative propulsion systems. The main content in the third blog of the Sustainable Aviation Series includes information about what hydrogen propulsion is, and the advantages and challenges surrounding this emerging technology.
- Part 1 of this blog series focuses on modeling and simulating fuel savings and increased flight range for aircrafts powered by hybrid electric propulsion systems.
- Part 2 of this blog series explains the improvements and trends that our experts are seeing in aircraft technologies and why other solutions will most likely happen in later future.
What is Hydrogen Propulsion?
Conventional fuels used nowadays for aircraft propulsion release carbon emissions into the atmosphere during combustion – as they are partly composed of carbon molecules – which is a contributor to global warming.
Introducing hydrogen propulsion, a technology that emits zero carbon dioxide (CO2) while flying and could be used to power a fuel cell to generate electricity to power a propeller. There are several types of fuel cells – the most common are:
- Proton-exchange membrane (PEMFC)
- Solid oxide (SOFC)
In both technologies, the fuel is typically hydrogen and a chemical reaction with an oxidizing agent (often oxygen) generates electricity and converts the hydrogen into mostly water. For PEMFC, the membrane lets the hydrogen protons cross toward the oxygen while the electrons – blocked by the membrane – are redirected through an electrical circuit. Thus, inducing a direct current through the circuit. When the hydrogen protons reach the oxygen, they react to form mostly water. In a hydrogen propulsion system, the electrical power generated is typically used either directly to power an electric motor that rotates a propeller or stored in batteries for later usage.
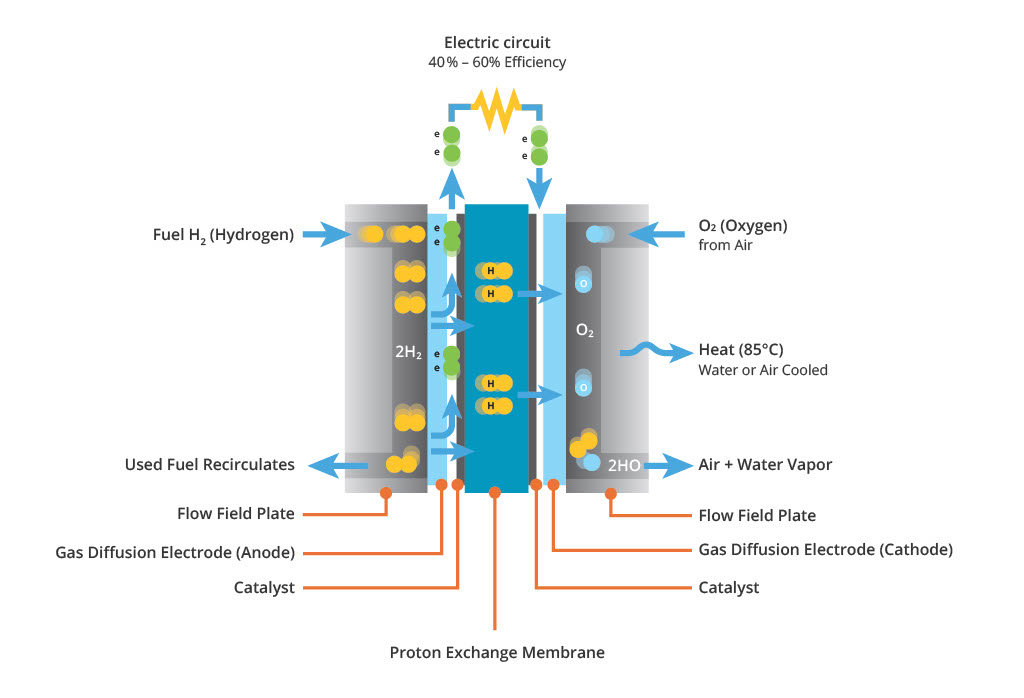
In this blog, you’ll learn compelling reasons why you should think about integrating hydrogen propulsion into your aircraft design, as well as the challenges you may encounter along the way.
The Advantages of Hydrogen Propulsion
The advantages of hydrogen as a fuel for aircraft are astonishing:
- It is lightweight
- It does not generate CO2
- It can be generated anywhere it is needed
- Refueling times are short
Lightweight
Hydrogen’s energy density is about three times higher than jet fuel. This means that, for the same amount of energy, hydrogen would be three times lighter to transport in an aircraft than jet fuel. This is a remarkable difference from some concepts in the current technology pipeline, namely the full and hybrid electric ones. Instead of looking for designs and concepts of operation where limited use of the alternative energy source brings benefits, it inherently allows us to “think big” (thanks to the theoretical 3x improvement of the fuel mass for the same amount of energy in comparison to jet fuel).
Lack of Co2 generation
When talking about the context in which hydrogen propulsion is used, there are two main use cases:
- Hydrogen aero engine: Substituting the aviation fuel with hydrogen, hence burning it. The combustion of hydrogen does not generate carbon dioxide.
- Hydrogen fuel cell: Using hydrogen to feed a fuel cell would generate electricity used by electric motors to power the aircraft propellers or fans. In such a system, the fuel cell would generate electricity and water.
In neither case is carbon dioxide generated. Both would lead to substantial improvements in greenhouse emissions.
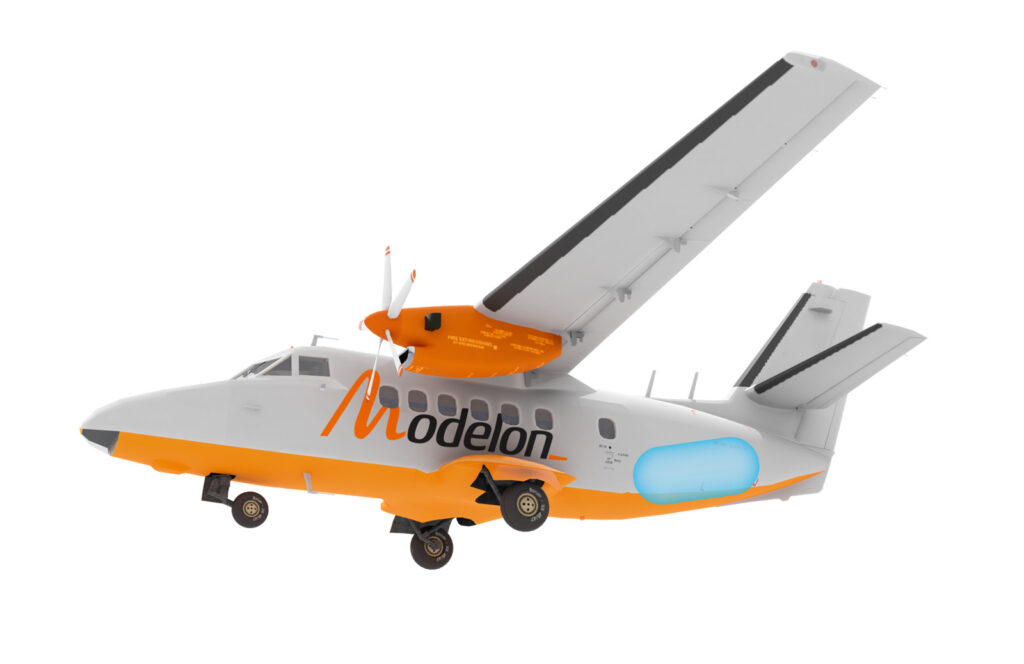
Generation wherever needed
Contrary to jet fuel which requires oil extraction in fewer places, is harder to access, and has complex refinement, hydrogen can be generated anywhere there is water, electricity, and an electrolyzer. Hydrogen can be generated near its consumption point – removing the need for long-distance transport.
Refueling time
As discussed in our previous blog post, alternatives for improving sustainability in aviation could involve batteries. Charging time for large battery packs is typically longer than refueling hydrogen tanks. Furthermore, it has already been proven that exchangeable tanks are a viable solution for hydrogen distribution and refueling. A public example is Universal Hydrogen which demonstrated the loading of hydrogen modules within an ATR aircraft to provide liquid hydrogen storage to the aircraft and quick exchangeability for operational needs.
The Challenges of Hydrogen Propulsion
The challenges associated with hydrogen are:
- Clean production
- Storage
- Tanks
- The volume of space occupied
- Contrails
Clean Production
Even if it is the world’s most present atom, purifying hydrogen is not trivial, and the processes that exist to generate it require power. This power shall come from renewable energies to be sustainable.
The processes of generating hydrogen also have a reasonably low efficiency: around 40%. This means that there is a need for 2.5 times more renewable energy to be produced than hydrogen consumed. Today’s renewable production is not scaled to generate the hydrogen the aerospace industry would consume.
Storage
With this comes a second challenge: storage. Hydrogen is the smallest molecule on earth which makes it almost impossible to seal in tanks. Leakage is almost inevitable, either literally through the tank structure or as a boil-off on low-temperature concepts. Hence, aviation providers are thinking about producing hydrogen near airports to use in a short time frame and avoid transportation.
Integral Tanks
Storage is not only a challenge because of potential leakage, but also because of the tanks required. Current aircraft have integral tanks – meaning that they are formed by the cavities of the regular aircraft structure. They require equipment such as pumps and valves as well as a special coating, but their mass is minimal in relation to the mass of fuel they carry. This will not be the case for hydrogen tanks. The quality of their designs is typically measured in terms of gravimetric efficiency – the mass of hydrogen stored inside the tank over the total mass of the tank and stored hydrogen. For example, a tank with gravimetric efficiency above 33% means that the combined mass of fuel and its storage will be lower than that of jet fuel. Nevertheless, it will not reach the theoretical 3x improvement of the fuel mass for the same amount of energy in comparison to jet fuel. At 33%, the combined masses will be equal.
The Volume of Space Required
As much as hydrogen’s energy density is high, its volumetric energy density is low. For a given amount of energy, hydrogen would occupy at least three times more volume than jet fuel in ambient conditions. To tackle this issue, two main streams are investigated:
- Liquefying: Liquid hydrogen requires very low temperatures (~ -250°C), with the constraints that come with it like cold management, mechanical differential dilatations, and phase change.
- Compressing: This requires pressures in the order of 700 bar (10,000 psi) to be attractive, which increases the leakage and reduces the lifetime of the mechanical parts. Thus, the hydrogen molecules infiltrate the material, impacting durability. Due to the so-called Joule-Thompson effect, heating with leakage is an additional concern.
Contrails
Lastly, even for hydrogen-powered aircraft, emissions must not be neglected. Burning hydrogen would not emit carbon dioxide (CO2), but contrails and nitrogen oxide (NOx) are a concern. Contrails today result from water vapor emitted by jet engines. The amount of water vapor in the exhaust of a hydrogen-powered aircraft would be higher, and therefore the impact must be carefully studied. Contrails only form under specific conditions, and this can be understood both as a challenge and as an opportunity. The former is because nontrivial science and involved studies may be required. The latter is because limited space and time conditions may be circumvented through rerouting.
Nitrogen oxide also contributes through several location-dependent mechanisms to climate change, but it may be much harder to avoid the relevant conditions. Additionally, nitrogen oxide production usually has increased with modern gas turbine designs. In fact, fuel burn reductions via higher thermal efficiency have previously been achieved at the cost of increased nitrogen oxide production. This is not acceptable anymore, and the resulting challenges are sometimes called the “fuel burn paradox”. For hydrogen-powered aircraft, it may well be considered to deliberately reduce the thermal efficiency of a hydrogen-burning aero engine to reduce remaining emissions. These nitrogen oxide emissions are the main argument in favor of the hydrogen fuel cell concept introduced above. This is the cleanest concept and does not emit any nitrogen oxide (only water vapor).
Solving Sustainability Challenges with System Simulation
These challenges aren’t stopping aircraft manufacturers from their efforts toward increasing sustainability for aviation. At the same time, the number of aspects to consider in the urgently required studies is large and cannot be handled without sophisticated multi-domain system simulation technology.
Modelon is supporting these organizations in this goal using Modelon Impact and its embedded extended set of libraries – covering many physical domains and applications. Studying different architectures in parallel or studying cryogenic storage, distribution, and propulsion – all in a single tool – enables better trade-offs. In addition, Modelon’s aerospace team supports customers by developing new and desired models or variants, so they can focus on designing the best technical solutions with low effort.
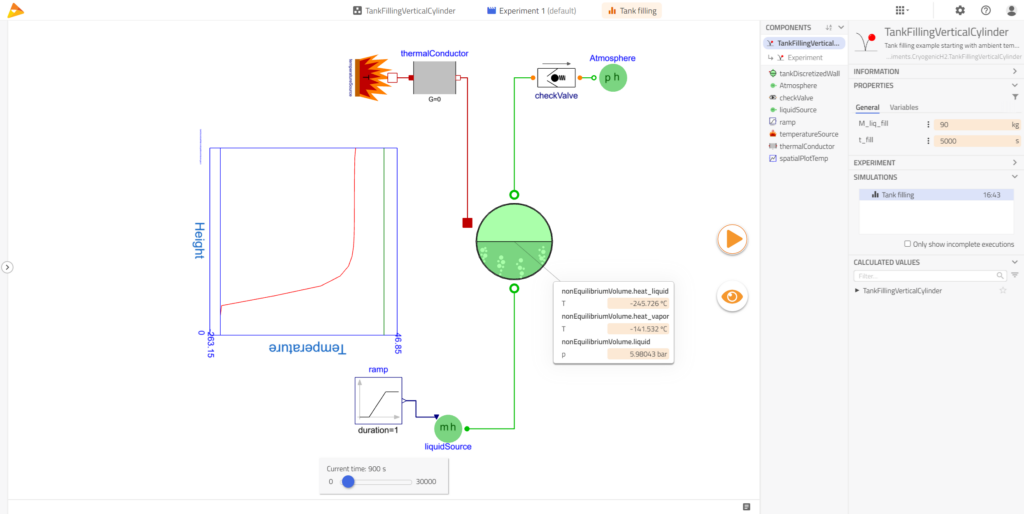
To learn more about sustainable solutions for the aviation industry, reach out to our experts!