Electrified Aircraft: Boosted turbofan concept propels research and development
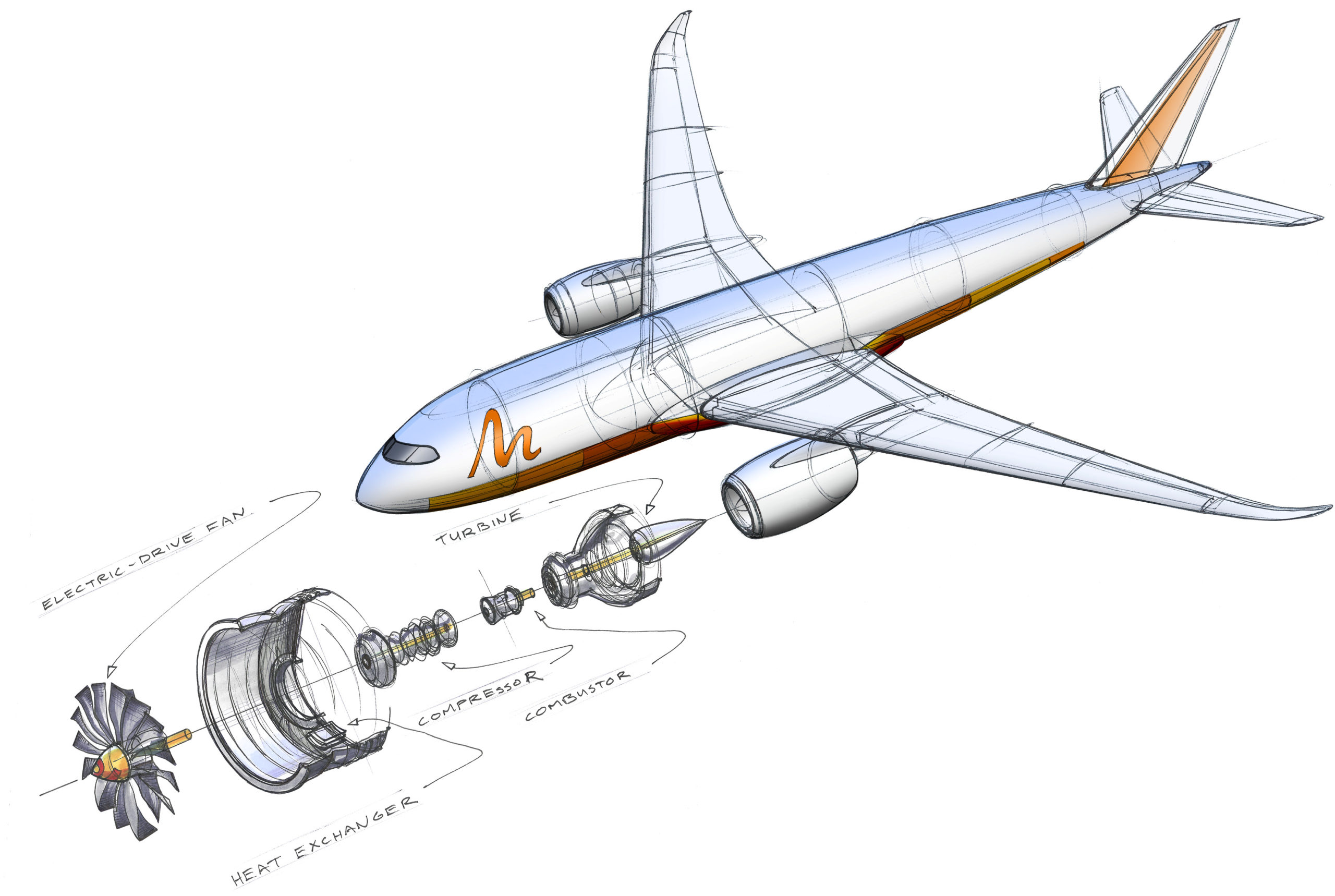
This blog is a continuation of Electrified Aircraft: What Is It and Why Is It Important?
Overview
Modelon is proud to be a collaborative partner in the Turbo electRic Aircraft Design Environment (TRADE) project, funded by the Clean Sky 2 Joint Undertaking – under the European Union’s Horizon 2020 research and innovation program.
This research development is primarily focused on configuring and analyzing the capability of electric machines and batteries to add electric power to the fans of gas engines – also known as the boosted turbofan engine concept. In order to study this and similar concepts, the consortium developed a simulation and optimization design platform with analysis models of higher fidelity for hybrid electric aircraft.
Boosted Turbofan Engine Concept
In the research completed for the TRADE program, the boosted turbofan concept features a base configuration of a standard turbofan gas turbine engine. The “boost” comes from an electric drive that is mounted on a spool of the gas turbine or on an accessory drive shaft. Benefits of using the boosted turbofan concept include:
- Simple installation: The overall design of the aircraft does not require a lot of modification. For example, the aircraft can still have podded engines attached below the wings.
- Simple analysis: The aircraft design still features common propulsion devices, components are generally found in the same locations, and the balancing of jet fuel and electric energy occurs in electrified gas turbines.
But, how is a concept like this tested and validated?
Subsystem and System Simulation with Modelica
Using Modelon’s Aircraft Dynamics Library, a Modelica-based library, we had the flexibility to build and layer multiple architectures and topologies, as well as fidelity and abstraction levels to validate the boosted turbofan concept.
Figure 1.
In Figure 1, you can see a simple experiment that displays one aircraft and models of the surrounding, including:
- The flat earth or ellipsoidal ECEF coordinate system, a model of the height and friction coefficient of the ground, and ambient conditions;
- The parametric aircraft model, including passive aircraft structure, power and propulsion system, and consumer systems;
- And the landing gear.
The benefit of using Modelica-based technology is that the multi-level configurations allowed us (the consortium) to separate the complete architecture from the model configuration for expert analysis (See Figure 2).
Figure 2.
Using Modelon’s Jet Propulsion Library and Electrification Library, part of the Modelon Library Suite, we could implement parametric sub-system models. Once the complete system and all subsystems were in place (Figure 3), we began testing and validating the boosted turbofan concept.
Figure 3.
Consortium Work
Electrical Power System – University of Nottingham (United Kingdom) led the design and modeling of the electrical power system. This covers the batteries as electrical power storage system, the power electronic converters, and the electrical machines. New component and sub-system models are gradually integrated into Modelon’s Electrification Library and will be shipped with a future release.
Gas Turbine – Mälardalen University (Sweden) led the design and modeling of the gas turbine aero engine of the hybrid electric aircraft. This covers the gas turbine core or gas generator and the geared fan. New component and sub-system models are continuously integrated into Modelon’s Jet Propulsion Library such as the geared turbofan model shipped with the 2019.2 release.
Thermal Management – Modelon and Mälardalen University (Sweden) jointly led the design and modeling of the thermal management system. This covers the air-cooled oil cooler heat exchangers, pumps and plumbing. Component and sub-system models are largely available in Modelon’s Liquid Cooling Library and Heat Exchanger Library and extensions are shipped with regular library releases.
Interfacing via Common Parametric Aircraft Configuration Schema (CPACS) – Implemented by Modelon – A substantial amount of data was exchanged via the CPACS XML dialect. This is used to exchange geometry and mass data. The functionality was implemented via Modelon DataAccess, which is shipped with every product in Modelon Library Suite. The functionality was described in a previous post.
Testing and Validation
In order to benchmark the boosted turbofan concept, we created a gas turbine baseline. This baseline included a conventional geared turbofan (GTF) for DLR’s single aisle commercial aircraft configuration D150 and technology levels for Entry-Into-Service 2035. Our baseline analysis considered climb rates, step-up cruise, available fuel, and thrust.
From there, we started defining the concept of operations for the boosted turbofan by analyzing baseline GTF safe operation – i.e., surge margin. This identified mission segments suitable for electric boost but also segments that require battery charging instead of boosting or conventional handling bleed. We then studied ways to handle power peaks more efficiently, using the electrical system to level out the power peaks beyond the essentially constant gas turbine load. We also examined the dynamics of the climb operation to identify the optimal design to maintain level power requirements. The electrified propulsion sub-system was integrated with a thermal management sub-system and assessed on aircraft level.
Results and Conclusions
Based on our TRADE assumptions and models, different levels of block fuel were burned for the baseline and boosted turbofan engines. These burn levels varied depending on the mission range (Figure 4). Our results also showed that increasing the range improved the block fuel benefit of the boosted turbofan over the baseline gas turbine due to cruise SFC improvement. In fact, longer ranges showed a block fuel benefit of approximately 3.5 percent.
Figure 4. From “The boosted turbofan for electrified aircraft: the TRADE perspective”, Electric & Hybrid Aerospace Technology Symposium 2019.
Such results are encouraging, but the bottom line is that the block fuel burn benefit is highly dependent on achieving ambitious weight and efficiency targets on sub-system level. Many open questions remain for engineers to solve before these targets can be met. In any case, flexible modeling and simulation technology is a critical enabler to resolving these engineering challenges. Later this year, we unveil a second configuration including assessment results. Remember to check for more details soon!
Read up on all technical details in the following scientific publications:
Zhao, X., Sahoo, S., Kyprianidis, K., Sumsurooah, S., Valente, G., Rashed, M., Vakil, G., Hill, C. I., Jacob, C., Gobbin, A., et al., “A framework for optimization of hybrid aircraft,” ASME Turbo Expo 2019: Turbomachinery Technical Conference and Exposition, American Society of Mechanical Engineers Digital Collection, 2019.
Zhao, X., Sahoo, S., Kyprianidis, K., Rantzer, J., and Sielemann, M., “Off-design performance analysis of hybridised aircraft gas turbine,” The Aeronautical Journal, Vol. 123, No. 1270, 2019, pp. 1999–2018.
Valente, G., Sumsurooah, S., Hill, C.I., Rashed, M., Vakil, G., Bozhko, S., and Gerada, C., “Design Methodology and Parametric Design Study of the On-Board Electrical Power System for Hybrid Electric Aircraft Propulsion,” The 10th International Conference on Power Electronics, Machines and Drives, The Institution of Engineering and Technology, 2020.
Hecken, T., Zhao, X., Iwanizki, M., Arzberger, M. J., Silberhorn, D., Plohr, M., Kyprianidis, K. G., Sahoo, S., Sumsurooah, S., Valente, G., Sielemann, M., et al., “Conceptual Design Studies of ‘Boosted Turbofan’ Configuration for short range,” AIAA Scitech 2020 Forum, American Institute of Aeronautics and Astronautics, 2020.
Acknowledgment
We acknowledge the pivotal contributions of our academic consortium partners, who led the initial study and model implementation efforts.
This project has received funding from the Clean Sky 2 Joint Undertaking under the European Union’s Horizon 2020 research and innovation programme under grant agreement number 755458.