Aircraft System Simulation for Reducing Carbon Dioxide Emissions
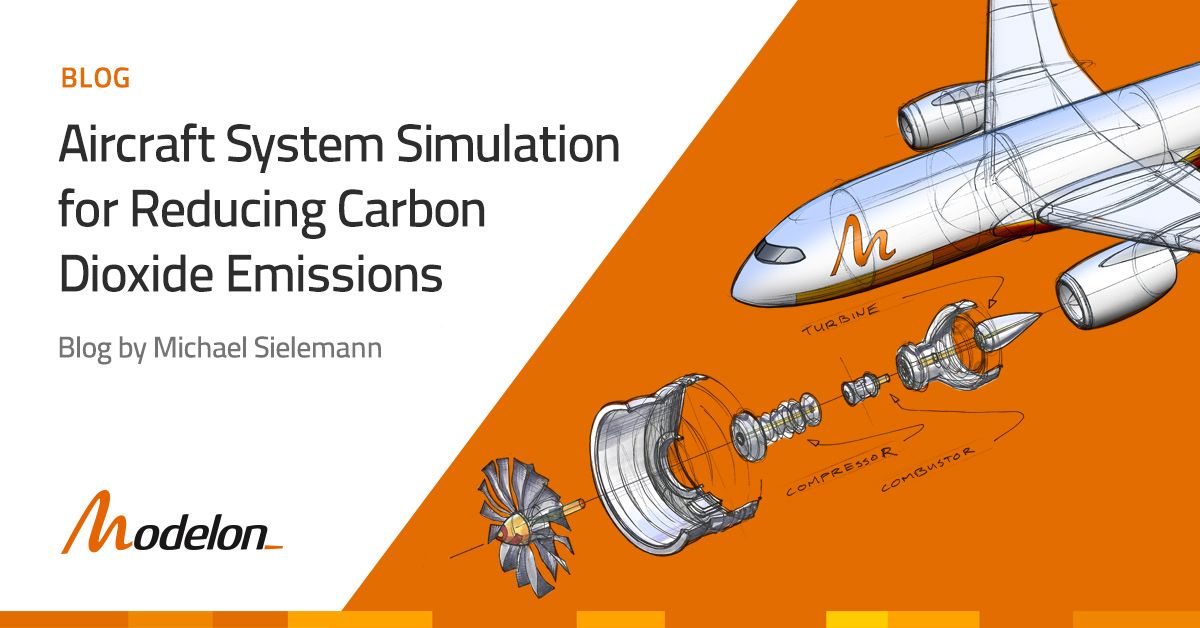
Aircraft system simulation software is essential for companies designing electrified aircraft to reduce carbon dioxide emissions. Modelon Impact coupled with our team of experts is leading the way. The content below was originally published in Skyline, by the Clean Sky 2 Joint Undertaking – under the European Union’s Horizon 2020 research and innovation program.
Despite the current downturn in travel, due to COVID-19, aerospace companies remain committed to designing aircraft that will meet performance and efficiency needs. The long-term need for reduced emissions while maintaining performance has not changed. Modelon is proud to be bridging the gap between public interest and private industry to lead and advance this research.
For decades, aerospace companies have addressed emission reductions by focusing on component technology, such as a new heat exchanger or electric drive. Today, this alone is nothing. Model-based systems engineering is the key to understanding how a holistic system will perform. Modelon’s software for aircraft system simulation is based on the open standards of Modelica and is the enabler for this advanced research and catalyst for innovation.
“Modelon’s Modelica-based technology, along with our team of industry experts, is leading the way in integrated aerospace design. In CleanSky, Modelon was appointed as the coordinator for the TRADE (Turbo electRic Aircraft Design Environment) research project. What a privilege it has been” says Michael Sielemann.
For the last three years, the consortium with Universities of Mälardalen (Sweden), Nottingham (UK), and Berlin (Germany) worked on computational models for systems design and integration of hybrid-electric aircraft. This research development was focused on configuring and analyzing the capability of electric machines and batteries to add electric power to the fans of gas turbine engines – such as the boosted turbofan engine concept. Modeling with this concept gives industry experts an insight into the efficiency needs for aircraft system simulation.
Boosted Turbofan Engine Concept In Aircraft Design
The boosted turbofan concept features a base configuration of a standard turbofan gas turbine engine. The “boost” comes from an electric drive that is mounted on a spool of the gas turbine or on an accessory drive shaft. Benefits of using the boosted turbofan concept include:
- Simple installation: The overall design of the aircraft does not require a lot of modification. For example, the aircraft can still have podded engines attached below the wings.
- Simple analysis: The aircraft design still features common propulsion devices, components are generally found in the same locations, and the balancing of jet fuel and electric energy occurs locally in electrified gas turbines.
Aircraft System Simulation and Subsystem Development
In order to study this concept, the consortium created a simulation and optimization design platform with analysis models of higher fidelity for hybrid-electric aircraft. Powered by Modelon’s Aircraft Dynamics Library, we had the flexibility to build and layer multiple architectures and topologies, as well as fidelity and abstraction levels to validate the boosted turbofan concept.
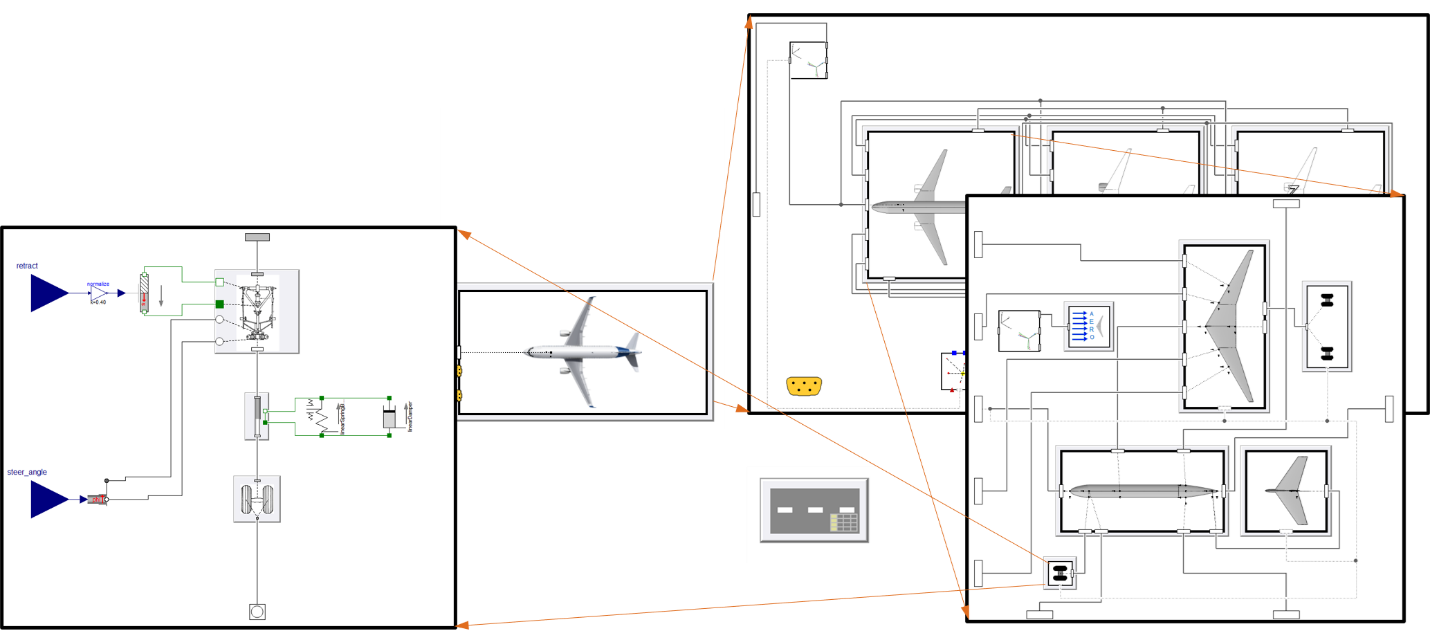
In Figure 1, you can see a simple experiment that displays one aircraft and models of the surrounding, including:
- The flat earth or spherical coordinate system including ground and ambient conditions.
- The parametric aircraft model, including airframe, power and propulsion system, and consumer systems.
- And the landing gear.
Modelica-based technology enables multi-level configurations – separating the complete architecture from the model configuration for expert analysis (Figure 2).
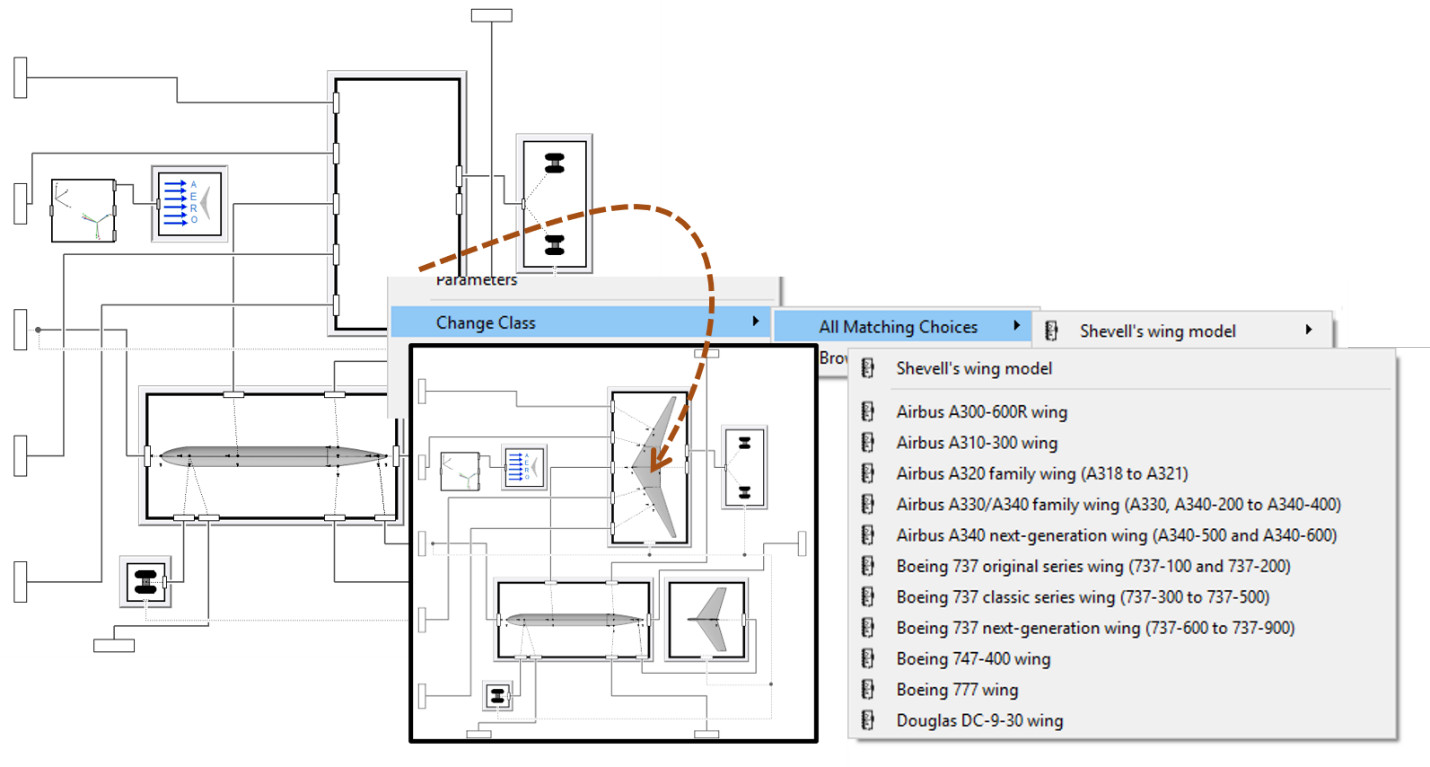
Modelon’s Jet Propulsion Library and Electrification Library let the consortium implement parametric sub-system models. Once the complete system and all subsystems are in place (Figure 3), experts allow testing and validating the boosted turbofan concept.
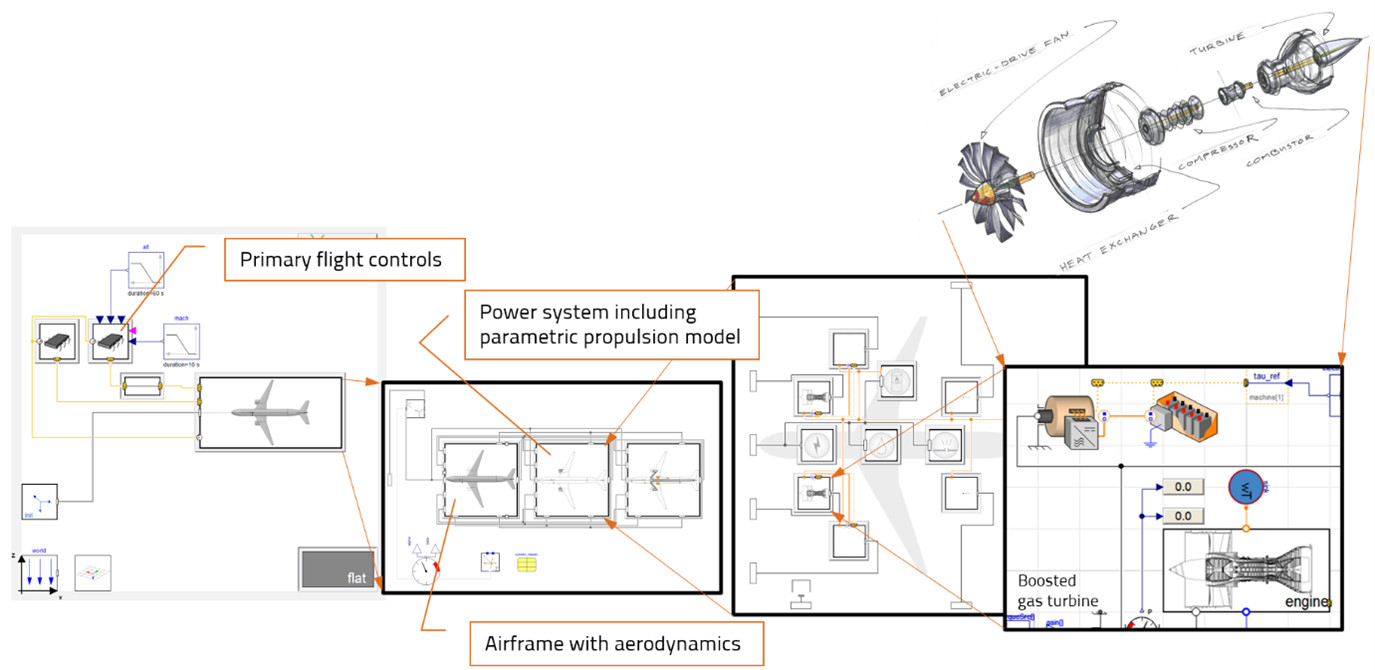
The TRADE models and engineering insights of this and the turbo-electric concept were provided to aircraft designers, who already master the engineering of other, more established aircraft system simulation concepts. Users included the German, French, and Dutch aerospace centers as well as Airbus.
Modelon Impact Enables Insight Into Emission Reductions
We have big plans for the future. After working on systems design and integration for more than 20 years, our company launched its cloud-based simulation platform, Modelon Impact. As evident from the above, a new age of engineering is upon us, where the design and integration of future physical systems are especially complex. Until now, gaps in the physical modeling toolchain and high barriers to entry have prevented many organizations from fully leveraging the benefits of simulation. By focusing on aircraft system simulation, aerospace companies have found insight into emission reductions with Modelon Impact. Modelon Impact is a platform that inspires collaboration and creates value in systems modeling and simulation. More minds bring more experience, creativity, and ultimately better results.
This project has received funding from the Clean Sky 2 Joint Undertaking under the European Union’s Horizon 2020 research and innovation programme under grant agreement number 755458.