More Electric Aircraft: Sub-System Design, Integration, Performance, and Optimization
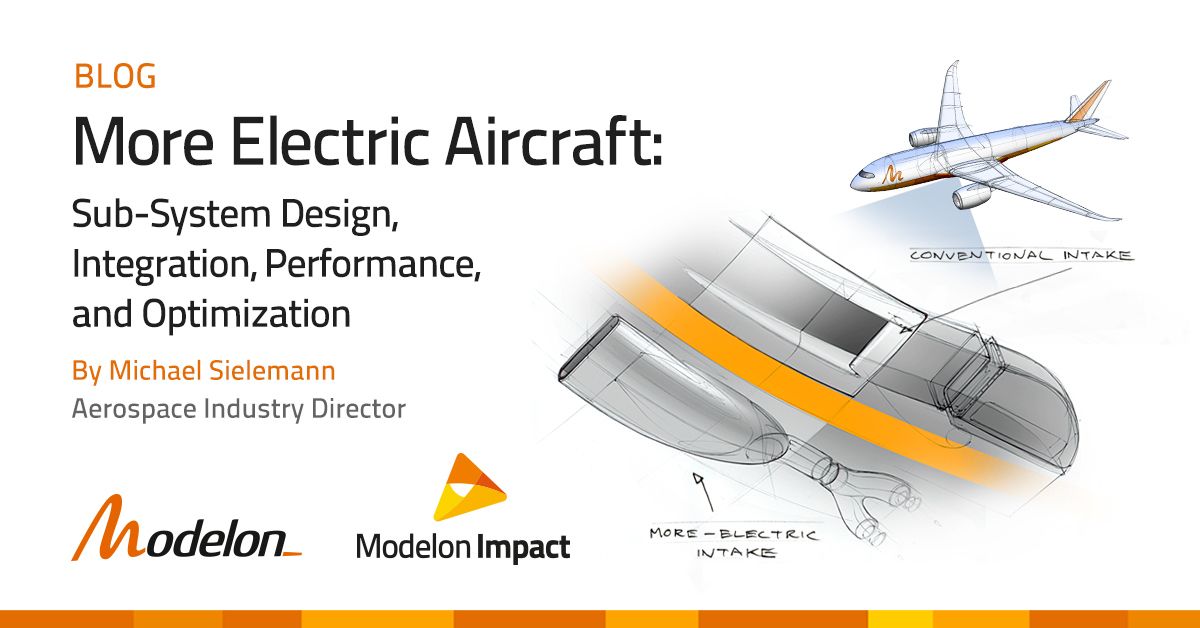
In this blog post, Modelon’s Aerospace Industry Director, Michael Sielemann, introduces the More Electric Aircraft concept and covers how modeling and simulation are shaping the way vehicle sub-systems are designed and integrated.
More Electric Aircraft: Vehicle Sub-System Design and Integration
More Electric Aircraft vehicle sub-systems are what remains once the mechanical structure of the aircraft (so-called “airframe” consisting of wings, fuselage, tail) and the propulsion (podded “aero engines” or commonly “turbines” below the wing) have been removed. In other words, the vehicle sub-systems provide essential functions to reach mission objectives beyond aerodynamic lift, structural integrity, and propulsive thrust.
On today’s commercial aircraft, vehicle sub-systems provide key onboard functions such as de-icing on the outside of the aircraft or powering actuators that move control surfaces and the landing gear. In an automotive application, this would be comparable to the braker booster, power steering, air conditioning, or power window lift.
Traditionally, aircraft vehicle sub-systems have been powered by a mix of pneumatic, hydraulic, and electric power – called secondary or non-propulsive power. In the 2000s, driven by demand to optimize performance while decreasing operating and maintenance costs, the first More Electric Aircraft appeared with the Boeing 787 and Airbus A380. These manufacturers began pushing toward More Electric Aircraft – leaving the traditional vehicle sub-system architecture behind – reducing the use of pneumatic and hydraulic power while increasing the use of electric power.
This advanced architecture, More Electric Aircraft, embodies the latest design and integration insights offering many advantages including reduced emissions and decreased maintenance costs. Electric cables do not leak, so some key advantages of More Electric Aircraft vehicle sub-systems are reliability and lower maintenance costs. Complexity can also be substantially lower. The following section describes this in more detail.
The ability to utilize electric power for all non-propulsion systems requires careful analysis of performance, system and controls optimization, integration, and validation.
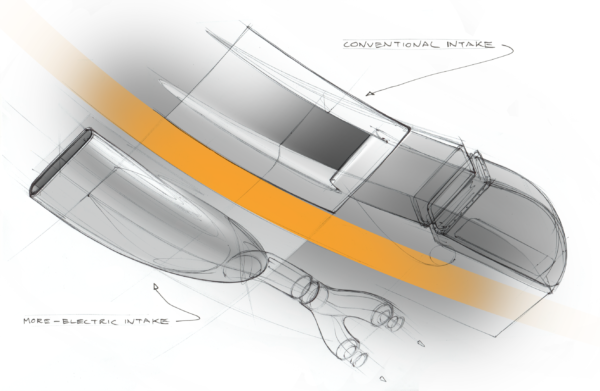
More Electric Aircraft: Performance and Optimization
The main challenge of More Electric Aircraft lies in the overall performance, which is influenced by more factors than just energy efficiency. For commercial aircraft, overall performance is typically measured in payload vs. range or simply mission block fuel consumption. Vehicle sub-systems influence this by:
- Energy demand and efficiency – how much useful work is done and wasted by the vehicle sub-system
- External aircraft drag increments – how much does the aerodynamically ideal aircraft shape have to be altered to accommodate the system
- Mass – how much extra lift must be generated by the aircraft to carry the vehicle sub-system mass, leading to additional aerodynamic drag based on the current lift-to-drag ratio
How does this play out on the commercial aircraft environmental control (air conditioning and pressurization) system, for instance? When using pneumatic air from an aero-engine gas turbine core, the conventional air cycle machine has reasonable but not great efficiency (air is used as fluid in the refrigeration cycle). This results in a low aircraft drag increment (capturing ambient ram air as heat sink incurs a few drag counts but a single flush intake per side is sufficient) and low mass. A more electric design using cabin air compressors eliminates the engine bleed air system, which improves mass and energy efficiency. However, it also adds several components including a second ambient air intake that feeds fresh air to the cabin air compressor. Due to the required pressure ratios, high intake pressure recovery and the use of a scoop intake is required, which increases the aircraft external drag in relation to a flush intake. The more electric design is only worthwhile with the right combination, so careful bookkeeping of all factors influencing overall performance is essential.
All vehicle sub-systems call for optimization, but the details often differ. Traditionally, hydraulic oil typically provided power through a piping network to actuators distributed throughout the aircraft. These actuators can also be replaced with electro-mechanical ones using ball screw drives or electro-hydrostatic actuators with a local hydraulic pump instead of the full hydraulic network. Here, the network is a degree of freedom in the trade-off. Safety can also be a challenge because, in some instances, certain parallel actuator designs require that the actuator can move freely in case of failures, which is impossible for plain screw drives.
More Electric Aircraft Capabilities in Modelon Impact
Electrification of vehicle sub-systems happens gradually, and the most recent Airbus A350, for instance, has electro-hydro static actuators but no electric environmental control system. So, the right decisions for considering development cost and risk need to be made carefully. The complexity of trade-offs can only be assessed by the complete system optimization which Modelon offers. Modelon Impact Pro comes with open model libraries covering the full range of vehicle sub-systems, airframe, and propulsion perimeters.
- Modelon’s Aircraft Dynamics Library comes with parametric aircraft models, which allow you to scale your commercial aircraft platform, capture so-called snowball effects given vehicle sub-system mass, and quantify the mission block fuel impact of all given factors.
- Modelon’s Environmental Control Library delivers ram air intake models, which predict the aerodynamic drag based on flight conditions and captured flow.
- Modelon’s Heat Exchanger Library allows you to parameterize simple and complex heat exchanger geometries and predict their mass.
- Modelon’s Hydraulics Library enables you to design actuators based on a range of force vs. speed requirements.
- Modelon’s Electrification Library provides flexible electric machine models, which expose the design trade-off between installation space, available cooling, mass, and performance.
- Modelon’s Jet Propulsion Library predicts the impact of secondary power off-take in terms of shaft power and customer bleed air on aero-engine fuel consumption using any cycle and design/off-design condition.
And, finally, More Electric Aircraft requirements are a key ingredient to the Modelon development roadmap.
More Electric Aircraft architectures offer break-through performance improvements, reduced emissions, and decreased maintenance costs. But More Electric Aircraft also introduces engineering challenges due to the delicate trade-off between factors such as energy efficiency, external drag, and vehicle sub-system drag as well as the introduction of electrification components. Modelon Impact is a platform that can address these issues efficiently through built-in yet customizable model libraries, an advanced mathematical engine for simulation and optimization, and customizable workflows ranging from micro-scripts in interactive mode to analysis notebooks and web apps enabling collaboration. This platform is backed up by Modelon’s world-class content and subject matter expertise. Modelon can help, so reach out!
The More Electric Aircraft concept differs from hybrid, electrified, and fully electric aircraft, which focus on aircraft propulsion (not vehicle sub-systems). A hybrid or electrified aircraft uses a conventional engine (gas turbine or internal combustion) combined with an electric power system, and a fully electric aircraft does not require fuel but is entirely driven by electric energy storage such as batteries. Check out our other blogs on the Electrified Aircraft and Boosted Turbofan for more practical insights!