クレーンシステム内での油圧の簡単な統合
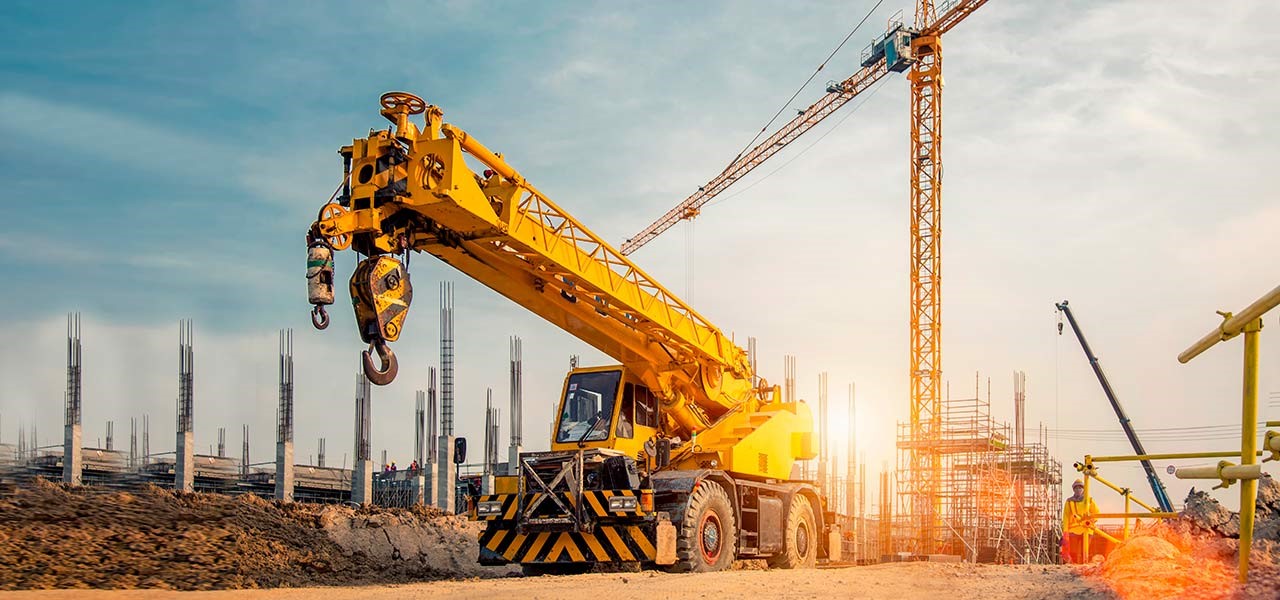
When trying to integrate hydraulics within a system, simulation tools can be a huge asset to system engineers by saving them time during the design and testing phases. But what happens when those same tools require a steep learning curve to use effectively? Today’s system engineers don’t have the time to use cumbersome technology for prototyping a hydraulic system into a simulation model and extract usable information. This creates a need for easy-to-use simulation technology that enables engineers to create quick system models which will return dependable results.
Modelon libraries, such as the Modelon Hydraulics Library, are comprehensive and easy-to-use Modelica based libraries that come with out-of-the-box components for quick system modeling. For modeling hydraulics systems, the Modelon Hydraulics Library is an ideal library solution as it comes with ready-to-use models including pumps, restrictions and valves, hydraulic lines etc., that can be plugged into an existing model for simulation. But just how easy is it to use the Modelon Hydraulics Library for accurate system simulation?
In this blog, we design a crane system where the boom is hydraulically actuated by the operator to pick up and move objects. The Modelon Hydraulics Library is used to model and simulate the boom and other hydraulic components of the proposed system to give us an understanding of how the crane will work in real life.
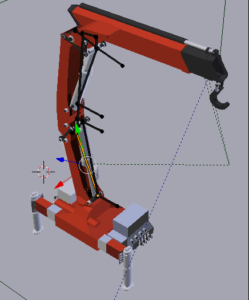
Model creation process
To start, we first need to model a mechanical structure for our crane. In this case, the mechanical structure is simply the booms and the joints that connect them. Our current system has three booms and two joints, where the base boom is assumed to be fixed. We can model this structure very easily using the Modelica Standard Library’s multibody components, a free standard library developed by The Modelica Association. A visual of this system is created automatically using dxf files of each mechanical component (see top half of Figure 2).
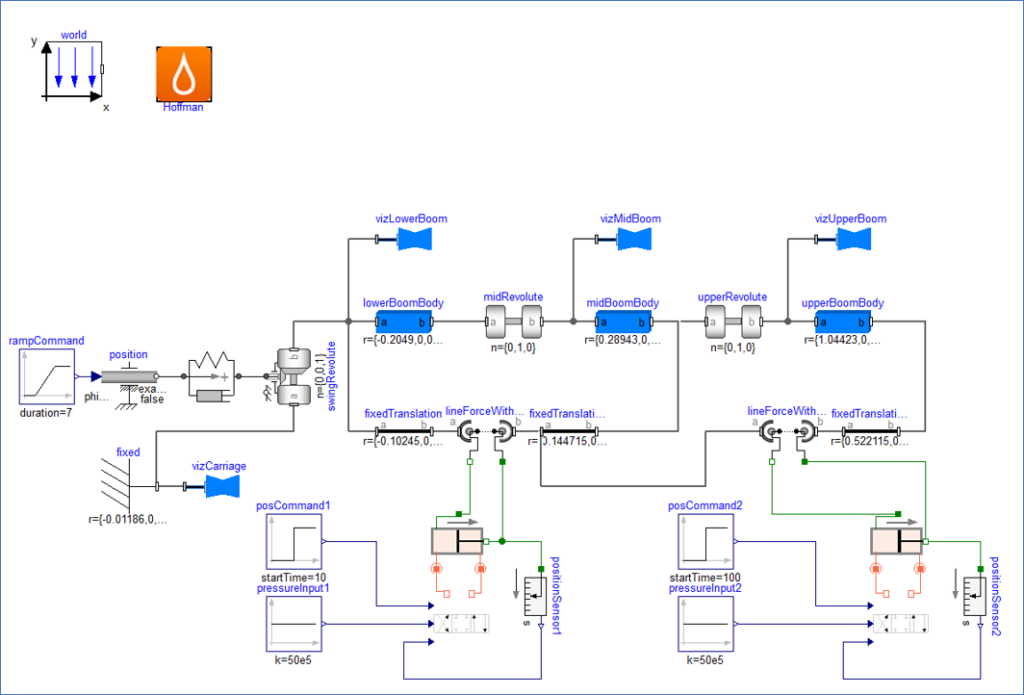
After we’ve modeled the mechanical structure of the crane, it’s time to model the hydraulic system. The hydraulic system holds and actuates the boom to achieve the required motion of the crane. In our model, the hydraulic jack and servo valve makes up the hydraulic system, where the servo valve controls the hydraulic fluid supply, pressure, and movement of the system. Our hydraulic system should aim to have a high-pressure supply line and a low pressure return line.
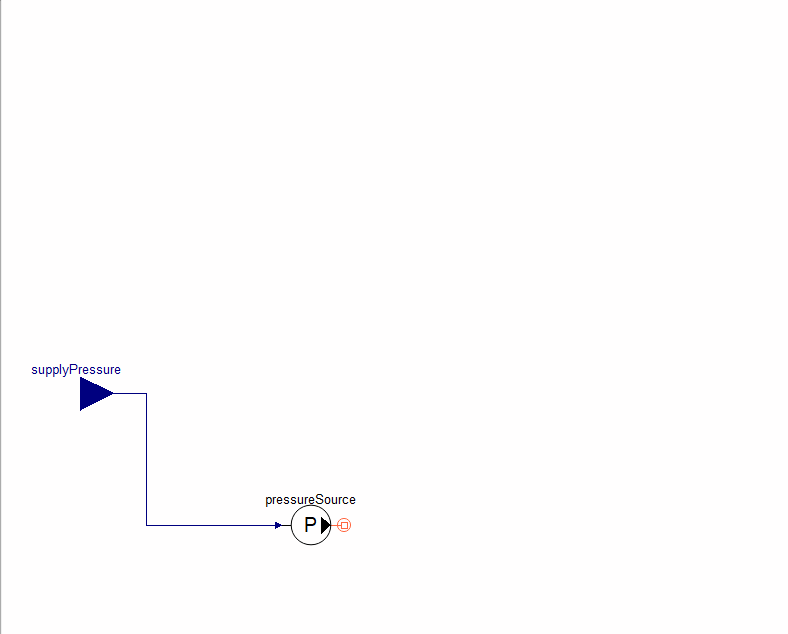
While modeling this hydraulic system may seem complicated, the configuration is quite easy with off-the-shelf component models of the hydraulic jack and servo that come with Modelon’s Hydraulic Library. By simply dragging and dropping component models into various configurations, users can easily simulate the hydraulic system that is just right for their application (See Figure 3). Additionally, the off-the-shelf components within Modelon’s Hydraulic Library are easy to parameterize, needing only the minimum set of data points like geometry, hydraulic fluid property etc. This allows users to quickly set up their hydraulic systems and prepare them for simulation.
Simulation and Analysis
Now that we have our model, it’s time to simulate it. Each model can be given a set of inputs to observe accurate behaviors of the system. To observe the motion of the boom in our crane system, we would input a position command for each individual actuator. The controller model will ensure the jacks extend or retract only as a result of those commands. In some cases, numerical results can be hard to visualize for such a simulation. However, the following animation shows the possibility of visualizing system behavior.
Additional Benefits of the Modelon Hydraulics Library
The value of the Modelon Hydraulics Library is realized by hundreds of companies and users worldwide. Customers of varying industries, like aerospace R&D teams and automotive OEMs, use the Modelon Hydraulics Library to model entire gas turbine fuel control systems, transmission systems, brake system models, and more.
The Modelon Hydraulics Library also enables users to select hydraulic components with the correct sizing; something that can be hard to determine without accurate simulation tools. The sensitivity of the system to supply pressures can be studied using the library, which is a major aspect in sizing and designing the power pack for such systems. Additionally, the ability to model and simulate hydraulic systems also helps companies troubleshoot erroneous behaviors of their design, saving both the time and money to adjust a physical prototype.
To learn how to leverage the capabilities of Modelon’s Hydraulics Library for your systems, visit the Modelon Hydraulics Library product page or contact us below to talk to our experts for an in-depth solution.