【事例研究】発電所における運転操作の改善
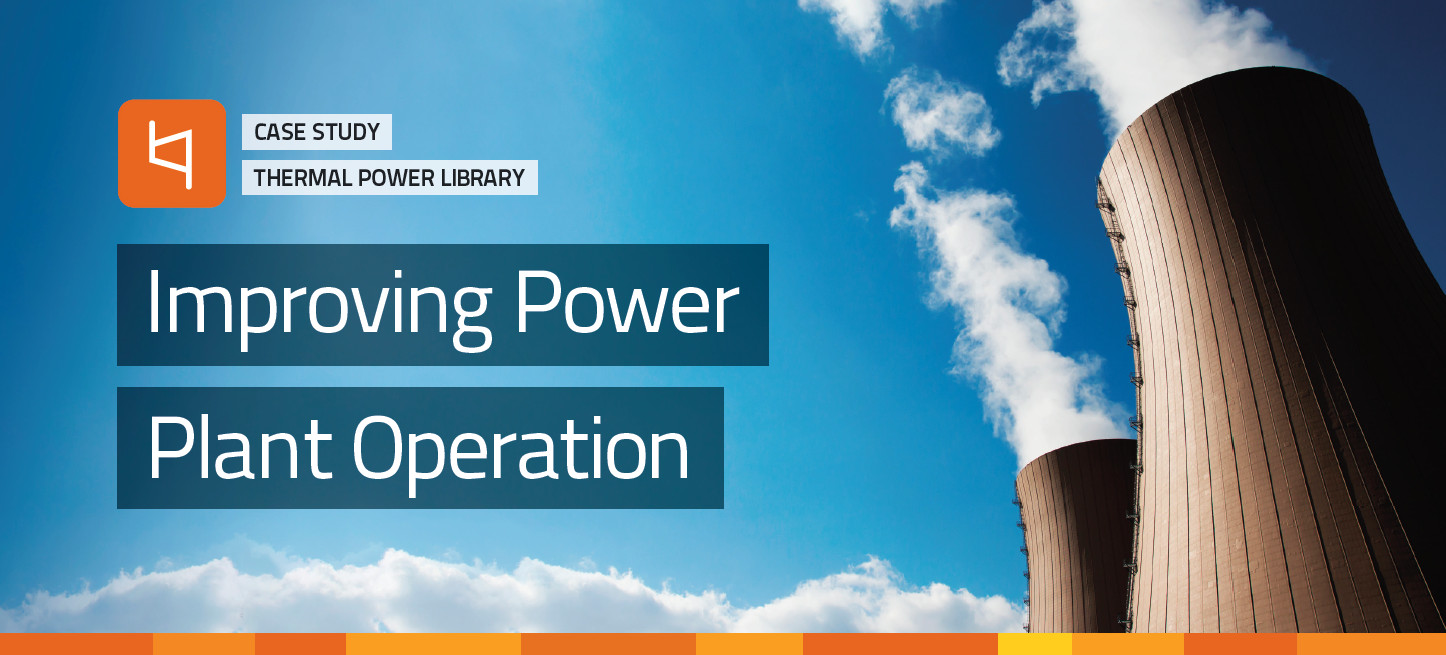
MORITZ HÜBEL, JOHAN WINDAHL
JUNE 12, 2017
This blog piece reviews and summarizes our newest case study. Detailing how one of Germany’s largest thermal power plants has improved their primary control reserves; resulting in an electric grid that can integrate a higher number of renewable energy sources, including wind and solar.
Why is balancing an electrical grid’s energy sources important? With multiple energy sources, an energy company can garner greater stability at reduced costs. To enable a system to integrate these multiple energy sources like wind and solar, new and existing plants need to be optimized in areas focused on load change rate, start-up time, minimum load and control reserves.
In a recent research collaboration, Modelon, the University of Rostock, and Vattenfall (one of Europe’s leading generators of electricity and heat) set out to improve the flexibility of the German power plant referenced above.
Modelon’s Thermal Power Library enabled researchers to develop a model consisting of different sub-sections, coupled through fluid-connections and a control signal bus. Nearly 11,000 differential-algebraic equations are used to describe the system which includes about 500 thermodynamic states.
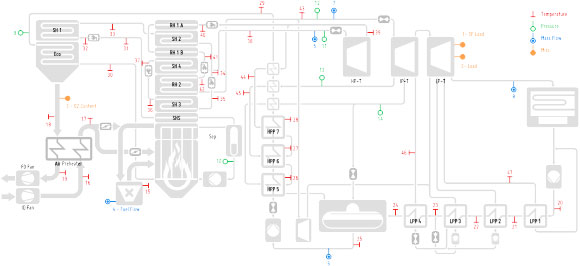
To ensure accuracy, model results were used to measure the deviation between measured and simulated values. In total, 47 reliable measurement points from the power plant were chosen to evaluate the accuracy of the model.
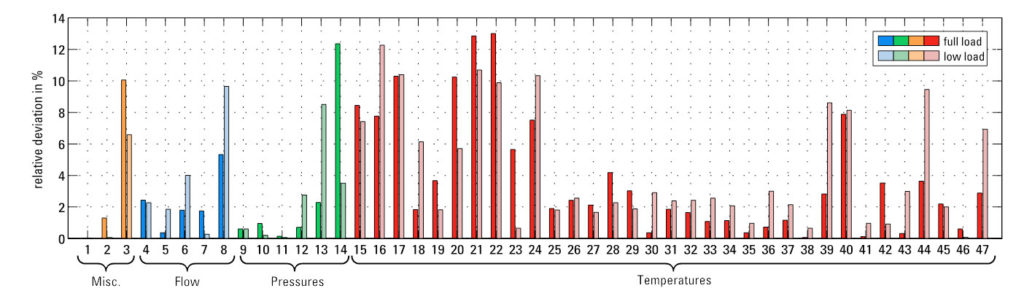
Next, utilizing the available detailed model in Modelon’s Thermal Power Library, accurate parameter identification could be performed. The results from the model could determine that the main block control oversteers the fuel flow too aggressively. By tuning the oversteering parameter in the block control, using the detailed dynamic power plant model, the control quality for the prequalification test increased significantly – reaching the desired bounds
Fine-tuning of control parameters in field operation is rather complex and risky; however, with an optimized control system that has been verified in a virtual safe environment the next step is to proceed with updating the controller of the real plant.
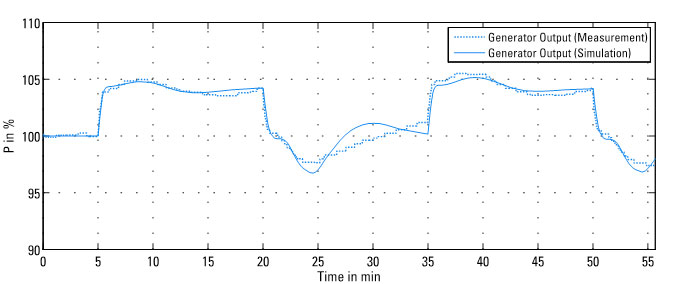
With the new optimized controller, the large-scale plant has improved its primary control reserve fulfilling tougher grid code requirements and thereby improving the quality and robustness of the Germany electric energy system. With a more stable grid, it is possible to have a higher penetration of fluctuation energy sources such as wind and solar.
This research demonstrates the necessity of model-based development where new optimized strategies can be developed and tested during various operating conditions in a safe-virtual environment.
References
https://www.modelon.com/blog/articles/new-solution-for-thermal-power-plant-start-up-optimization/
M. Hübel, A. Berndt, M. Meinke und E. Hassel, „Modelling a Lignite Power Plant in Modelica to Evaluate the Effects of Dynamic Operation and Offering Grid Services,“ in 10th International Modelica Conference, Lund, 2014.
M. Hübel, S. Meinke, E. Hassel und J. Nocke, „dentification of Energy Storage Capacities within large-scale Power Plants and Development of Control Strategies to increase marketable Grid Services,“ in ASME Power and Energy Conversion Conference, San Diego, 2015.