Enhancing Design and System Performance for Direct Combustion Boilers
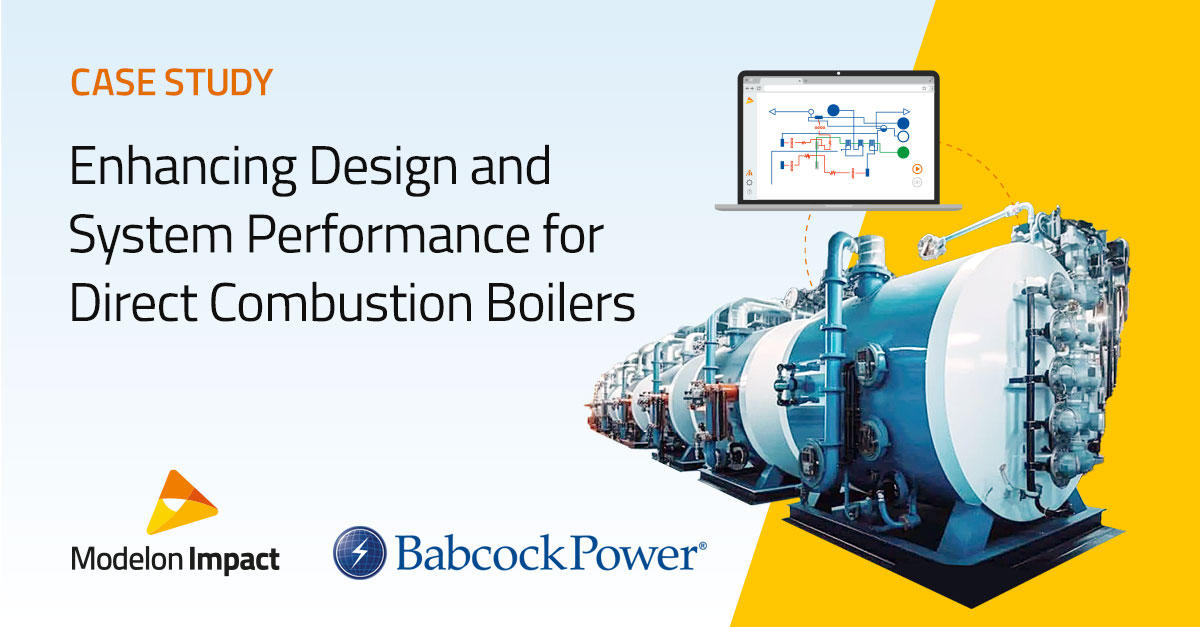
Babcock Power uses Modelon Impact to predict and improve utility-scale boiler performance in a changing energy landscape, incorporating new fuels and renewable energy sources.
Global energy production is evolving to help slow the effects of climate change. When implemented properly, renewable energy and other intermittent sources can cut carbon emissions, perform well in diverse scenarios, and be cost-effective. The increase in renewable energy production provides unique challenges to existing fossil plants that have historically been base load and are now routinely used as either peak or load following units. This puts strain on all plant systems, as they respond to changing demand by adjusting temperatures, pressures, and flows. Babcock Power is the global leader in energy-related products and services including natural gas conversions and additions.
With several business units serving customers for more than 100 years, they seek to maintain the highest levels of quality while innovating to meet the needs of a changing world. Babcock Power is now routinely asked to help optimize a unit’s ability to ramp. This requires the ability to predict performance across a range of fuels, as well as capture the short-term effects related to a load change, while keeping tools flexible enough to deal with the many unique configurations of boilers that exist.
Challenges
Achieving high efficiency is crucial to minimize operating costs and environmental impact when designing and operating a utility-scale boiler. Utility-scale boilers operate under high pressures and temperatures, which pose a few inherent safety challenges. Robust safety features, emergency shutdown systems, and adhering to regulatory standards are essential to prevent failure. Additionally, Babcock Power must assess the ramps’ impact on the boiler and its associated equipment to ensure the system stands the test of time.
Michael Johnson, a Senior Engineer at Babcock Power, emphasizes these challenges:
“If we want to incorporate renewables quickly and effectively, understanding how existing boilers respond to varying loads and fuel sources is crucial. We always want to find and leverage the best tools. System modeling and simulation are key parts of our engineering tool chain.”
Traditional analysis of boiler systems is performed in steady state. However, steady-state simulation does not predict short-term changes, such as those seen during load ramps, which occur frequently in the new energy landscape. Transient simulation is essential when designing and simulating a utility-scale boiler.
Babcock Power built and leveraged in-house system modeling and simulation software, feeding back decades of expertise into the system. In-house tools are flexible but often require building and validating numerous component models. Babcock Power’s requirements outpaced their in-house tools’ capabilities when developing the utility-scale boiler.
To model and simulate utility-scale boilers, Babcock Power looked for a system modeling and simulation tool capable of:
- Robust transient simulation
- Customizing pre-built component and media models
- Validating and tuning models using operating data
- Modeling systems with fundamental physics
- Recreating existing workflows from in-house tools
Solutions
Babcock Power chose Modelon Impact to improve its modeling abilities for utility-scale boilers.
As a Modelica-based system modeling and simulation tool, Modelon Impact gave Babcock Power critical customization abilities. Combining validated library components from Modelon’s Thermal Power Library with Babcock’s proprietary code was crucial to developing the model. In addition to Modelon Impact’s drag-and-drop user interface, Babcock Power’s team can edit the model’s code, which synchronously updates the graphical representation of the model.
Michael Johnson explains the advantages:
“Modelon Impact allowed us to build a robust transient system model. The pre-built components enable us to focus on improving our designs rather than starting from scratch. Their customer success team consistently answered questions and were hands-on in helping us make progress.”
With Modelon’s experts, the Babcock Power team built a hierarchically structured model consisting of a master model and many component models. This structure allowed subcomponents to be added, removed, or replaced with modules of different levels of detail.
The power plant system leveraged the Thermal Power Library’s pre-built sub-models and media property models. The model matched the original and modified drawings of the power plant operated by one of Babcock’s customers.
The model includes a multi-fuel combustor subsystem model, a boiler with multiple heat exchangers transferring heat from the hot flue gas to the water steam cycle, and a steam turbine model. The heat transfer model consists of the radiant furnace, and a back pass containing lower-temperature convective heat transfer modules.
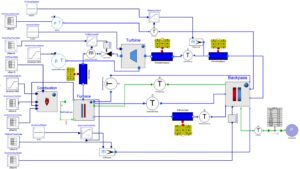
With a detailed boiler and simple plant model, Babcock Power began using operating data to validate and fine-tune their model. The accuracy of the operating data was critical to calibrating the model. Operating data was collected at 10-minute intervals, and intervals of interest were identified from a year’s worth of operating data. Steam temperatures, pressures, flow rates, flue gas temperatures, and O2 concentration were all included in the data set. The operating data helped define the typical operating range and established the base loads when tuning the model.
Results
With help from Modelon’s industry experts, the model was able to characterize the physical unit’s performance and provide valuable predictions about its behavior during transients.
Babcock Power’s models can more effectively calculate appropriate ramp rates for units following load and help predict future performance when using different fuels under real-world operating conditions. The tuned models provide valuable insight into a system’s behavior that wouldn’t be possible with steady-state simulation or in-house tools alone.
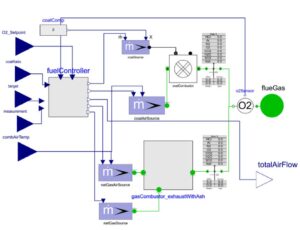
As Michael Johnson explains, “Predicting and managing ramp rates is essential for the safety and longevity of our customers’ power plants. Doing transient analysis of the model in Modelon Impact gives us insights to share with our customers and increases their confidence in our offering.”
A detailed approach to modeling and simulation serves Babcock Power and its customers in the short and long term. Operations and maintenance strategies are made using reliable data. As control strategies are improved, the maintenance requirements for the load following units can be reduced by limiting stresses on key components.
“Our collaboration with Modelon helps us stay at the forefront of our industry. We can make more informed engineering decisions that lead to safer and more reliable power generation,” Michael Johnson concluded.
Modelon Impact and our energy experts exceeded Babcock Power’s initial requirements for a modeling and simulation platform. The utility of our pre-built libraries, cloud-native platform, and our team’s knowledge enabled strategic decisions for Babcock Power as they deliver a more sustainable energy industry.