Gas Exchange and Exhaust Condition Modeling of a Diesel Engine using the Engine Dynamics Library
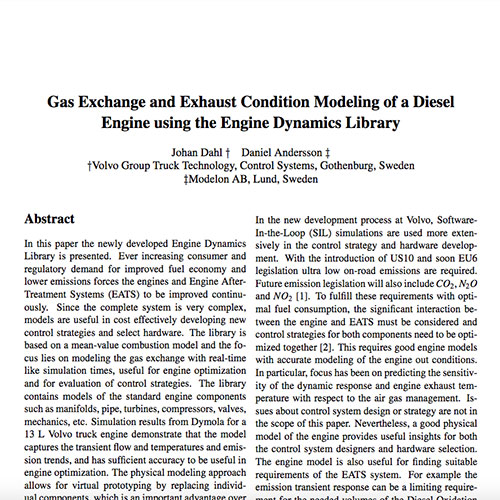
DAHL, J., ANDERSSON, D.
SEPTEMBER 3, 2012
Proceedings of the 9th International Modelica Conference
Munich, Germany, pp. 101-113
Introduction
As the requirements on the engine and EATS become more strict, a new development process of control strategies and hardware concept selection is needed as
only using engine test cells and vehicles in the development process is too time consuming and expensive. In the new development process at Volvo, Software-In-the-Loop (SIL) simulations are used more extensively in the control strategy and hardware development. With the introduction of US10 and soon EU6 legislation ultra low on-road emissions are required. Future emission legislation will also include CO2, N2O and NO2[1]. To fulfill these requirements with optimal fuel consumption, the significant interaction between the engine and EATS must be considered and control strategies for both components need to be optimized together [2]. This requires good engine models with accurate modeling of the engine out conditions. In particular, focus has been on predicting the sensitivity of the dynamic response and engine exhaust temperature with respect to the air gas management. Issues about control system design or strategy are not in the scope of this paper. Nevertheless, a good physical model of the engine provides useful insights for both the control system designers and hardware selection. The engine model is also useful for finding suitable requirements of the EATS system. For example the emission transient response can be a limiting requirement for the needed volumes of the Diesel Oxidation Catalyst (DOC), Diesel Particulate Filter (DPF) and Selective Reduction Catalyst (SCR) in order to fulfill the EU6 emission legislation.