Model-Based Systems Engineering for Aircraft Engines
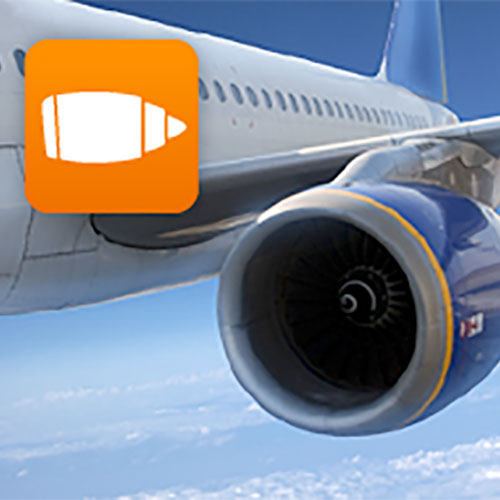
Modelon’s Jet Propulsion Library provides the foundation for modeling and simulating jet engines along with the integrated model-based systems engineering of aircraft systems.
Why start optimizing
The prime mover of an aircraft, the jet engine, is one of the most important subsystems of an aircraft. Jet engines provide primary power (thrust) and secondary power (to drive flight control, air conditioning, cabin lighting, etc.) to the aircraft. Performance and efficiency improvements are becoming increasingly difficult to achieve when focusing on the engine in isolation. In the past, engine improvements have largely been developed separately in incremental design cycles – these cycles have not considered the need to develop the total aircraft package as an entire unit. Today, aeronautical systems and their subsystems are becoming more and more integrated and therefore simulation models need to become further aligned to meet performance and efficiency needs.
How the Jet Propulsion Library can help
Modelon’s Jet Propulsion Library offers a comprehensive set of components that empower cycle performance analysis and optimization of all types of aerospace gas turbines. All component implementations properly distinguish static and total quantities, and rely on fully rigorous thermodynamic properties. This means that for accurate results, no undesirable simplifications are made in the thermodynamic property computations (such as if the isentropic exponent is constant across the reversible transformation between static and total quantities). Additionally, the behavior encoded in all component models can be scaled using on-design and off-design steady-state performance computations.
Component models include:
- Engine Inlets – used to model the behavior of key coefficients, for example ram pressure
- Burners – modeled primarily via efficiency and Rayleigh pressure loss
- Compressor and Turbine – models contain performance maps based on the industry-standard notation
- Nozzle – models can quantify nozzle exit gross thrust coefficient, or nozzle exit velocity coefficient
Modelon’s Jet Propulsion Library differentiates itself from competitors, allowing users to integrate aircraft systems and simulate the behavior of an entire system. The functionality to integrate components and systems is enabled using Modelica, the leading model language standard. This language standard brings significant benefits to systems engineering including seamless collaboration, knowledge sharing, IP protection, and ensures your investment will continue delivering returns in the future.
This integrated design leverages model assets across the design cycle from on/off design computations via transient simulation. With an open and modular approach, and integration with all relevant sub-systems and physical domains, end-to-end performance improvement applications including thermal management and fuel systems get within reach.
Performance improvement applications include:
- Fuel Systems – analyses of fueling/refueling, as well as inertia and flammability simulations
- Hybrid Propulsion – combining classic with electric power system technology
- Multi-Domain Dynamics – combining hybrid electric and so-called “More Electric Aircraft” (aircraft with increased use of electric secondary power for the aircraft sub-systems)
- Thermal management – adjusting thermal constraints without deteriorating performance
These applications are just a few examples of how our library model and components are integrated and aligned to meet overall performance and efficiency needs. Further applications can be covered with Modelon’s off-the-shelf libraries or in-house model assets. Modelon’s open-standard structure enables this model-based design approach.