ASME POWER 2023
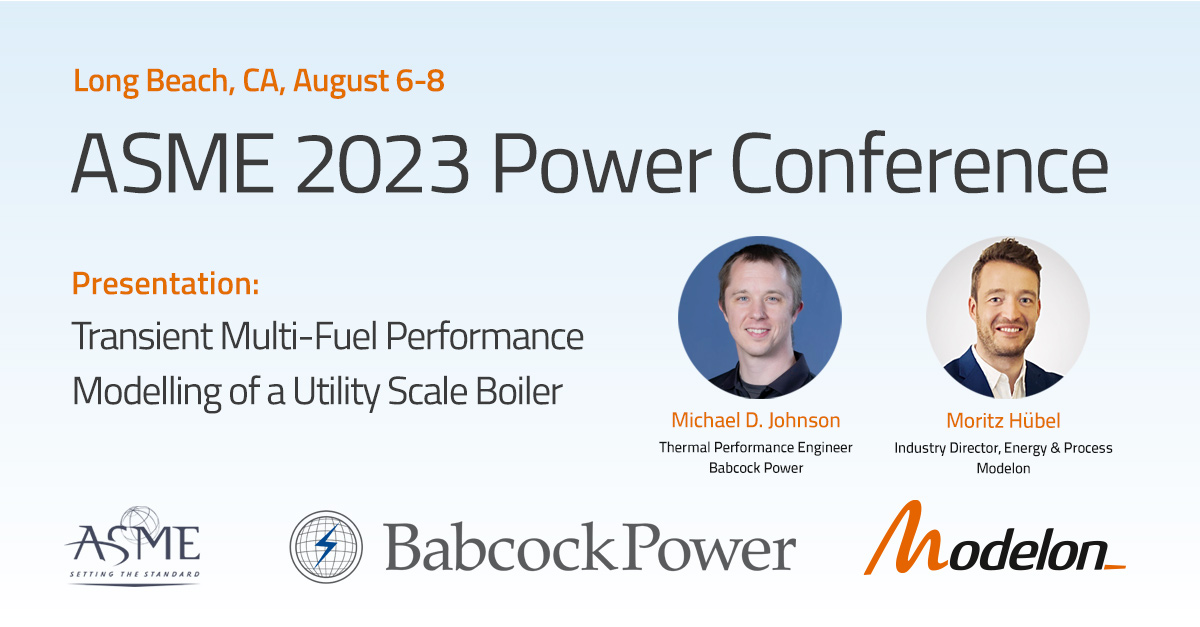
Modelon will present alongside Babcock Power at the upcoming ASME POWER 2023 conference in Long Beach, California. ASME POWER 2023 is an event that brings together power generation professionals working in industry, research, and academia to discuss current power industry issues, applications, and emerging technologies.
Michael Johnson, Thermal Performance Engineer at Babcock Power will be joined by Moritz Hubel, Industry Director of Energy & Process at Modelon to present “Transient Multi-Fuel Performance Modeling of a Utility Scale Boiler”. This will be presented in the “Experimental and Computational Fluid Dynamics and Thermal Hydraulics and Data Analytics” session. Below you will find the abstract of the presentation.
Presentation Abstract:
Traditional analysis of heat transfer within a boiler has generally focused on steady-state operation. This analysis predicts temperatures, mass flow rates, and other elements of the design at a specific set of boundary conditions. This is well suited to base-loaded units, but recently additional focus has been placed on load following units that may change load routinely. In this case, a dynamic model capable of capturing transient effects throughout a load ramp is necessary to provide the best information on how the boiler and equipment will respond to the change in conditions over time.
Riley Power Inc has worked with Modelon to develop transient capable modeling tools for a complete boiler (furnace through air preheater). The components developed include both heated pressure parts as well as external piping and consider both radiant and convective heat transfer as appropriate. Limited control systems have been incorporated to mimic boiler and burner management systems to the extent required. These include firing rate controls, feedwater controls, spray controls, turbine throttle controls, and airflow rate controls to allow the system to achieve the full range of desired loads and boundary conditions.
These tools were used to model an existing utility boiler for which substantial operating data was available for comparison. This model was tuned to match the operating data at full load conditions, and then the boundary conditions were varied to mimic ramping cases extracted from the real world data. Results of these simulations were then compared to the data to confirm accuracy.
Once adequately tuned this model can then be used to predict future behavior of the system under new conditions. This may be a fuel change, such as conversion from coal to gas, or fuel blending, such as co-firing gas with hydrogen. Alternatively, the model can consider changes to excess air, flue gas recirculation (if applicable), or other operator adjustments to determine optimum operating conditions across the load range.
This analysis allows examination in detail of transient behavior of specific components of the boiler, such as metal temperatures, which are a limiting factor in allowable ramp rates. This is particularly important in thick walled components such as drums and headers, where a high rate of change in temperature may lead to stress cracking or fatigue at nozzles or other connections. Additionally, the model can be configured to provide warnings or alerts if high metal temperatures that may exceed allowable stresses are detected at any point during a transient. Results of these models will provide valuable information to asset owners/operators with respect to optimizing operations and maintenance strategies and asset value within their generating fleet.
Presenting Author: Michael D. Johnson Babcock Power