Looking Ahead to Innovations in Aircraft Hydrogen Storage in 2024
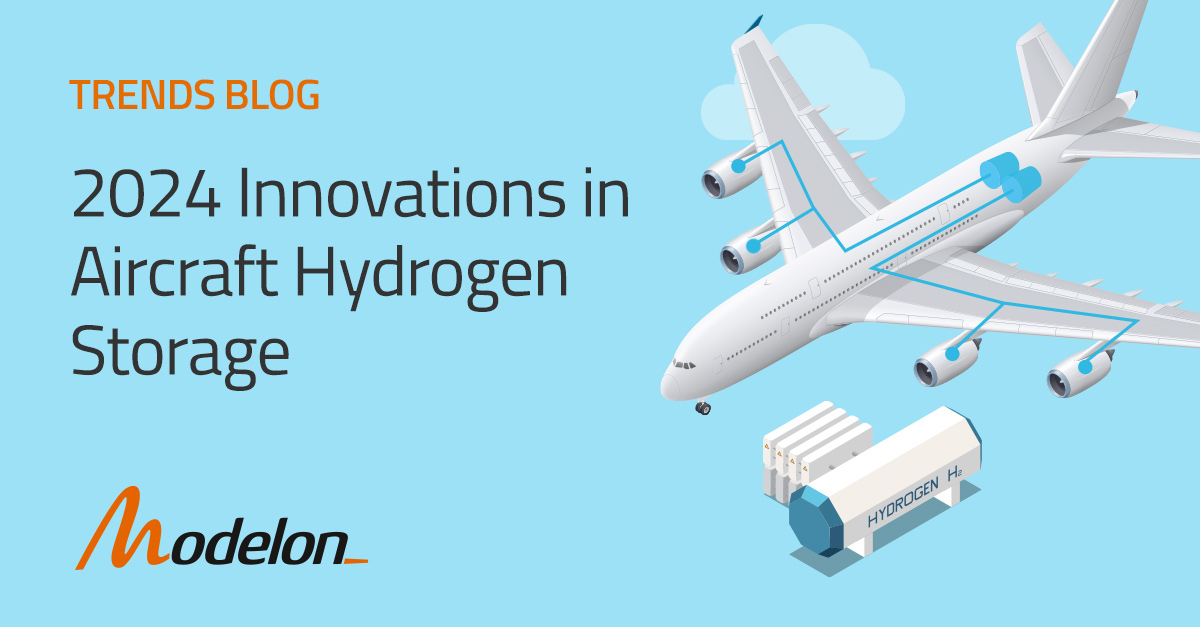
2023 saw meaningful progress in the use of hydrogen as a sustainable aviation fuel. Progress included successful test flights of hydrogen-powered fuel cell planes from ZeroAvia, Universal Hydrogen, and, notably, H2FLY, which achieved the world’s first piloted flight of an electric aircraft powered by liquid hydrogen. This milestone marked a pivotal moment in the journey toward sustainable aviation and showcased the immense potential of hydrogen-based technology in revolutionizing the industry.
In many regards, hydrogen is well-suited to flight. Hydrogen is light and energy-dense, yielding roughly three times more energy storage per unit mass than jet fuel. More importantly, hydrogen fuel cells are technically free of carbon emissions. These flights become truly carbon-free by sourcing green hydrogen produced entirely through renewable energy (as all the industry leaders plan to do).
Various challenges remain as the aviation industry attempts to accelerate progress toward a decarbonized future.
Modelon’s Aerospace Industry Director, Michael Sielemann, sees three essential design and engineering opportunities that can streamline progress for aircraft hydrogen storage in 2024: gravimetric efficiency, insulation choices, and fueling times.
1: Gravimetric Efficiency: Balancing Weight and Volume
As any frequent flyer knows, space is at a premium in any aircraft. In their current state, hydrogen storage systems take up too much space.
For example, Universal Hydrogen’s converted De Havilland Dash 8-300 turboprop (which completed a successful 15-minute test flight in March) runs a hydrogen-electric powertrain on fuel cells fueled by compressed gaseous hydrogen. Unfortunately, this plane must sacrifice 16 of the 56 seats available to make room for hydrogen storage tanks; that’s close to one-third of the seating. Even with this compromise, its range is just 400 nautical miles—roughly 20 percent of the standard fossil-fueled De Havilland Dash 8-300 turboprop’s range.
Sielemann notes, “The issue is that the tanks need to contain so much pressure, and the structure needs to sustain that. That means the tank gets extremely heavy. Yes, your hydrogen is still light, but the tanks weigh so much it’s unbelievable. It might be a hundred times the mass of hydrogen you’re carrying around.”
The tank’s weight creates additional loads, which stress surrounding structures, requiring even more structural reinforcement. The gravimetric efficiency trade-off can become a vicious cycle, resulting in a heavier plane, a smaller range, and fewer passengers onboard.
An alternate approach is cryogenic hydrogen storage. Storing hydrogen in liquid form at very low temperatures (below -253°C) allows for a higher (volumetric) energy density than gaseous hydrogen storage without such heavy tanks.
Of 2023’s three hydrogen-fueled demo flights, ZeroAvia and Universal Hydrogen both flew about 15 minutes using compressed gaseous hydrogen. Meanwhile, H2FLY’s modified Pipistrel twin fuselage Taurus 4G flew for more than three hours using cryogenic liquid hydrogen.
These units have significant differences: ZeroAvia flew a 19-seat plane, Universal Hydrogen a 40-seater, while H2FLY had an aerodynamic, extremely efficient glider. Based on their estimates, comparing the performance of their liquid hydrogen-fueled Pipistrel Taurus 4G to their gaseous hydrogen-fueled Taurus 4G, H2FLY estimates that liquid hydrogen storage doubles a craft’s range.
2: Improving Insulation
Insulation has become a vital design area due to the promise of cryogenic hydrogen as a fuel for aviation.
“Often people assume that vacuum insulation is best,” according to Sielemann. That makes sense, as anyone who has owned a high-quality travel coffee mug can attest. However, Sielemann has had the opposite experience using Modelon’s simulation modeling and assisting hydrogen engineers and design teams.
“Intuitively, we think vacuum insulation sounds great. The thing about vacuum insulation is that the thermal conductivity of the insulation is good. However, it’s also necessary to have an outer shell strong enough to resist buckling despite the evacuated void between the structural shells. That structure to support the outer shell will be quite heavy.”
This creates the same gravimetric efficiency trade-offs that made gaseous hydrogen perform poorly.
“In simulations, we’ve seen a lot of cases where foam came out much better as an insulation for cryogenic hydrogen. It sounds boring: I’m using foam to insulate my fancy cryogenic hydrogen tank. There must be something more exciting in science fiction than using foam to insulate! But at the end of the day, the vacuum insulation is often not competitive against the foam-based insulation.”
3: Decreasing Fueling Times
According to Sielemann, regardless of whether systems use high-pressure compressed gaseous hydrogen or liquid hydrogen, fueling times are a challenge. It’s not enough to build a tank that withstands specific amounts of pressure with necessary insulation while meeting specific gravimetric efficiency benchmarks.
Engineering teams must build with a specific strategy for filling the tank efficiently.
“If you design your tank, you can’t just say, okay, in theory, it needs to be this big and has to have that much insulation,” Sielemann notes. “You have to also make up your mind on how you fill it over time. With fossil fuel, you plug a hose into the airplane and flood the tank with jet fuel. That won’t work with hydrogen.”
Consider a tank for cryogenic hydrogen: If you begin filling the tank at ambient temperature, it’s the same as pouring cool water into a hot kitchen pan: the hydrogen hits the tank and turns to vapor. The vapor gets trapped beneath the incoming liquid hydrogen, effectively insulating the liquid from the surface and maintaining the evaporation of new incoming liquid.
“You cannot fill the tank with the liquid hydrogen without a strategy,” Sielemann says, “because everything that you’re putting in there is evaporating too quickly, building up pressure. At the end of your refueling operation, you will mostly have vapor in the tank and maybe 5 percent liquid hydrogen. That’s not going to take you where you need to be.”
Sielemann estimates that, given current designs and strategies, refilling a hydrogen-fueled aircraft might take twice as long as conventional fueling—which is a problem in many modern air travel or logistics applications.
“A lot of the design problems that Modelon is called in to help model right now concern how to consume the hydrogen and refill the tank efficiently,” Sielemann says.
Moving Ahead with Hydrogen Fuels in the Aviation Industry
Modelon works with aviation engineers to continue developing hydrogen fuel systems as efficiently as possible. Adopting comprehensive physics-based models delivers more accurate data related to hydrogen storage, extraction, and distribution, bringing more efficient, lower-cost solutions to the aviation market more quickly.
Reach out to our experts and let us help bring hydrogen-powered flight to runways around the globe.